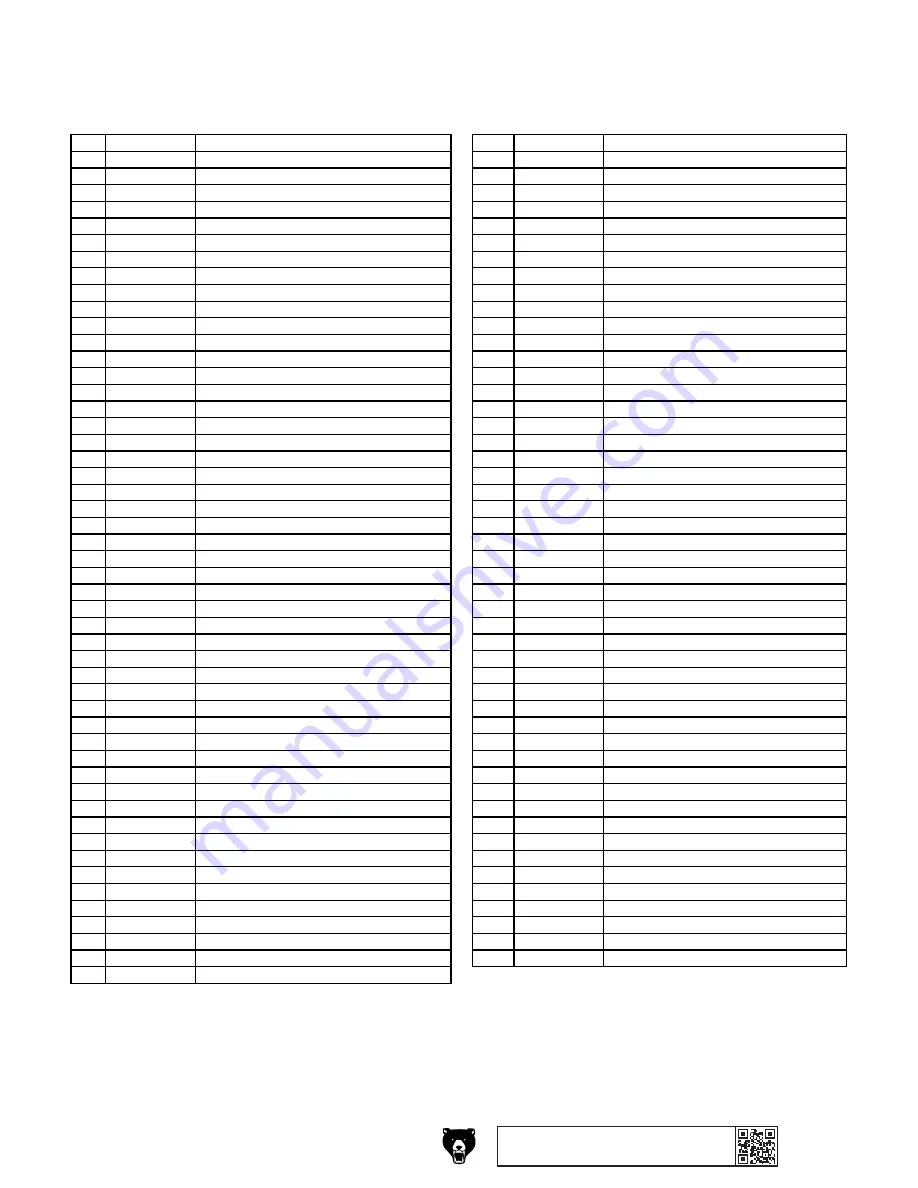
G1021X2 & G1021Z (Mfd. Since 08/16)
-57-
BUY PARTS ONLINE AT GRIZZLY.COM!
Scan QR code to visit our Parts Store.
