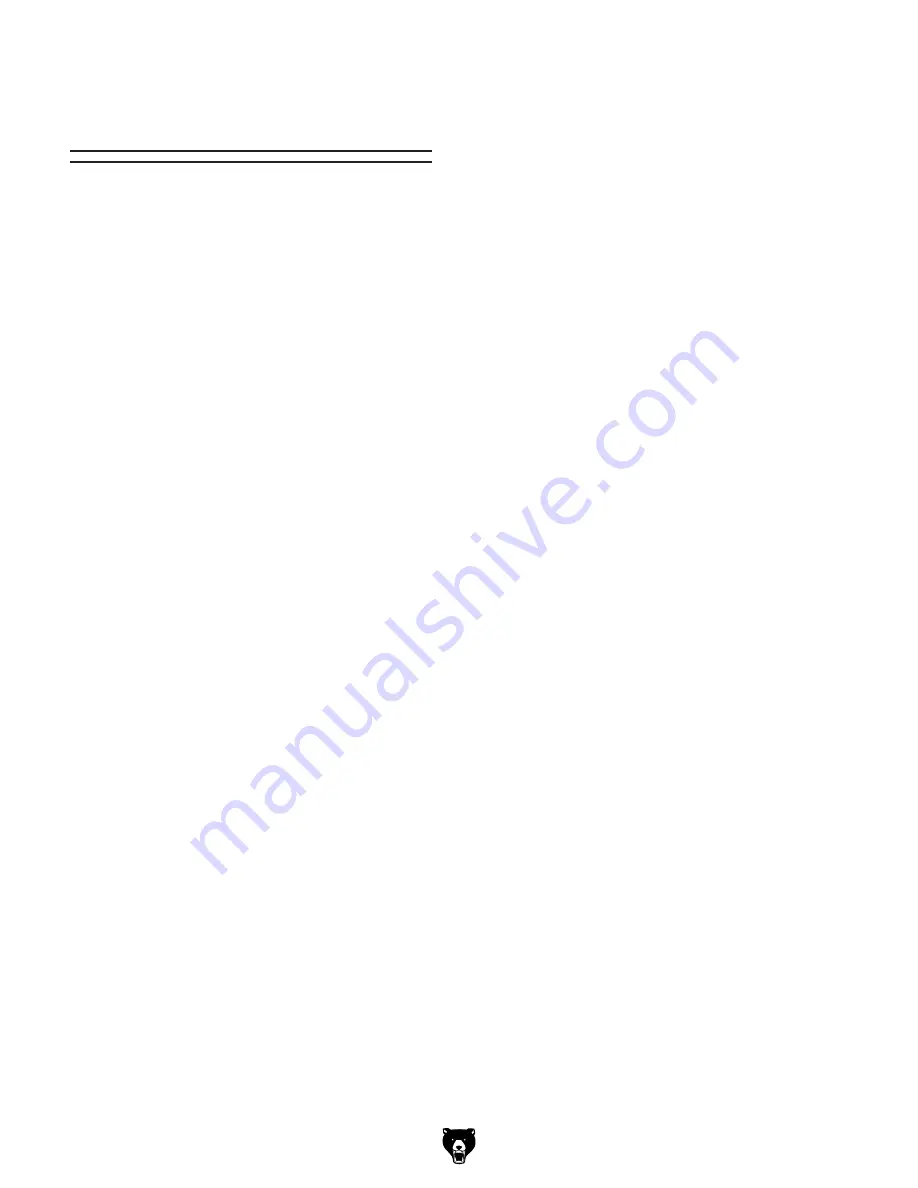
Model T25920/T25926 (Mfd. Since 08/14)
-17-
Stock Inspection &
Requirements
Some workpieces are not safe to turn or may
require modification before they are safe to
turn.
Before turning a workpiece, inspect all
workpieces for the following:
•
Workpiece Type:
This machine is intended for cutting natural
and man-made wood products, and some
plastics. Never attempt to cut any metal,
stone, or rubber workpiece; cutting these
materials can lead to machine damage or
severe injury.
•
Foreign Objects:
Nails, staples, dirt, rocks and other foreign
objects are often embedded in wood. While
cutting, these objects can become dislodged
and hit the operator, cause tool grab, or break
the turning tool, which might then fly apart.
Always visually inspect your workpiece for
these items. If they can't be removed, DO
NOT turn the workpiece.
•
Large/Loose Knots:
Loose knots can become dislodged during
the turning operation. Large knots can cause
a workpiece to completely break in half dur-
ing turning and cause machine damage and
personal injury. Choose workpieces that do
not have large/loose knots.
•
Wet or "Green" Stock:
Cutting wood with a moisture content over
20% increases the chance that the workpiece
will warp, crack, or shrink after it completely
dries.
•
Excessive Warping:
Workpieces with excessive bowing or twist-
ing are unstable and unbalanced. Never turn
these workpieces at high speed, or instability
will be magnified and the workpiece can be
ejected from the lathe causing impact injures.
Only turn concentric workpieces!
Summary of Contents for T25920
Page 48: ......