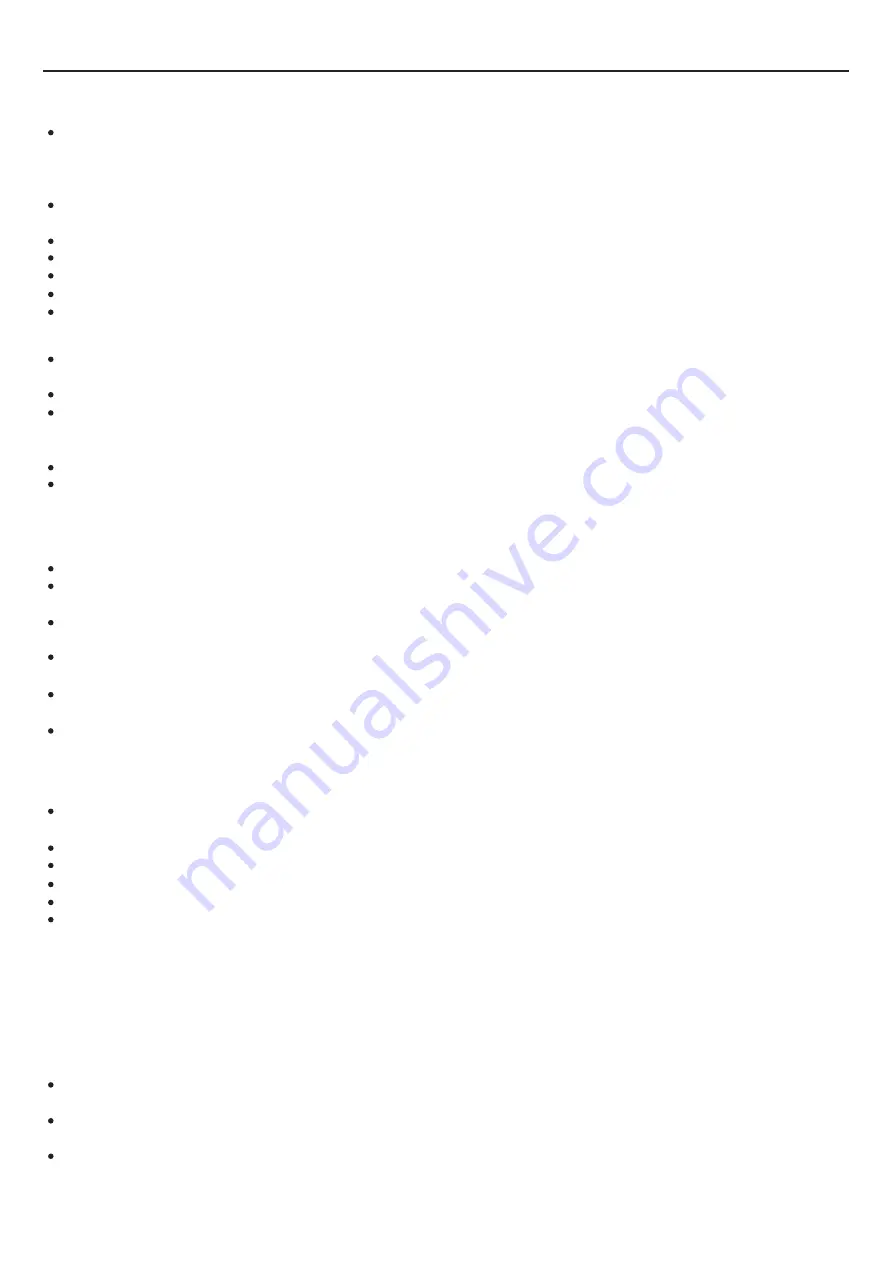
Maintenance Items
Maintenance Requirements
Maintenance of Electrical Components
Maintenance of Intrinsically Safe Elements
Removal and Vacuumizing
Welding
10
Before the refrigeration system is operated, the circulating system shall be cleaned with nitrogen. Afterwards, the outdoor
unit shall be vacuumized, the duration of which cannot be less than 30 minutes. Finally, 1.5~2.0MPa OFN shall be used for
nitrogen flushing (30 seconds~1 minute), to confirm the position requiring treatment. Maintenance of the refrigeration system
is only allowed after the residual gas of flammable refrigerant is removed.
