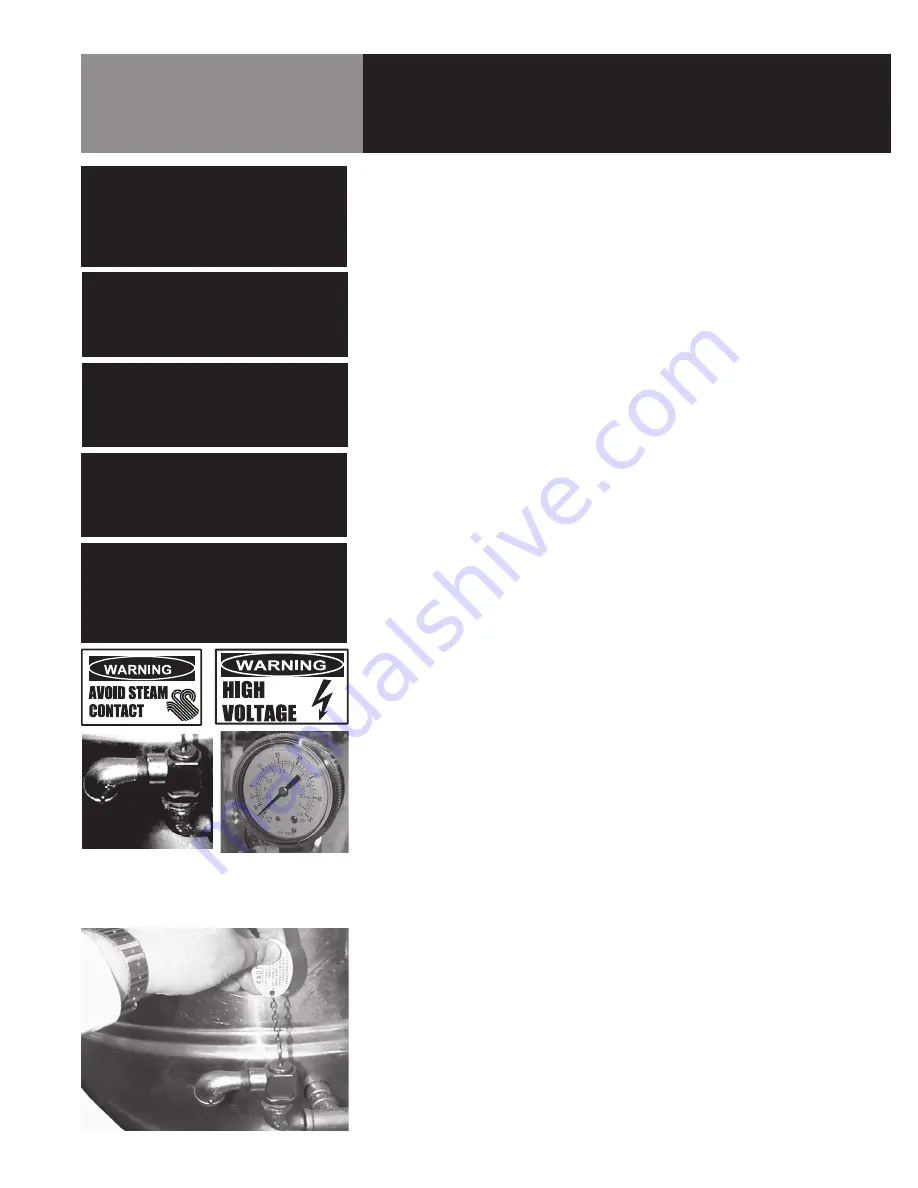
OM-DEE/4 13
Maintenance
NOTICE: Contact an authorized representative when repairs are required.
A Maintenance & Service Log is provided at the back of this manual. Each time
maintenance is performed on your kettle, enter the date on which the work was done,
what was done, and who did it. Keep this manual on file and available for operators to
use. Periodic inspection will minimize equipment down time and increase the efficiency of
operation. The following points should be checked:
1.
Check the pressure/vacuum gauge everyday. The gauge should show a vacuum of
20 to 30 inches mercury (Hg), when the kettle is cold. If it does not, see “Jacket
Vacuum” on page 14.
2.
Also check the jacket water level every day. It should be between the markers on
the gauge glass. If the level is low, see “Jacket Filling and Water Treatment” on
page 14.
3.
Test the safety valve at least twice each month. Test the valve with the kettle
operating at 105 kPa (15 psi), by holding the test lever for at least 5 seconds. Then
release the lever and let the valve snap shut. If the lever does not activate, or there
is no evidence of discharge, or the valve leaks, stop using the kettle and contact a
qualified service representative.
4.
Keep electrical wiring and connections in good condition.
5.
Keep the inside of the control console clean and dry.
6.
Safety Valve Operating Instructions
If adding water to a boiler, DO NOT ALLOW water to flow through safety valve as
sediment or debris may be deposited on seating surface.
To achieve topmost performance and maximum service life, it is necessary to
maintain a proper pressure margin between set pressure of the safety valve and
equipment operating pressure. The minimum required pressure margin for this type
of valve is 10% of the safety relief valve set pressure, but not less than 34.5 kPa
(5 psi). UNDER NO CIRCUMSTANCES SHOULD THIS MARGIN BE LESS THAN 34.5
kPa (5 psi). Failure to maintain this operating margin may result in water leakage
past the seat and an accumulation of deposits on the seating surface. Excessive
deposits may prevent the valve from operating properly, and a dangerous pressure
build-up and equipment rupture may result.
7.
Lubrication (Gears)
The gear housing has fittings for proper lubrication of moving parts. Because the
gears do not run in oil, periodic lubrication with grease is necessary. Frequency of
lubrication will depend on operating conditions, but it should be performed at least
once every six months. It is recommended that a Number Two grade LGI lithium
grease be used. Add grease through the Zerk fittings on the gear housing until
grease flows out of the bearings around the trunnion shaft. Place a liberal amount
of grease on the gear to cover the arc that is in contact with the worm gear.
WARNING
WHEN TESTING, AVOID ANY EXPOSURE TO
THE STEAM BLOWING OUT OF THE SAFETY
VALVE. DIRECT CONTACT COULD RESULT IN
SEVERE BURNS.
WARNING
DISCONNECT ELECTRICAL POWER FROM
THE UNIT BEFORE ATTEMPTING TO
GREASE THE TRUNNION BEARINGS.
WARNING
TO AVOID INJURY, READ AND FOLLOW ALL
PRECAUTIONS STATED ON THE LABEL OF
THE WATER TREATMENT COMPOUND.
WARNING
ELECTRIC POWER ALWAYS SHOULD BE
SHUT OFF BEFORE WORK IS DONE ON
INTERNAL COMPONENTS.
CAUTION
BEFORE YOU HEAT THE KETTLE AGAIN
FOR ANY PURPOSE, TURN THE ELBOW
BACK CLOCKWISE UNTIL THE OPENING
FACES DOWNWARD.
Make sure that the open
end of the elbow on the
pressure relief valve is
directed downward.
The pressure gauge
should show a vacuum of
20 to 30 inches when the
kettle is cold.
Test the safety valve at least twice monthly.
Summary of Contents for DEE-CE Series
Page 18: ...18 OM DEE 4 Parts List...
Page 19: ...OM DEE 4 19 Parts List...
Page 21: ...OM DEE 4 21 Wiring Diagram...
Page 23: ......