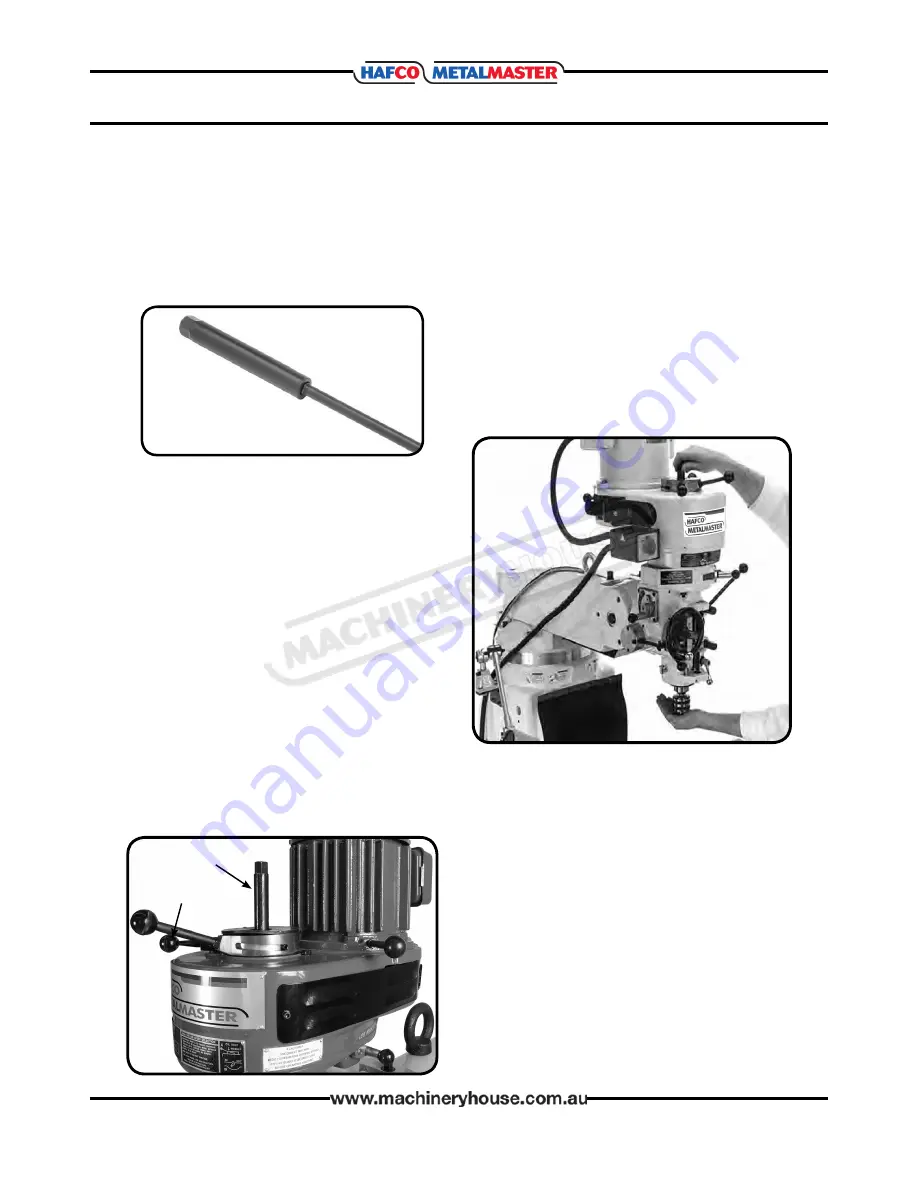
21
OPERATION MANUAL
LOADING & UNLOADING TOOLING
These mills are equipped with a NT-30 spindle
taper (BM-23A) with an 12mm drawbar and a
NT-40 spindle taper (BM-53VE, BM-63VE) with
a M16 spindle drawbar (Fig. 17)
Drawbar Upper
Portion
Fig. 17
Loading Tooling
1. DISCONNECT MILL FROM POWER!
2. Clean any debris or surface substances
from inside the spindle taper and the
mating surface of the tooling.
NOTE:
Debris or oily substances can prevent
the tooling and spindle from properly
mating. This condition can cause excessive
vibration, poor cutting results, or tool/work-
piece damage.
3. Place the mill in the low spindle speed
range to keep the spindle from turning
or use the spindle brake in the next
steps. (B of Fig. 18)
4. With one hand holding the tool in place,
insert the drawbar into the spindle from
the top of the head, then thread it into
the tool (see A of Fig. 18)
A
B
Fig. 18
5. Tighten the drawbar until it is snug. Avoid
overtightening, as this could make removing
the tool difficult
UNLOADING TOOLING
1. DISCONNECT THE MILL FROM POWER!
2. Place the mill in the low spindle speed
range to keep the spindle from turning
in the next step.
3. Loosen the drawbar a couple of turns,
then tap the top of it with a brass hammer
to knock the tool loose at the bottom of
the spindle.
4. Support the tool with one hand, then
completely unthread the drawbar from
the tool.
Fig.19
NOTE:
Make sure that the drawbar has at
least three threads engaged with the tooling
in the next step to avoid damaging the
threads of the drawbar or tool.
Page 21
Instructions Manual for BM-23A (M595D)
12/02/2018