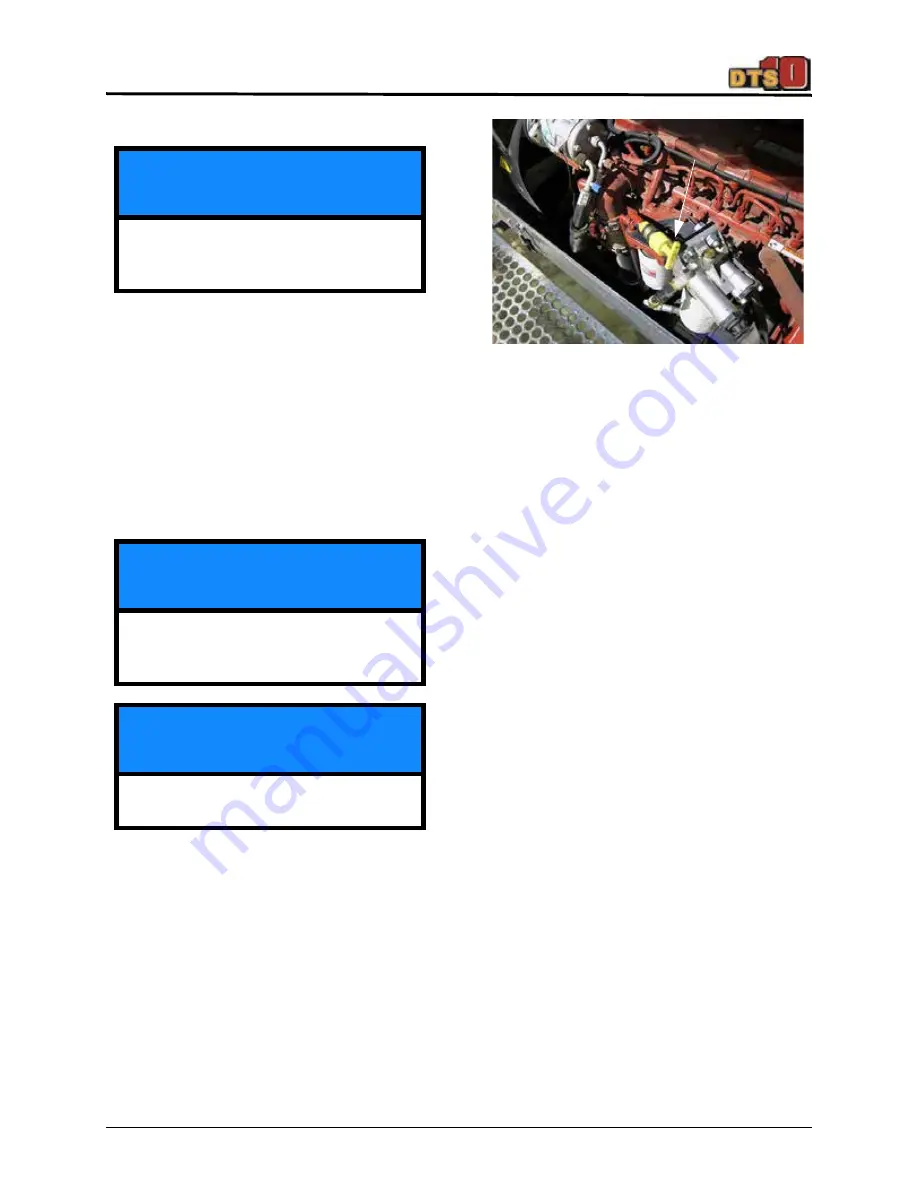
SECTION 8 –
MAINTENANCE AND STORAGE
8-3
General Maintenance
If your machine is going to sit unused for
an extended period of time, occasionally
rotate the wheel hubs by driving the machine
forward and backward - at least half of a tire
rotation to adequately coat all internal wheel
hub parts. This will prevent rusting if
moisture inadvertently entered the wheel hub
during an oil change.
Engine Oil
The Engine Oil Dipstick is located on the
left-hand side of the engine. Wait at least five
(5) minutes after shutting the engine off to
check the oil level.
NOTE: Check the engine oil level daily.
Capacity
•
Engine Oil Dipstick Capacity (low to
high mark) = 2 quarts (1.9 L)
•
Engine Oil Pan Capacity (including fil-
ter) = 17 quarts (16.1 L)
Type
•
Valvoline Premium Blue® Classic
Engine Oil - 15W-40 (recommended)
NOTE: Change the engine oil every 250
hours of operation or yearly,
whichever occurs first.
Engine Oil Fill
Engine oil can be added through the
Engine Oil Fill Port or the Remote Engine Oil
Fill Port (both located on the left-hand side of
engine).
NOTICE
Failure to rotate the wheel hub and
disperse oil may cause rusting and
internal wheel hub damage.
NOTICE
Never operate the engine with oil level
below the “L” (low) mark or above the “H”
(high mark) on the engine oil dipstick.
NOTICE
The engine must be level when checking
the oil level to ensure accuracy.
Engine Oil Dipstick
(Located on the left-hand side of engine)
-Typical View
Summary of Contents for DTS 10
Page 122: ......