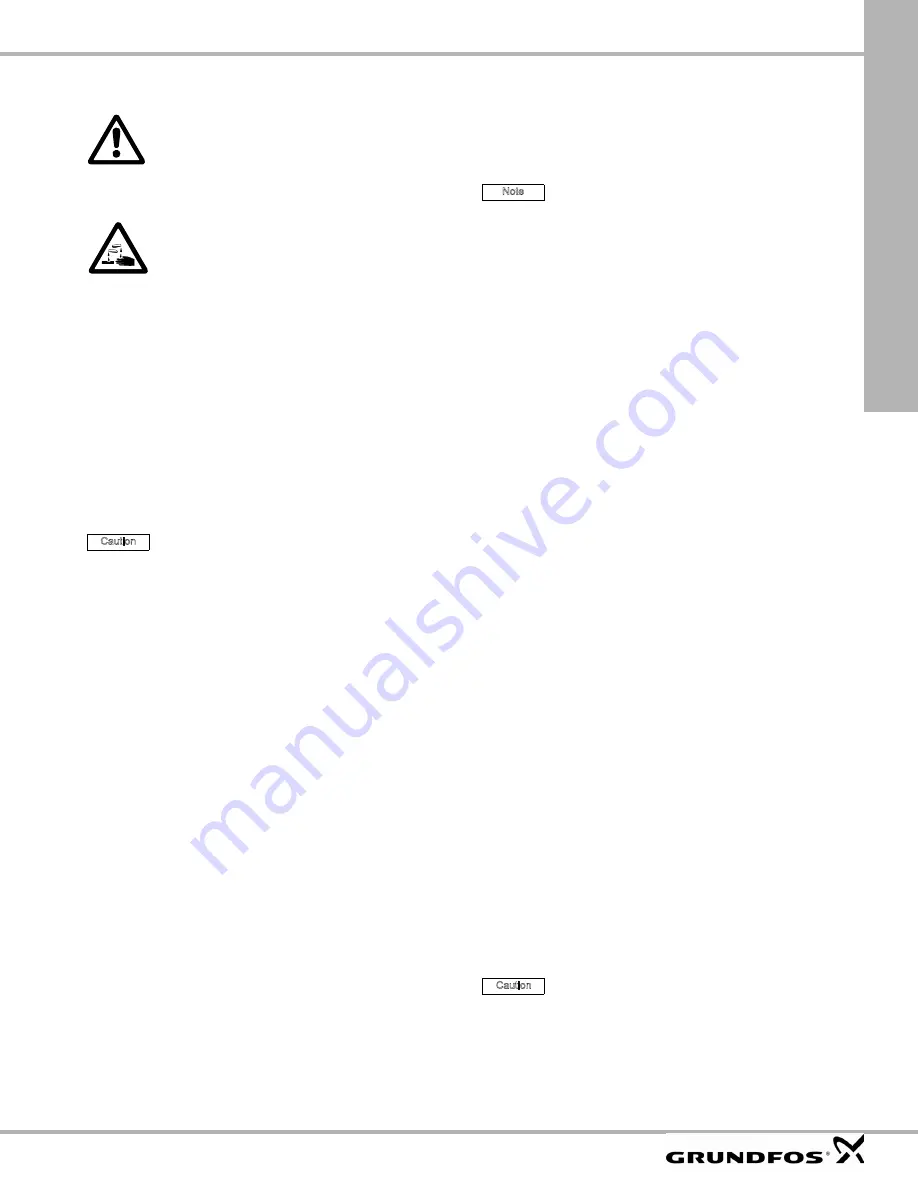
Eng
lish
(US)
12
7.3 Disassembly of pumps
1. Complete disassembly instructions are outlined below.
Proceed only as far as required to perform the maintenance
work needed.
2. Turn of power.
3. Drain System. Flush, if necessary.
4. Closed coupled units. Remove motor hold down bolts.
7.3.1 Disassembly of liquid end
1. Remove casing bolts (8B).
2. Remove back pull-out bearing frame assembly (20Y) from
casing (1A).
3. Unscrew impeller nut (8A).
4. Use appropriate size gear puller aligned behind impeller
vanes to remove impeller (3A) from shaft (6A).
5. Remove impeller key (12A).
6. Remove back plate bolts (8D). Remove back plate (2K) and
seal housing (26P).
