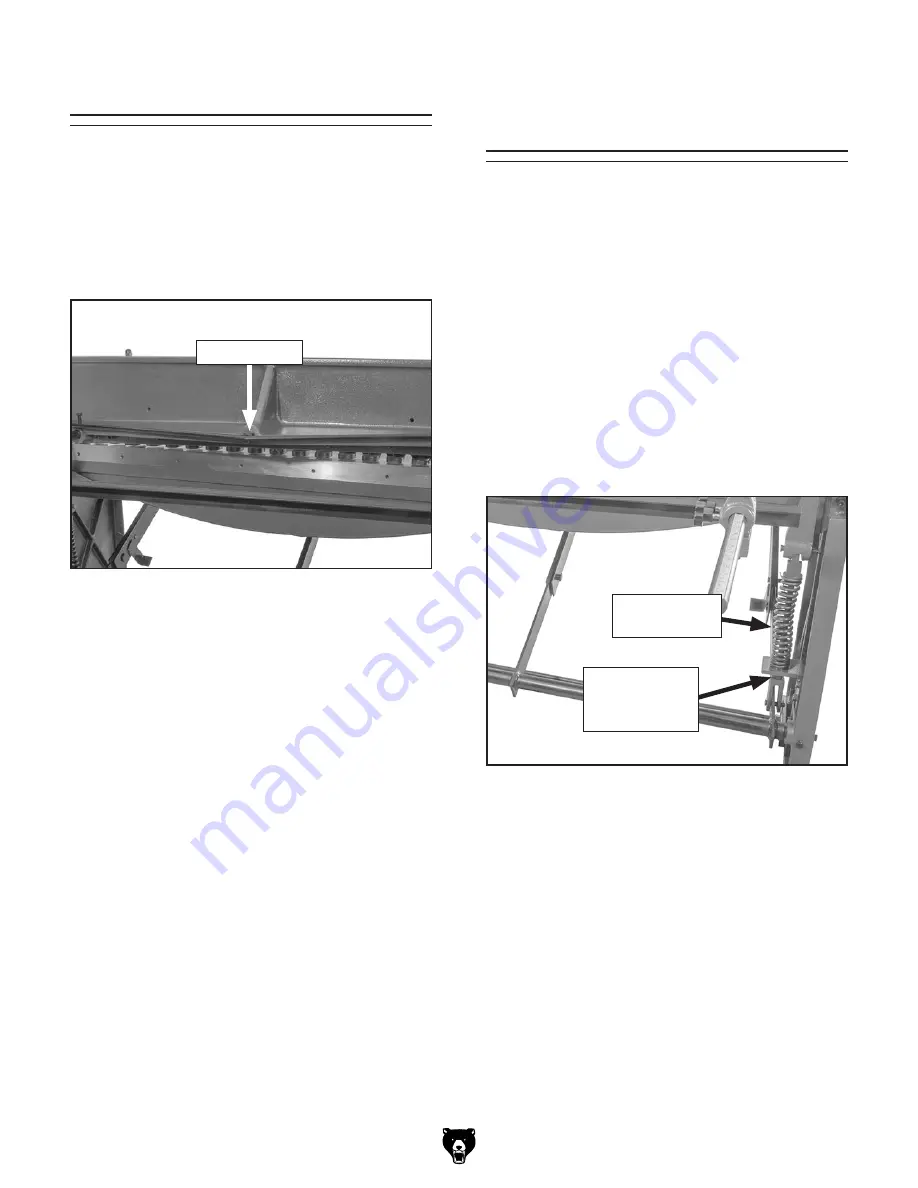
Model T32957 (Mfd. Since 09/21)
-27-
Adjusting Blade Bow
The blade bow is used to keep the upper blade
straight along its full length by adjusting the
amount of force that the bow exerts on the blade
ends.
The blade bow is adjusted by adjusting the bow
jam nut on the centering rod (see
Figure 37).
Items Needed
Qty
Open-End Wrench 24mm .................................. 1
Scrap Paper ...................................... As Needed
To adjust blade bow:
1. Perform Step 1 of Adjusting Blade Gap on
Page 26 to determine if blade bow needs
adjustment. Adjust blade gap, if necessary,
before proceeding
— If paper cuts cleanly on ends but not cen-
ter of blades, adjust bow jam nut clock-
wise while testing results until paper cuts
cleanly along entire length of blades.
— If paper cuts cleanly at center but not end
of blades, adjust bow jam nut counter-
clockwise while testing results until paper
cuts cleanly along entire length of blades.
Figure 37. Location of bow jam nut.
Bow Jam Nut
Adjusting Return
Spring Tension
The tension of the return springs can be adjusted
to increase or decrease the return rate.
Tool Needed
Qty
Open-End Wrench 24mm .................................. 1
To adjust return spring tension:
1. Adjust (2) return spring hex nuts in small,
equal increments (see
Figure 38).
— To increase return rate, tighten hex nuts
against springs.
— To decrease return rate, loosen hex nuts.
Figure 38. Return spring tension adjustment
components.
Return Spring
Hex Nut
(1 of 2)
Return Spring
(1 of 2)
Summary of Contents for T32957
Page 36: ......