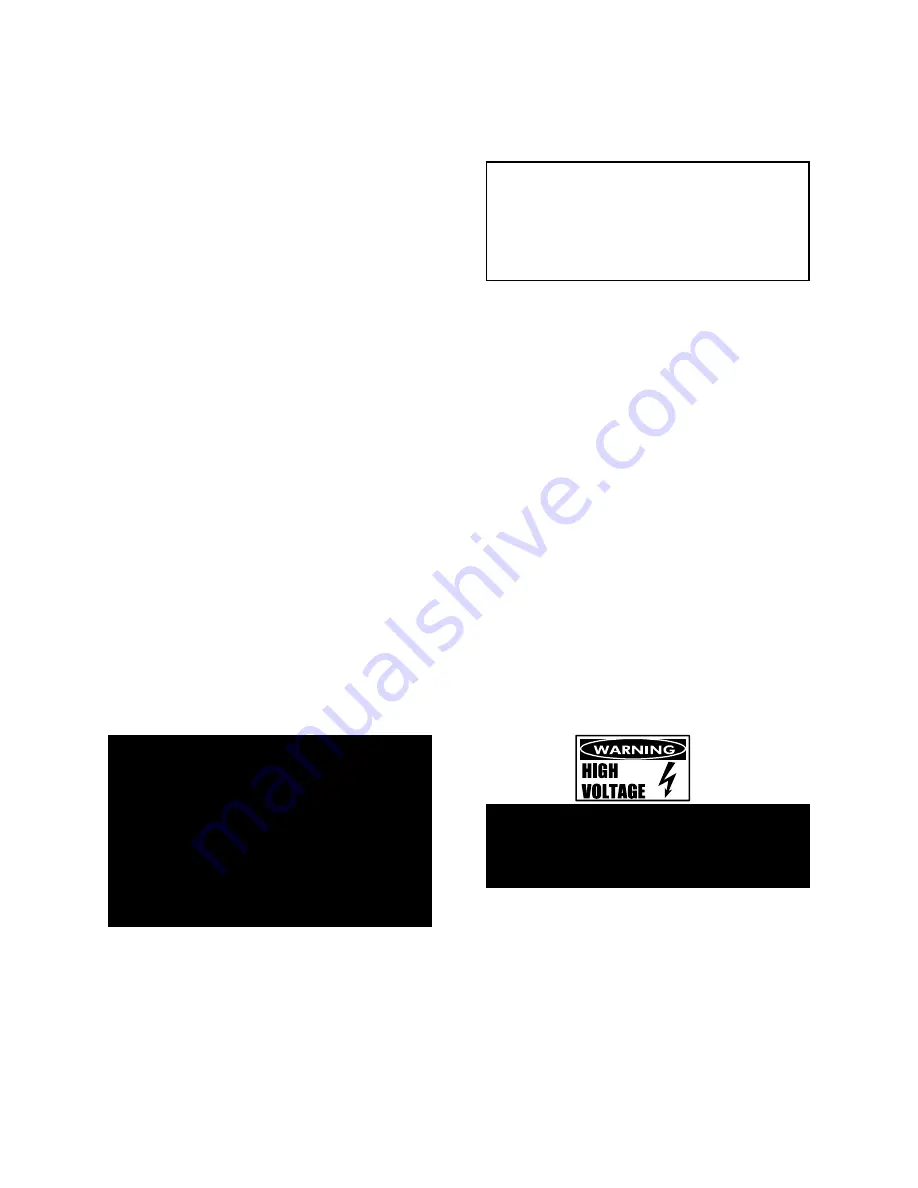
OM-CFPC
10
f,
As part of the daily cleaning program,
clean all inside and outside surfaces that
may have been soiled. Remember to
check such parts as the undersides of the
cover, the electrical console and other
more remote spots. Clean between the
pan body and the control console using
the brush provided (P/N 058705).
g.
To remove materials stuck to the
equipment, use a brush, sponge, cloth,
plastic or rubber scraper, or plastic wool
with the cleaning solution. To make
washing easier, let the cleaning solution sit
in the unit and soak into the residue, or
heat the solution briefly. Do
not
use any
gritty cleaner or metal tool that might
scratch the surface. Scratches make the
surface harder to clean, and also provide
places for bacteria to grow. Do
not
use
steel wool. Small bit of steel wool left in
the surface of the unit can cause rusting
and pitting.
h.
The outside of the unit may be polished
with a recognized stainless steel cleaner
such as Zepper from the Zep
Manufacturing Company.
i.
When the equipment needs to be
sanitized, use a sanitizing solution
equivalent to one that supplies 100 parts
per million available chlorine. Get advice
about the best sanitizing agent from you
supplier of sanitizing products.
j.
Following supplier instructions, apply the
sanitizing agent after the unit has been
cleaned and drained. Thoroughly drain off
the sanitizer.
CAUTION
NEVER LEAVE A CHLORINE SANITIZER IN
CONTACT WITH STAINLESS STEEL
SURFACES FOR LONGER THAN 30
MINUTES. LONGER CONTACT CAN CAUSE
CORROSION.
k.
After the unit has been cleaned, sanitized
and drained, let all surfaces air dry unless
the unit must be used again right away.
l.
It is recommended that the unit be
sanitized just before use. Follow the
directions of the sanitizer supplier.
m.
About once a week (more often if the
water is very hard), use a heavy duty
cleaner to remove any mineral deposits
or film left by hard water or foods.
Follow the supplier’s directions very
carefully, and rinse the unit off
thoroughly as soon as cleaning is
finished.
n.
If especially difficult cleaning problems
persist, contact your cleaning product
supplier for help. The supplier has a
trained technical staff with laboratory
facilities to serve you.
Maintenance
WARNING
USE OF REPLACEMENT PARTS OTHER
THAN THOSE SUPPLIED BY GROEN OR
THEIR AUTHORIZED DISTRIBUTORS CAN
CAUSE INJURY TO THE OPERATOR AND
DAMAGE TO THE EQUIPMENT AND WILL
VOID ALL WARRANTIES. SERVICE
PERFORMED BY OTHER THAN FACTORY-
AUTHORIZED PERSONNEL WILL VOID ALL
WARRANTIES.
Your Braising Pan is designed to require
minimum maintenance, but certain parts may
require replacement after prolonged use.
After installation, no user adjustment should be
necessary. If a service need arises, only
authorized personnel should perform the work.
. . . . . . . . . . . . . . . . . . . . . . . . . . . . . . . . . . . . .
WARNING
ELECTRICAL POWER MUST BE SHUT OFF
BEFORE ANY WORK IS PERFORMED ON
INTERNAL COMPONENTS.
Service personnel should check the unit at least
once a year. This should include inspecting
electrical wires and connections and cleaning
inside of the control console.
A Maintenance
and Service Log is provided at the rear of this
manual. Each time work is performed, enter the
date on which it was done, what was done, and
who did it
.
Summary of Contents for CFPC
Page 12: ...OM CFPC 12 Parts List Model CFPC...
Page 14: ...OM CFPC 14 Parts List Model CFPC 2...
Page 17: ...OM CFPC 17 Wiring Diagrams...
Page 18: ...OM CFPC 18 Wiring Diagrams...
Page 19: ...OM CFPC 19 Wiring Diagrams...
Page 20: ...OM CFPC 20 Wiring Diagrams...
Page 21: ...OM CFPC 21 Wiring Diagrams...
Page 22: ...OM CFPC 22 Wiring Diagrams...
Page 23: ...OM CFPC 23 Wiring Diagrams...
Page 27: ...OM CFPC 27 NOTES...