7. Place seal housing on flat surface and press out seal seat
(14A).
8. If shaft sleeve (5A) requires replacement, it must be evenly
heated to approximately 350 °F to loosen locktite. Twist
sleeve off shaft (6A).
7.3.2 Disassembly of bearing frame (LF)
1. Remove slinger (13G).
2. Remove grease seal(s), (14S) if any.
3. Remove bearing house retaining ring (61K).
4. Press or tap on the pump end of the bearing-shaft assembly
until one bearing is out.
5. When one bearing is out, remove second retaining ring (61F),
then remove complete assembly from bearing housing.
6. Remove shaft retaining ring (61C) and press off bearings.
7. press on new bearings, remember to press only on inner race
of bearing while pressing them on.
8. Assemble frame in the reverse procedure used for
disassembly.
9. Observe the following when reassembling the bearing frame.
10. Replace lip seals (14S) if worn or damaged.
11. Replace bearings (18A), (18B) if loose, rough or noisy when
rotated.
12. Check shaft (6A) for runout at the sleeve (5A) area. Maximum
permissible is .002" T.I.R.
7.4 Seal replacement (LCS)
1. Complete preparations noted.
2. Remove coupling guard (34F).
3. Remove coupling bolts (8E). Pry apart the coupling halves
(23D), remove keys (12B) and set aside.
4. Unscrew tubing connector from pipe tee of air vent assembly.
Pipe dope is applied to threads during factory assembly, and
resulting bond may retard but will not prevent manual
disassembly.
5. Remove seal cap bolts and slide seal cap (2N) up shaft to
remove.
6. Remove seal head assembly manually from shaft (6A).
Water-soluble lubricant may be applied to shaft to ease
removal of shaft seal (14A). Pull seal head assembly
manually from shaft, using slight twisting motion (as
necessary) to loosen bellows from shaft.
7. Remove and discard seal spring and retainer.
8. remove and discard seal seat from seal cap (2N) and
thoroughly clean the inside cavity of seal cap.
9. Interior surface of bellows on new seal head is coated with
bonding agent that adheres to motor shaft. When old seal
head is removed, bonding agent no longer exists and bellows
may crack or split during removal. Installation of new
mechanical seal is always recommended if it becomes
necessary to remove existing seal from shaft.
10. Clean and lubricate shaft (6A) with water-soluble lubricant
and make sure no sharp edges exist to cut or scratch bellows
of new seal.
11. Press new seal seat firmly into seal cap. Avoid direct contact
of seal face with metallic or abrasive objects and wipe clean
after installation to ensure abrasive free sealing surface.
12. Slide new seal head assembly onto shaft by applying even
pressure to base of assembly.
13. Install seal cap (2N) down shaft.
14. See reassembly instructions.
7.5 Wear ring replacement
1. Complete preparations.
2. Back-pull rotating assembly.
3. It may be necessary to remove volute (1A) from piping, to
facilitate easy access to interior of volute. If necessary,
remove flange bolts at piping.
4. To remove worn Case Wear Ring (4A), drill two holes slightly
smaller than width of ring into exposed edge of ring. Once
holes are drilled, a chisel may be used to completely sever
ring at holes and break ring into two halves for easy removal.
5. Clean the ring cavity in the volute prior to installing wear ring
to ensure a properly aligned fit.
6. To reassemble, press fit new wear ring squarely into volute
casing cavity. Ring may be tapped into place to make sure it
is completely impressed into cavity.
Warning
Depending on the product being pumped, the
pump should be washed down before any work is
done on it.
Warning
Observe extreme caution when venting and/or
draining hazardous liquids. Wear protective
clothing in the presence of caustic, corrosive,
volatile, flammable, or hot liquids. DO NOT
breathe toxic vapors. DO NOT allow sparking,
flames, or hot surfaces in vicinity of the
equipment.
Caution
Do not screwdriver between impeller vanes to
prevent rotation. It may be necessary to use a
strap wrench around the impeller or shaft to
prevent rotation.
Note
Note
Mark or measure the original position of the
pump coupling on the motor side.
Caution
Do not use metal tooling against wear ring
surfaces. Use only rubber, rawhide, wood or
other soft material to prevent damage to ring.
PA
CO Pumps
15