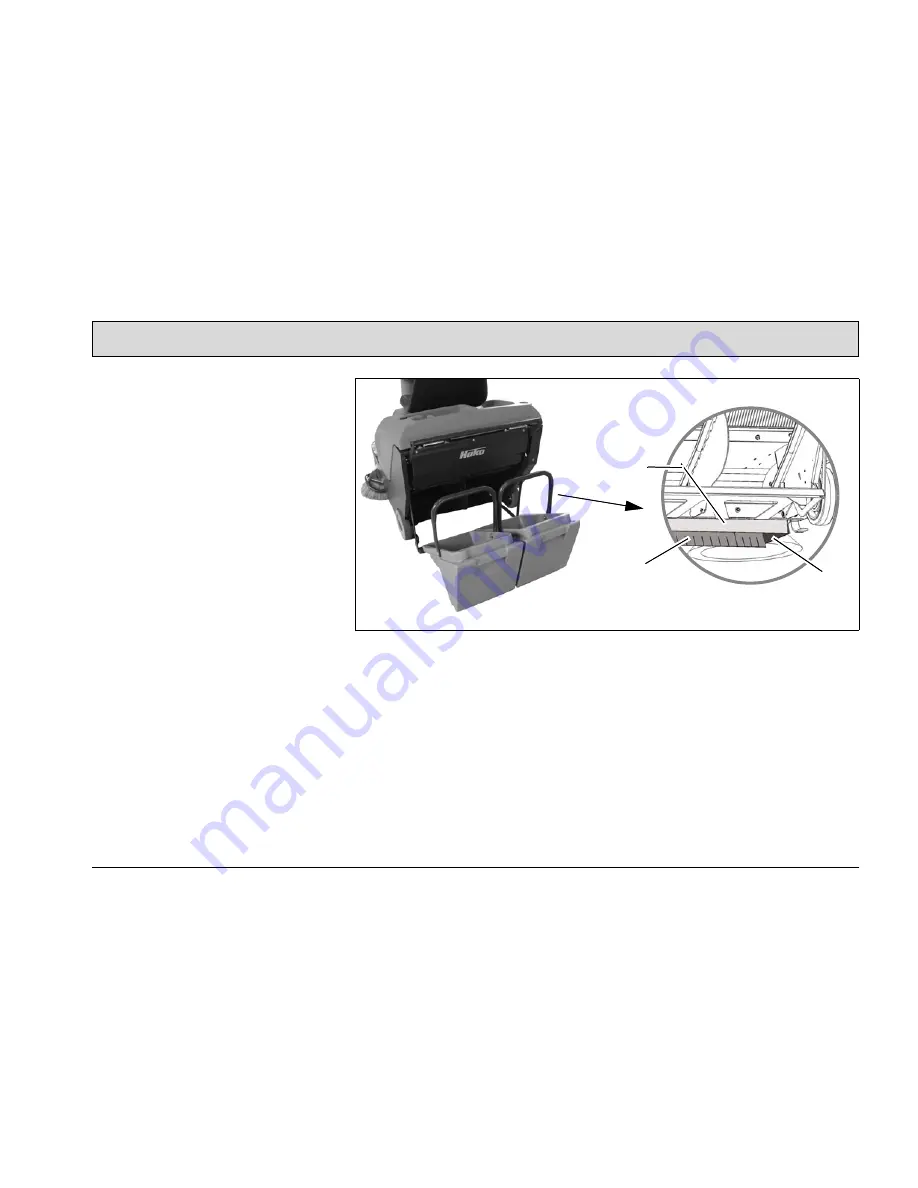
57
Maintenance and Service
5.6.4 Changing the sealing strips in
the broom space
The broom space is sealed by means of
four sealing strips. Check the four seal-
ing strips on a weekly basis and change
them in the case of wear.
1. Switch the vehicle off using the key
switch and secure with the parking
brake.
2. Remove the screws connecting the
sealing strips (Fig. 22/1 to 3).
3. Assemble the new sealing strips and
set a distance of 1 - 2 mm to the
floor.
Fig.22
1 Sealing strip, front (folding apron)
2 Sealing strip, rear
3 Sealing strips, right and left
2
1
3