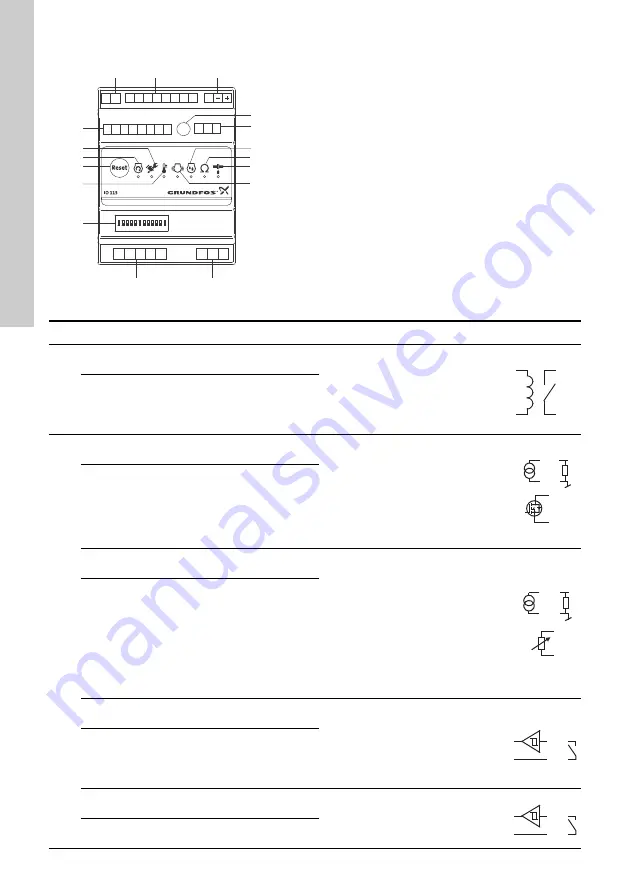
En
gl
is
h (
G
B)
20
7. Control functions
Fig. 24
IO 113 module
TM0
5
1
88
1 3
8
11
PE
T1 T2
G1 A1 G2 A2 K1 K2 R1 R2
D1 D2 D3 D4 D5 D6 D7 D8
P1 P2 P3 P4 P5
A Y B
I1 I2 I3
ON
DIP
1 2 3 4 5 6 7 8 9 10 11 12
1
2
3
4
5
6
7
8
9
10
11
12
13
14
16
15
17
Pos. Terminal Description
Data
Function
Diagram
1
T1
Terminal for
alarm relay
Max. 250 VAC
All alarms trip the alarm relay. The
alarm relay is closed during normal
operation.
In case of alarm or if IO 113 is not
connected to the power supply, the
relay opens and breaks the
connection between T1 and T2.
T2
Terminal for
alarm relay
Max. 250 VAC
2
G1
GND for analog
output 1
1) 0 V
2) 0 V
Analog output 1 has two functions set
via DIP switch 8. See section
.
1.
4-20 mA for content of water in
the oil. Load resistance: max.
250 Ω.
2.
Pulse output for content of water
in the oil and stator insulation
resistance.
A1
Terminal for
analog output 1
1) 15 VDC
2) 24 VDC, max.
100 mA
G2
GND for analog
output 2
1) 0 V
2) 0 V
Analog output 2 has two indications
set via DIP switch 7. See section
4.5 SM 113 sensor detection and
address setting
.
1.
4-20 mA for stator winding
temperature.
Load resistance: max. 250 Ω.
Note
: There is no 4-20 mA signal
if the pump is installed with PTC
sensor.
2.
Pt1000 emulator for stator
winding temperature.
A2
Terminal for
analog output 2
1) 15 VDC
2) 24 VDC, rated
1 mA
K1
GND
connection
0 V
Feedback from motor contactor
whether the pump is running or not.
Short-circuit the input when the pump
is running. The signal is used by IO
113 for filtering measuring signals
and for analysis during fault
indication.
K2
Terminal for
conductor for
contactor status
Digital input
R1
GND
connection
0 V
For resetting of alarms, see section
Short-circuit the input when alarms
are reset.
R2
Terminal for
resetting
Digital input
T1
T2
G1
A1
R
1)
G1
A1
2)
G2
A2
R
1)
G2
A2
2)
K2
K1
R2
R1