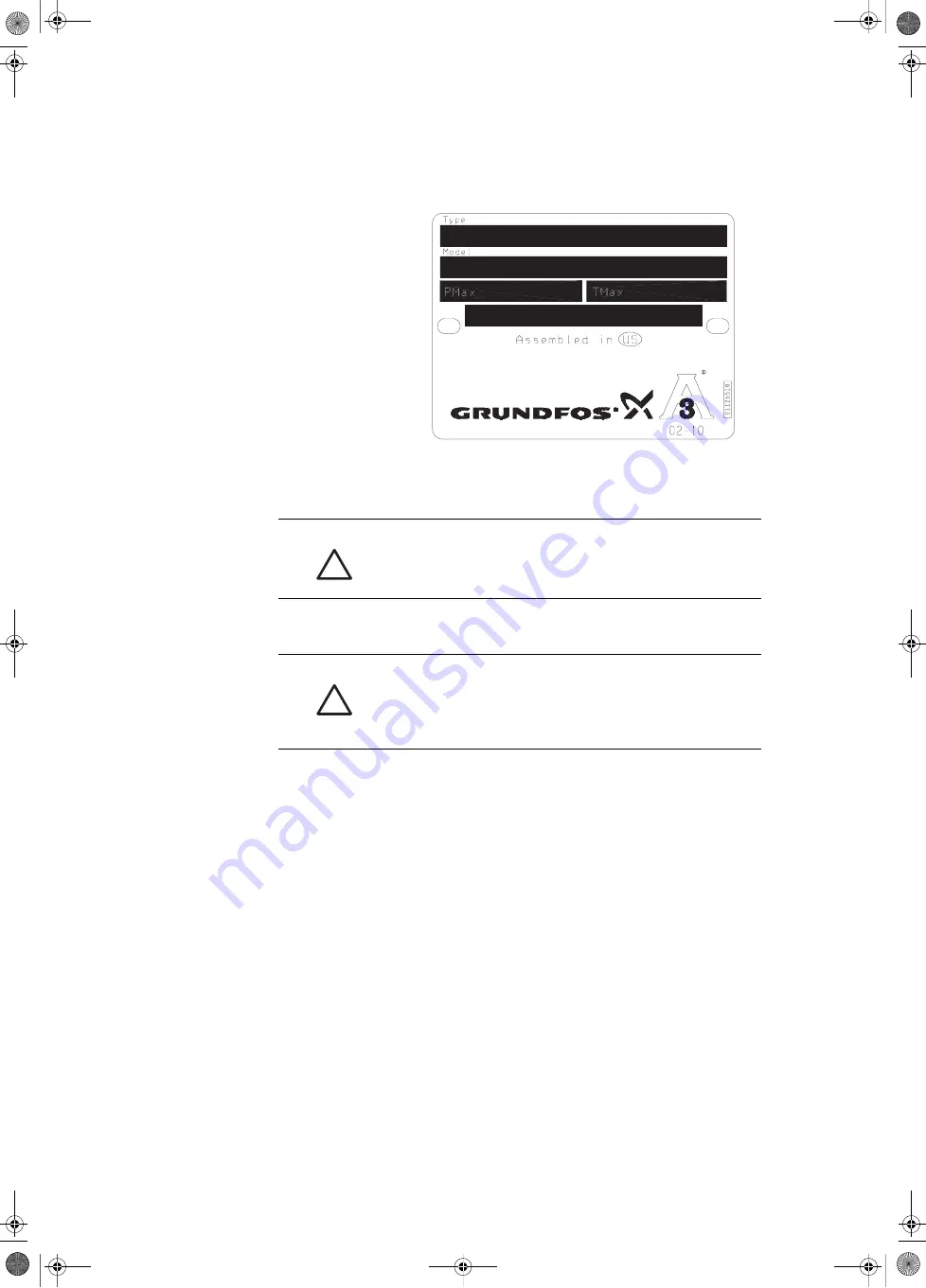
14
3.4.2 Pump model number
The pump can be identified by the pump model number.
When ordering spare parts give always the pump model
number (see nameplate for this).
3.4.3 Nameplate
3.4.4 Maximum operating temperature
C A U T I O N
!
Exceeding the maximum operating temperature!
S
Bodily injury, damage to property.
Z
Never exceed the specified operating temperatures.
3.4.5 Maximum operating pressure
W A R N I N G
!
Pressure overload!
S
Damage to property.
Z
Never exceed the specified maximum operating
pressures.
Pump opera ing pressure
The maximum permitted operating pressure depends on
various factors:
•
pump type
•
design of connections
•
design of mechanical seal.
For the values that apply to your pump, please refer to the
pump nameplate.
Fig. 4
Pump nameplate
K
.034
9V1