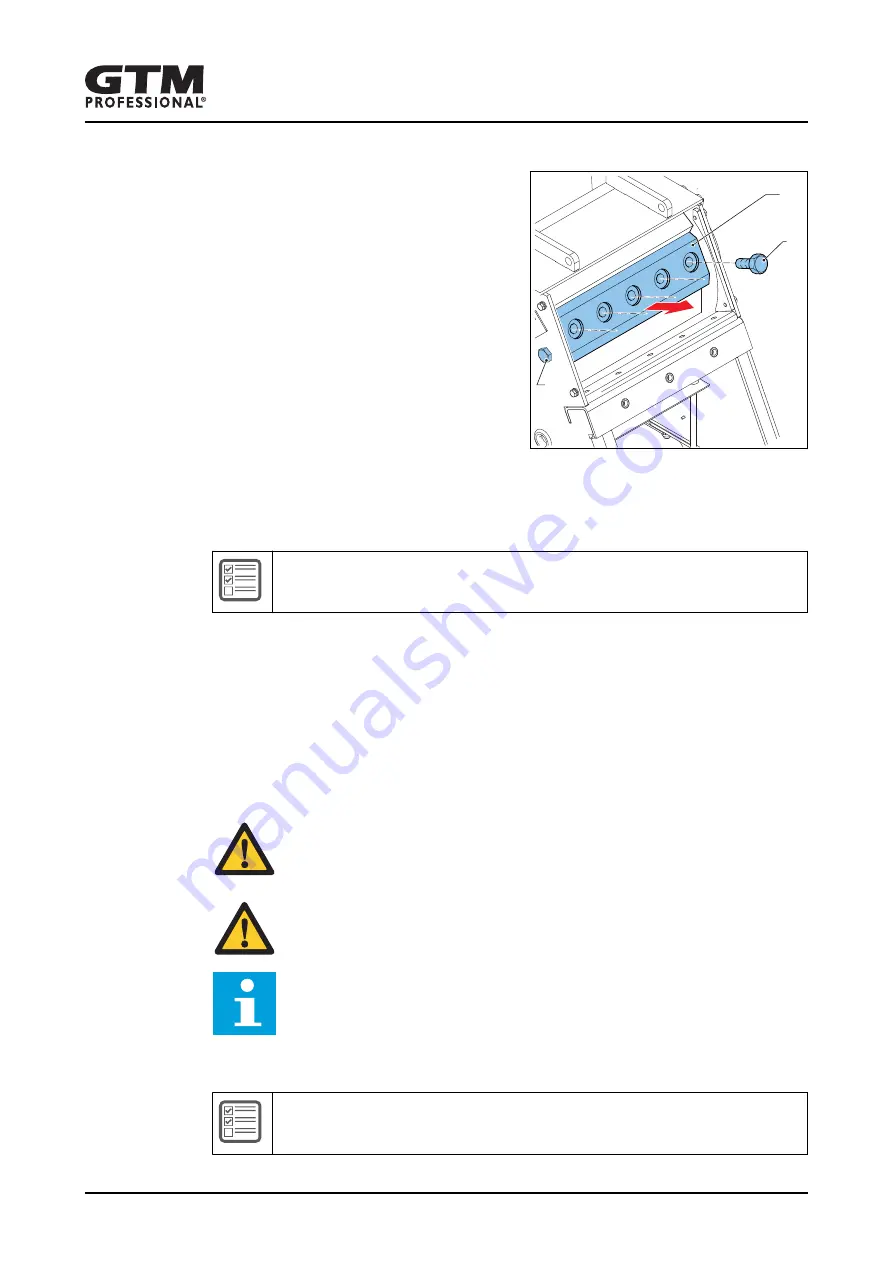
Procedure
1. Remove the bolts (5x) (A).
2. Remove the blade (B).
3. Remove the locking bolt (C).
4. Repeat the procedure for the second
blade.
7.1.3
Turn the blades
If one side of the blade is dull, you can turn the blade around to the sharper side.
Preliminary requirements
1.
The blades are removed.
Procedure
1. Clean the surface of the blade and the blade holder.
2. Turn the blade around to the sharper side.
3. Repeat step 1 and step 2 for the second blade.
4. If both sides of the blade are dull, sharpen or replace the blade. Refer to section
.
5. Install the blades. Refer to section
7.1.4
Sharpen the blades
Warning:
Do not sharpen a damaged blade.
Caution:
Make sure that the blade doesn't become overheated during sharpening. This
can cause damage to the steel.
Note:
•
Blades must be sharpened by a professional.
•
A blade can be sharpened 0,5 mm to a maximum of 3 times. After that,
the blade has to be replaced.
Preliminary requirements
1.
The blade is removed
C
B
A
Corrective maintenance
D09-CC13S20-11
37