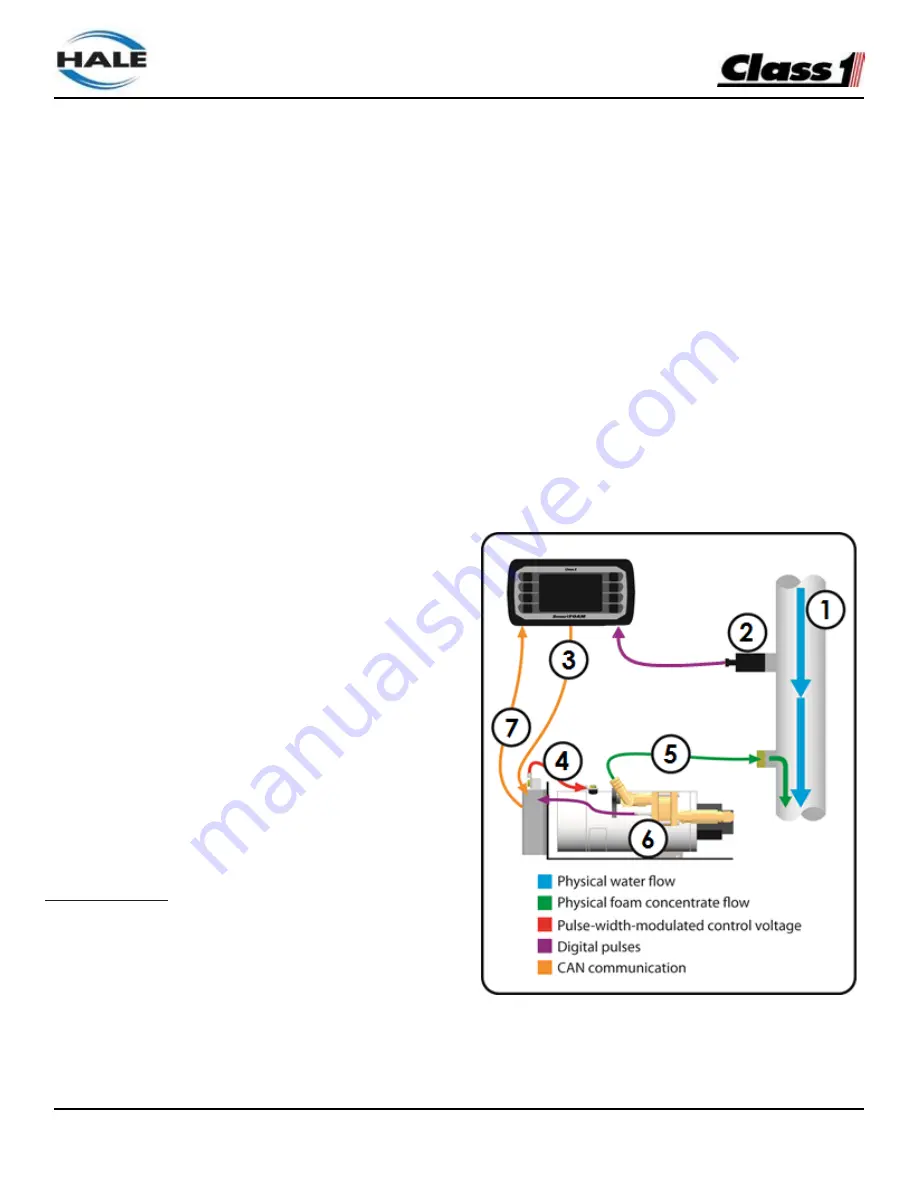
FoamLogix, Model 2.1A and 1.7AHP Class
“A”
Electronic Foam Proportioning Systems
71
SECTION 6 TROUBLESHOOTING
USER DIAGNOSTICS
Diagnostic LED indicators are provided on the distribution
box and on the feedback sensor. The LED on the feedback
sensor flashes when the sensor is receiving pulses from the
flow sensor rotor targets. These LEDs help to ease tracing of
power supply faults and eliminates some of the guesswork
in troubleshooting. If the system malfunctions make sure the
following conditions are checked:
❑
All hose connections are correct and tight (Refer to
appropriate system plumbing diagram in the
INSTALLATION section).
❑
All electrical connections are correct and tight (Refer
to appropriate system electrical diagram in the
INSTALLATION section).
❑
Apparatus electrical system energized with power
supplied to pump panel and Hale Foamlogix
controller.
Once the above conditions are met, proceed to the system
troubleshooting section to determine the cause of the
malfunction.
Hale Foamlogix systems consist of individual subsystems
working together to provide finished foam solution at the
proper percentage. Also see the SYSTEM OVERVIEW
section.
The system is designed using modular components making
troubleshooting and repair easier. Each subsystem has its
own set of troubleshooting procedures. The procedures that
follow provide a logical flow path to isolate and correct a
system failure.
Note: Hale
Foamlogix
system electronic components have
no user serviceable components inside and are replaced as
a unit. Opening of Hale
Foamlogix
electronic components
voids the manufacturer warranty.
System Overview
The Foamlogix proportioner is a closed-loop system. The
“brain” behind the system is the computer-controlled
Foamlogix Controller Display. A basic understanding of how
the system functions makes troubleshooting easier (refer to
Figure 1
: Closed Loop Control Diagram
while reading the
following control steps).
1. Water flows through the discharge manifold and past
the water flow sensor spinning its paddlewheel.
2. The water flow sensor sends the raw digital pulses
to the Foamlogix controller display.
3. The Foamlogix controller display calculates the
desired foam flow rate based on the water flow rate
and the currently set foam concentrate percentage.
The Foamlogix controller display transmits a
requested motor rate (0% to 100%) to the
distribution box via CAN communication.
4. The distribution box sends pulse-width-modulated
control voltage (0% to 100%) to the motor which
turns the pump at the desired speed.
5. The pump begins discharging foam concentrate into
the discharge manifold where it mixes with the
water.
6. The foam sensor detects the foam concentrate
flowing past the target rotors and sends the raw
digital pulses to the distribution box.
7. The distribution box sends the foam flow rate to the
Foamlogix controller display where it is evaluated
and the process starts again at step 1.
Figure 1
: Closed Loop Control Diagram
Note: The
Foamlogix
system has a simulated flow function
described in the SIMULATED FLOW OPERATION section.
This allows troubleshooting without flowing water yet
simulates an actual water flow.
Summary of Contents for FoamLogix 1.7AHP
Page 4: ...FoamLogix Model 2 1A and 1 7AHP Class A Electronic Foam Proportioning Systems 4 NOTES...
Page 10: ...FoamLogix Model 2 1A and 1 7AHP Class A Electronic Foam Proportioning Systems 10...
Page 14: ...FoamLogix Model 2 1A and 1 7AHP Class A Electronic Foam Proportioning Systems 14 NOTES...
Page 28: ...FoamLogix Model 2 1A and 1 7AHP Class A Electronic Foam Proportioning Systems 28 NOTES...
Page 52: ...FoamLogix Model 2 1A and 1 7AHP Class A Electronic Foam Proportioning Systems 52 NOTES...
Page 68: ...FoamLogix Model 2 1A and 1 7AHP Class A Electronic Foam Proportioning Systems 68 NOTES...
Page 79: ...NOTES FoamLogix Model 2 1A and 1 7AHP Class A Electronic Foam Proportioning Systems 77...