During the use of refrigerant charging tools, cross contamination of different refrigerants shall be avoided. The total length
(including the refrigerant pipelines) shall be shortened as much as possible, to reduce the residual of refrigerant inside.
The cylinders of refrigerant shall be kept upright, and be fixed.
Before refrigerant charging, the refrigeration system shall be earthed.
The refrigerant charged shall be of the type and volume specified on the nameplate. Excessive charging is not allowed.
After maintenance of the refrigeration system, the system shall be sealed with a safe manner.
The maintenance in progress shall not damage or lower the original class of safety protection of the system.
Partial of the electrical component under maintenance shall be subject to inspection on refrigerant leakage with dedicated
leak detection equipment.
After the maintenance, the components with safety protection functions cannot be disassembled or removed.
During the maintenance of sealing elements, before opening the seal cover, the air conditioner shall be powered off first.
When power supply is required, continuous leak detection shall be carried out at the most dangerous position, to avoid potential
risks.
During maintenance of electrical components, the replacement of enclosures shall not affect the level of protection.
After maintenance, it shall be guaranteed that the sealing functions will not be damaged or the sealing materials will not
lose the function of preventing the entry of flammable gas due to aging. The substitute components shall meet the recommended
requirements of the air conditioner manufacturer.
The intrinsically safe element refers to the components working continuously inside flammable gas without any risks.
Before any maintenance, leak detection and inspection on earthing reliability of the air conditioner must be carried out, to
ensure no leakage and reliable earthing.
In case the allowable voltage and current limit may be surpassed during the service of the air conditioner, any inductance or
capacitance cannot be added in the circuit.
Only the elements appointed by the air conditioner manufacturer can be used as the parts and components replaced, or
otherwise a fire or explosion
may be triggered in case of refrigerant leakage.
For the maintenance not involved in system pipelines, the system pipelines shall be well protected, to ensure that no
leakage will be caused due to maintenance.
After maintenance and before test run, the air conditioner must be subject to leak detection and inspection on earthing
reliability with leak detection equipment or leak detecting solution. It shall be guaranteed that the startup inspection is carried
out without leakage and under reliable earthing.
The maintenance or other operations of the refrigeration circuit shall be made as per conventional procedures. Moreover,
the flammability of refrigerant shall also be mainly considered. The following procedures shall be followed:
Refrigerant cleaning;
Pipeline purification with inert gas;
Vacuumizing;
Pipeline purification again with inert gas;
Pipeline cutting or welding. The refrigerant shall be recovered to a proper cylinder. The system shall be purged with OFN, to
ensure safety. The step above may need to be repeated for several times. Compressed air or oxygen cannot be used for
purging.
In the course of purging, OFN shall be charged inside the refrigeration system under vacuum state, to reach the operating
pressure. Afterwards, the OFN shall be discharged to the atmosphere. Finally, the system shall be vacuumized. The step above
shall be repeated until all the refrigerants in the system are cleared. The OFN charged for the last time shall be discharged to
the atmosphere. Afterwards, the system can be welded. The operation above is necessary in case of pipeline welding.
It shall be guaranteed that no alight fire source is around the outlet of the vacuum pump and the ventilation is favorable.
Favorable ventilation must be guaranteed in the maintenance area. After the maintenance machine is subject to the
vacuumizing above, the system refrigerant can be discharged on the outdoor unit side.
Before the outdoor unit is welded, it must be guaranteed that no refrigerant is inside the outdoor unit and the system
refrigerant has been discharged and cleared.
The refrigeration pipelines cannot be cut with a welding gun under any circumstance. The refrigeration pipelines must be
disassembled with a pipe cutter, and the disassembly must be carried out around a ventilation opening