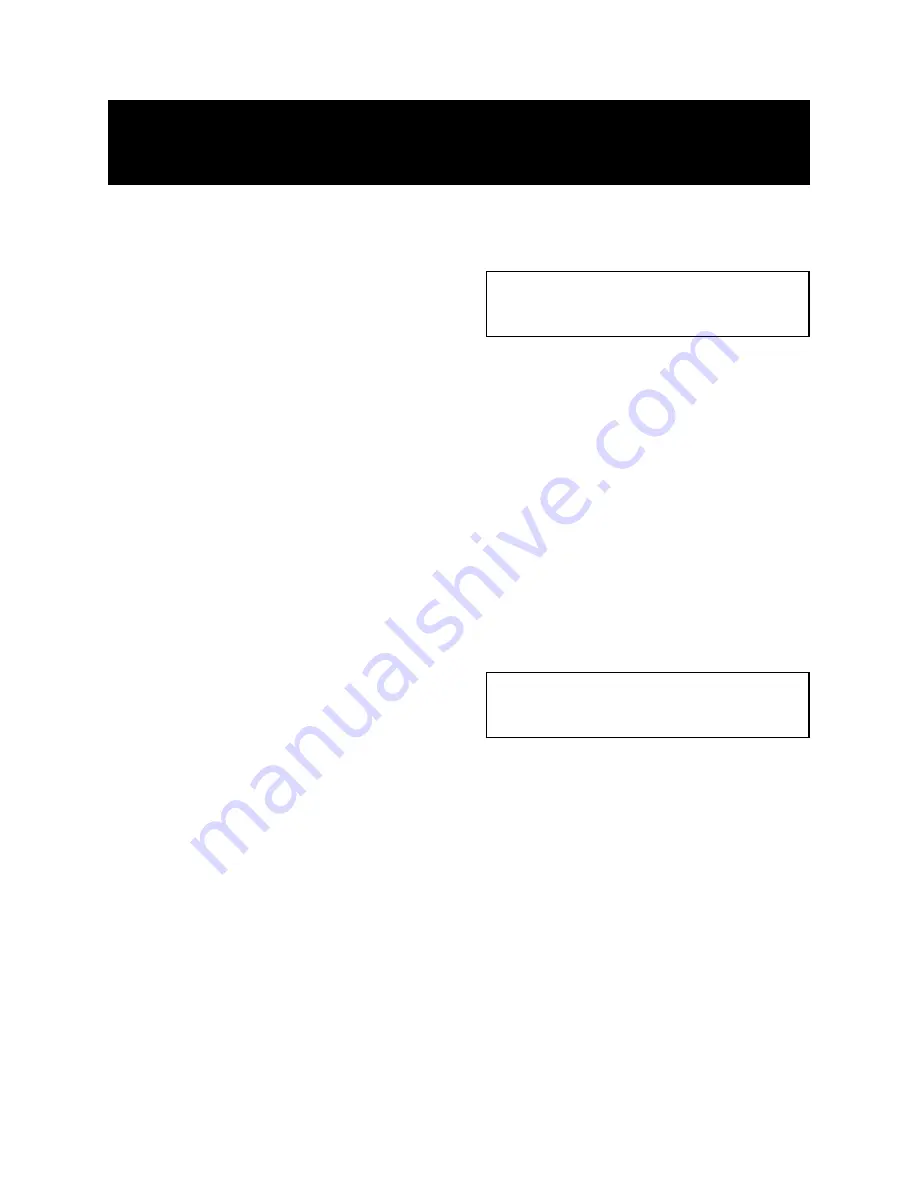
OM-CFPC
6
Installation
WARNING
THE BRAISING PAN MUST BE INSTALLED BY PERSONNEL WHO ARE QUALIFIED TO WORK WITH
ELECTRICITY. IMPROPER INSTALLATION COULD RESULT IN PERSONAL INJURY OR EQUIPMENT
DAMAGE.
Internal wiring for the Braising Pan is supplied
complete. When you receive it, the unit is ready
for connection. A wiring diagram is inside the
control box, as well as in this manual (Pages 14-
21). Your pan was operated and tested at the
factory to confirm that all controls and heating
elements were functioning correctly.
Installation is as follows:
1.
Set the unit in place and level it by turning
the adjustable feet. Make sure the pan
body is at its lowest position and check
levelness by placing a spirit level on the
bottom of the pan. The unit must be level
to avoid uneven cooking across the pan.
2.
Bolt the rear legs to the floor.
3.
At the electrical service entrance in the
bottom of the control box, make a
waterproof connection with the incoming
power line. A BX connection is not
recommended.
CAUTION
ELECTRICALLY GROUND THE PAN AT THE
TERMINAL PROVIDED.
4.
Provide the proper electrical supply as
specified on the electrical plate attached to
the equipment. Observe local codes
and/or the National Electrical Code in
accordance with ANSI/NFPA 70 — latest
edition.
5.
Any mechanical or electrical change must
be approved by the Groen Food Service
Engineering Department.
Initial Start-Up
Now that the Braising Pan has been installed,
you should test it to ensure that it is operating
correctly.
1.
Remove all literature and packing
materials from the interior and exterior of
the unit.
2.
Turn on the electrical power to the unit.
3.
Put enough water into the pan to cover its
bottom to a depth of ¼” to ½”. With the tilt
mechanism still lowered all the way back
to the horizontal position, note how the
water covers the pan bottom. This is a
good method to confirm that the unit is
properly leveled.
4.
Set the thermostat to 235ºF. The heating
indicator light should come on to indicate
that the pan is heating. Heating should
continue until the water boils.
5.
To shut the unit down, turn the thermostat
dial to “OFF.”
CAUTION
STAND AWAY FROM THE HOT WATER
WHILE TILTING THE PAN TO EMPTY IT.
6.
Position a container for the pour-off and
press down on the power tilt switch so that
the water pours out. This will confirm that
the pan body can be tilted from horizontal
to vertical. Pull the switch up to lower the
pan.
If the unit functions as described above, it is
ready for use. If it does not, call your local
Groen Authorized Service Agent.
Summary of Contents for CFPC
Page 12: ...OM CFPC 12 Parts List Model CFPC...
Page 14: ...OM CFPC 14 Parts List Model CFPC 2...
Page 17: ...OM CFPC 17 Wiring Diagrams...
Page 18: ...OM CFPC 18 Wiring Diagrams...
Page 19: ...OM CFPC 19 Wiring Diagrams...
Page 20: ...OM CFPC 20 Wiring Diagrams...
Page 21: ...OM CFPC 21 Wiring Diagrams...
Page 22: ...OM CFPC 22 Wiring Diagrams...
Page 23: ...OM CFPC 23 Wiring Diagrams...
Page 27: ...OM CFPC 27 NOTES...