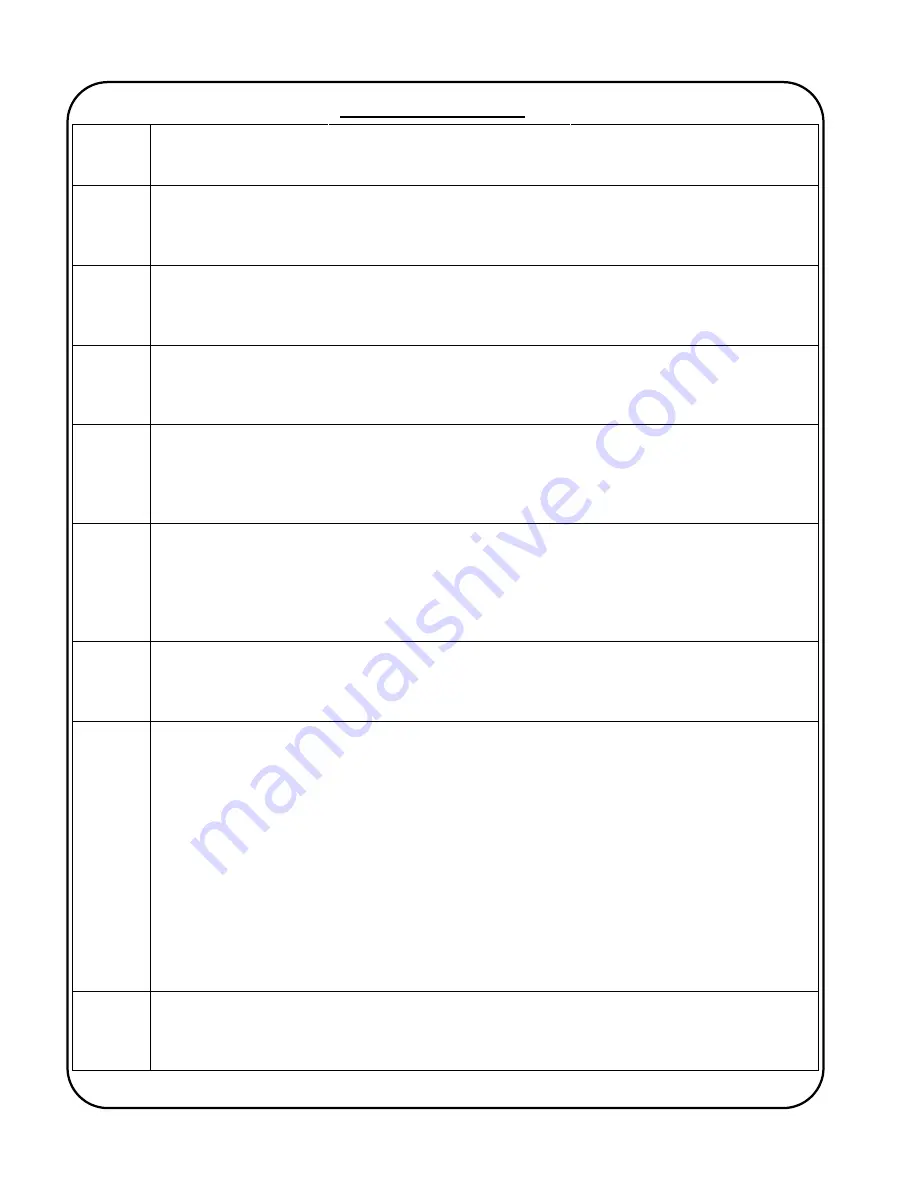
T-2
LED
Flash
Rate Reason
4
Flashes
every 2
seconds
Normal Closed Loop Operation - No problems detected.
24
Flashes
every 2
seconds
Open Loop Operation - No problems detected which would prevent the motor from running
safely, however a travel speed encoder has not been detected and as such the control will
run in open loop mode. The speed regulation is not as accurate in open loop mode.
1 Flash
every 2
seconds
The “GSP-1100” control was set to run when electrical power was initially supplied to the
control (powered-up). To prevent unexpected motion generated from the “GSP-1100”
control, the motor output is disabled and the LED blinks once every two seconds until the
control is reset by being placed in “Hold” (stop) mode.
2
Flashes
every 2
seconds
The current draw of the motor exceeded that permissible (set by the “Current Limit”
potentiometer VR2), resulting in the termination of motor output from the control. Rectify
the fault causing the excessive current draw, or increase the value of the “Current Limit”
potentiometer
- only if it is set too low
. Then reset the “GSP-1100” control by either
powering-down the control, or by placing the control in “Hold” (stop) mode.
3
Flashes
every 2
seconds
A motor travel speed encoder was detected on power-up, but is no longer recognized,
resulting in the termination and/or prevention of motor output from the control. Rectify the
encoder problem then, reset the “GSP-1100” control by placing the control in “Hold” (stop)
mode. Note: If the power is turned off then back on again without rectifying the encoder
fault, the control will not detect the encoder on power-up and will only operate in open-loop
mode (NO CLOSED-LOOP SPEED REGULATION).
4
Flashes
every 2
seconds
A motor travel speed encoder is detected on, but no encoder pulses are received from it
during a two second period of the motor output being energized, resulting in the
termination of motor output from the control. Rectify the encoder problem then, reset the
“GSP-1100” control by placing the control in “Hold” (stop) mode.
5
Flashes
every 2
seconds
As port “CN12” is usually used to provide an external “Hold” (stop) command, wiring
should run from pin 1 of this port, up to the external device and then back to pin 3, thereby
closing the circuit between pins 1 and 3 whenever connected. Each time the “GSP-1100”
control is powered-up, it checks the status of pins 1 & 3 of “CN12” and if closed circuit, the
control will continue to monitor their status as well as the status of pin 2 with respect to pin
1 (if pin 1 & 3 were open circuit on power-up, the control ignores all signals for port
“CN12”). Once the “GSP-1100” control has recognized a device was connected to “CN12”
but is no longer connected (i.e. pins 1 & 3 change from closed circuit to open circuit), the
motor output is disabled and the LED blinks five times every two seconds. Rectifying the
fault and resetting the “GSP-1100” control by placing the control in “Hold” (stop) mode, will
clear the error.
Note: turning the power to the “GSP” control off, waiting ten (10)
seconds then re-applying the power will clear the error, but if the circuit between pin
1 & 3 remains open, all signals coming into “CN12” will be ignored (failing to
recognize external “Hold” commands).
6
Flashes
every 2
seconds
The GSP-1100 has recognized that a remote speed adjustment potentiometer is
connected to port “CN14”.
Diagnostic LED Table
Summary of Contents for , GPP-200
Page 2: ......
Page 6: ...4 GENERAL DIMENSIONS...
Page 13: ...11 WELDING POSITIONER PARTS BREAKDOWN DRAWING GP 200...
Page 15: ...13 WELDING GAS PURGE POSITIONER PARTS BREAKDOWN DRAWING GPP 200...
Page 23: ......
Page 24: ...www GULLCO com...
Page 26: ......
Page 35: ...T 9 GSP 1100 CONTROL ASSEMBLY BREAKDOWN SEE NOTES...
Page 36: ...T 10 GSP 1100 CONTROL CIRCUIT BOARD SCHEMATIC DRAWING G1100 RB REV B...
Page 38: ...www GULLCO com...