G1021X2 Main Parts List
REF PART #
DESCRIPTION
REF PART #
DESCRIPTION
1
P1021X2001
KNOB 5/16-18, D1-3/4, ROUND
57V2
P1021X2057V2 SPROCKET 31T V2.05.18
2V2
P1021X2002V2 BELT/PULLEY COVER V2.05.18
58
P1021X2058
FENDER WASHER 6 X 20 X 3MM
3V2
P1021X2003V2 V-BELT M58 3L580 V2.05.18
59
P1021X2059
HEX BOLT M6-1 X 16
4
P1021X2004
STANDOFF-HEX MM 5/16-18 X 3/8, 3
60
P1021X2060
CHAIN 06B-1 X 63 (31 LINKS)
5
P1021X2005
FLANGE BOLT M6-1 X 12
60-1
P1021X2060-1 MASTER LINK
6
P1021X2006
BELT/PULLEY GUARD
61
P1021X2061
SPROCKET 31T
7
P1021X2007
FLAT WASHER 5/16
63
P1021X2063
EXT RETAINING RING 12MM
8
P1021X2008
HEX NUT 5/16-18
64
P1021X2064
CHIP BREAKER ADJUSTMENT ROD
9
P1021X2009
HEX BOLT M8-1.25 X 20
65
P1021X2065
CHIP BREAKER PIVOT ROD
10
P1021X2010
FENDER WASHER 8 X 30 X 4MM
66
P1021X2066
HEX NUT M12-1.75
11
P1021X2011
CUTTERHEAD PULLEY
67
P1021X2067
E-CLIP 15MM
13
P1021X2013
UPPER COVER
68
P1021X2068
SPACER
15V2 P1021X2015V2 FLANGE BOLT M6-1 X 12
69
P1021X2069
ANTI-KICKBACK FINGER
17
P1021X2017
CAP SCREW M6-1 X 20
70
P1021X2070
ANTI-KICKBACK SHAFT
18
P1021X2018
RETURN ROLLER BRACKET
71
P1021X2071
INFEED ROLLER
19
P1021X2019
KEY 4 X 4 X 10
72V2
P1021X2072V2 SPROCKET 31T V2.05.18
20
P1021X2020
HANDWHEEL TYPE-3 151D X 10B-K X 3/8-16
73
P1021X2073
CAP SCREW M6-1 X 12
21
P1021X2021
CHIP BREAKER
74
P1021X2074
BALL BEARING 6204ZZ
22
P1021X2022
FLAT WASHER 10MM
75
P1021X2075
GEAR 16T
23
P1021X2023
HEX NUT M10-1.25
76
P1021X2076
CAP SCREW M6-1 X 25
24
P1021X2024
REVOLVING HANDLE 1 X 3-9/16, 3/8-16 X 1/2
77
P1021X2077
BALL BEARING 6201-2RS
25
P1021X2025
CHIP DEFLECTOR
78
P1021X2078
GEAR 47T
26
P1021X2026
HEX BOLT M6-1 X 12
79
P1021X2079
GEARED SHAFT 18T
28
P1021X2028
FLAT SPRING 84 X 46 X 0.6MM
80
P1021X2080
KEY 5 X 5 X 10
29
P1021X2029
TENSIONING SET SCREW M22-1.5 X 20
81V2
P1021X2081V2 GEARBOX COVER V2.05.18
30
P1021X2030
SPACER 8.2 X 22 X 3MM
82
P1021X2082
LOCATING PIN 8 X 7.55 X 7.95
31
P1021X2031
CHAIN TENSIONER
84
P1021X2084
GEARED SHAFT 22T/18T
32
P1021X2032
SHOULDER BOLT M8-1.25 X 14, 4 X 12
85
P1021X2085
KEY 6 X 6 X 40
33
P1021X2033
IDLER WHEEL
86
P1021X2086
GEAR 71T
34
P1021X2034
IDLER SHAFT
87
P1021X2087
KNOB 3/8-16, D1-1/4, BALL
35
P1021X2035
ROLL PIN 6 X 20
88
P1021X2088
CHAIN 06B-1 X 47 (23 LINKS)
36V2 P1021X2036V2 DRIVE CHAIN COVER V2.05.18
88-1
P1021X2088-1 HALF LINK
37
P1021X2037
CAP SCREW M8-1.25 X 50
89
P1021X2089
SPROCKET 12T W/KEY
38
P1021X2038
SET SCREW M6-1 X 16
90V2
P1021X2090V2 OIL PLUG 1/4 NPT X 3/4" V2.05.18
39
P1021X2039
EXTENSION SPRING 1 X 8.5 X 33
91
P1021X2091
OIL SEAL 28 X 40 X 8
40
P1021X2040
SPRING BRACKET
92V2
P1021X2092V2 GEARBOX V2.05.18
41
P1021X2041
BALL BEARING 6205-2RS
93
P1021X2093
GASKET
42
P1021X2042
CAP SCREW M6-1 X 10
94
P1021X2094
COMBO GEAR 92T/96T
43
P1021X2043
KEY 8 X 8 X 36
95
P1021X2095
BEARING SHAFT
44V2 P1021X2044V2 SPIRAL CUTTERHEAD 15" V2.05.18
96
P1021X2096
GEAR SHAFT
46
P1021X2046
SET SCREW M10-1.5 X 12
97
P1021X2097
COMPRESSION SPRING 0.6 X 5.9 X 16
47
P1021X2047
SET SCREW M8-1.25 X 12
98
P1021X2098
STEEL BALL 6MM
48
P1021X2048
COMPRESSION SPRING 3.5 X 19.7 X 70
99
P1021X2099
OIL SEAL 25 X 47 X 6
49
P1021X2049
BUSHING BLOCK
100
P1021X2100
BALL BEARING 6204ZZ
50
P1021X2050
BUSHING BLOCK PLATE
101
P1021X2101
KEY 5 X 5 X 12
51
P1021X2051
HEX NUT M6-1
102
P1021X2102
SHIFTING FORK
52
P1021X2052
HEAD CASTING
103
P1021X2103
SHIFTING SHAFT
53
P1021X2053
OUTFEED ROLLER
104
P1021X2104
O-RING 11.8 X 2.4 P12
54
P1021X2054
DEPTH LIMITER
108V2 P1021X2108V2 BALL BEARING 608ZZ V2.05.18
55
P1021X2055
FLAT HD SCR M5-.8 X 8
114
P1021X2114
SET SCREW M6-1 X 12
56
P1021X2056
KEY 5 X 5 X 22
Summary of Contents for G1021X2
Page 76: ......