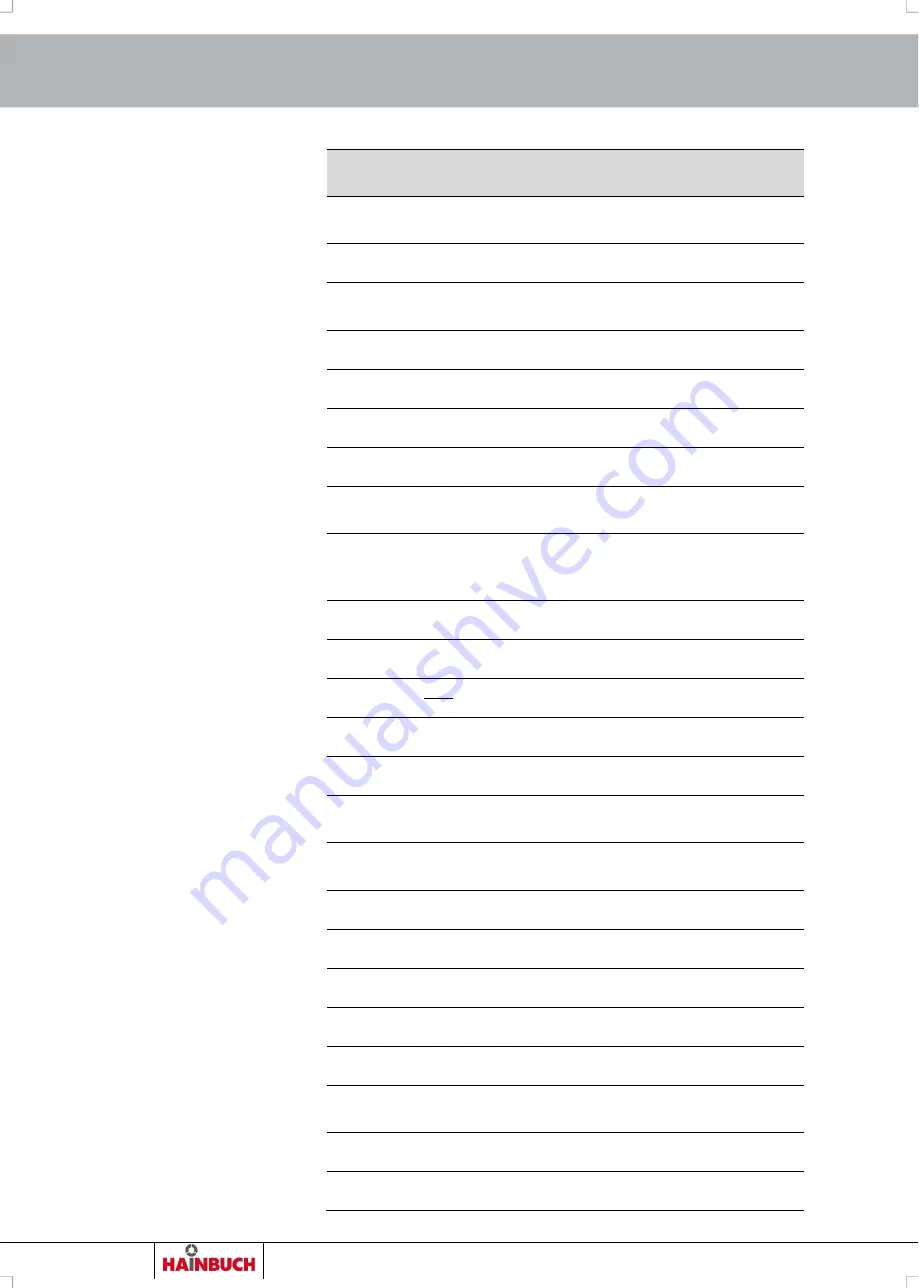
HYDROK
Use and limits of use
34
Order h49 7144.907-333
Brief des-
ignation
Unit
Explanation
𝑓
𝑓𝑧
𝑁
Clamping force supplement for rotational
compensation
𝐹
𝐺
𝑁
Density of workpiece
𝑓
𝑛
𝑚𝑚
Feed / rotational movement of drilling op-
eration
𝐹
𝑞
𝑁
Transverse force
𝐹
𝑞 𝑚𝑎𝑥
𝑁
Maximum permitted transverse force
𝐹
𝑟𝑎𝑑
𝑁
Radial clamping force
𝐹
𝑟𝑎𝑑 𝑒𝑟𝑓
𝑁
Required radial clamping force
𝐹
𝑠𝑘
𝑁
Clamping force to prevent the workpiece
getting levered out
𝐹
𝑠𝑧
𝑁
Clamping force to absorb the machining
forces and torques during turning and/or
drilling operations towards the chuck axis
𝐹
𝑡
𝑘𝑁
Tailstock force
𝐹
𝑡 𝑚𝑎𝑥
𝑘𝑁
Maximum tailstock force
𝑘
𝑐
𝑁
𝑚𝑚
2
Specific cutting force
𝐿
𝑚𝑚
Total chuck length
𝐿
𝑎
𝑚𝑚
Unclamping length
𝐿
𝑔
𝑚𝑚
Center of gravity distance between
»Workpiece - clamping point«
𝐿
𝑞
𝑚𝑚
Distance, »radial bore machining - clamp-
ing point«
𝐿
𝑠𝑝
𝑚𝑚
Clamping length
𝐿
𝑠𝑝 𝑚𝑖𝑛
𝑚𝑚
The minimum clamping length required
𝐿
𝑠𝑝 𝑣
𝑚𝑚
Total clamping length
𝐿
𝑤
𝑚𝑚
Workpiece length
𝐿
𝑣
𝑚𝑚
Clamping head, front-end length
𝐿
𝑧
𝑚𝑚
Distance between »Machining point -
clamping point« when turning
𝑚
𝑘𝑔
Mass of the clamping head
𝑀
𝐵
𝑁𝑚𝑚
Drilling operation torque