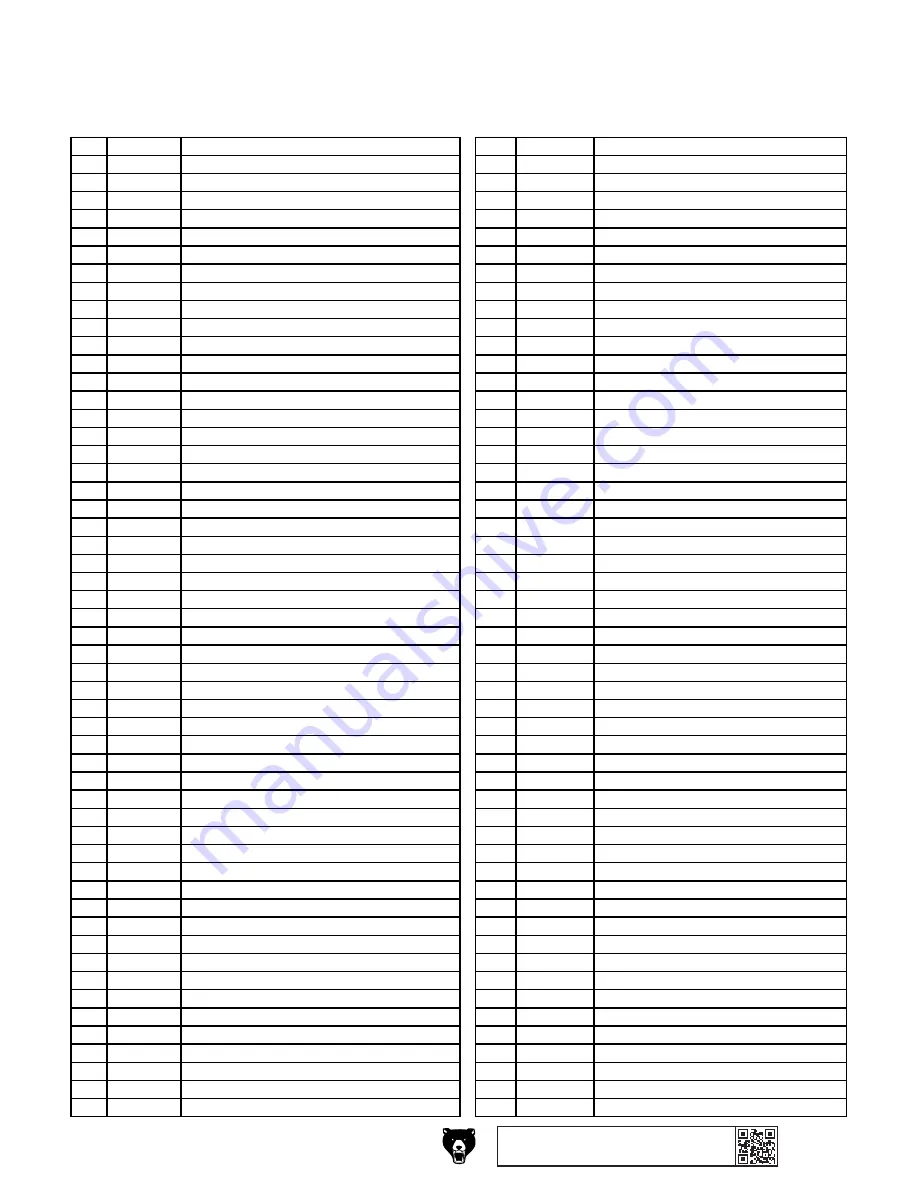
Model G0926 (Mfd. Since 11/20)
-49-
BUY PARTS ONLINE AT GRIZZLY.COM!
Scan QR code to visit our Parts Store.
REF PART #
DESCRIPTION
REF PART #
DESCRIPTION
1
P0926001
MOTOR 3/4HP 120V 1-PH
56
P0926056
PHLP HD SCR M6-1 X 16
2
P0926002
CAP SCREW M5-.8 X 16
57
P0926057
KNOB BOLT M10-1.5 X 30, 12-LOBE, D60
3
P0926003
BALL BEARING 607ZZ
58
P0926058
FLAT WASHER 10MM
4
P0926004
EXT RETAINING RING 11MM
59
P0926059
CORD CLAMP
5
P0926005
GEAR 43T
60
P0926060
BUTTON HD CAP SCR M5-.8 X 12
6
P0926006
KEY 4 X 4 X 6 RE
61
P0926061
GROMMET 5/16"
7
P0926007
GEAR 10T
62
P0926062
BALL BEARING 6202ZZ
8
P0926008
BALL BEARING 607ZZ
63
P0926063
SET SCREW M6-1 X 6
9
P0926009
KEY 5 X 5 X 10 RE
64
P0926064
MAGNET SEAT
10
P0926010
WHEEL SHAFT (FRONT)
65
P0926065
MAGNET 6 X 3MM
11
P0926011
GEAR 50T
66
P0926066
EXT RETAINING RING 35MM
12
P0926012
CAP SCREW M6-1 X 20
67
P0926067
INT RETAINING RING 15MM
13
P0926013
FLAT WASHER 6MM
68
P0926068
BLADE WHEEL (FRONT)
14
P0926014
GEARBOX
69
P0926069
SET SCREW M8-1.25 X 8
15
P0926015
SET SCREW M6-1 X 6
70
P0926070
KEY 5 X 5 X 25 RE
16
P0926016
MOTOR COVER
71
P0926071
FLAT WASHER 5MM
17
P0926017
PHLP HD SCR M4-.7 X 10
72
P0926072
HEX BOLT M5-.8 X 16
18
P0926018
BLADE SPEED DIAL
73
P0926073
GROMMET 5/16"
20
P0926020
DIGITAL SPEED DISPLAY 2017120401B
74
P0926074
MOTOR DRIVER CORD 18G 3W 45"
21
P0926021
DISPLAY WIRE
75
P0926075
FRAME
22
P0926022
TAP SCREW M3 X 10
76
P0926076
HEX BOLT M6-1 X 25
23
P0926023
SPEED SENSOR 45L
77
P0926077
HEX NUT M6-1
24
P0926024
TAP SCREW M3.5 X 20
78
P0926078
HEX BOLT M8-1.25 X 30
25
P0926025
POTENTIOMETER BK10
79
P0926079
FLAT WASHER 8MM
26
P0926026
CIRCUIT BREAKER ZHONGZUI 68-SERIES 4A
80
P0926080
BLADE GUIDE BASE (FRONT)
27
P0926027
CIRCUIT BOARD PWM500C
81
P0926081
FLAT WASHER 8MM
28
P0926028
CIRCUIT BREAKER WIRE
82
P0926082
LOCK WASHER 8MM
29
P0926029
PHLP HD SCR M5-.8 X 8
83
P0926083
HEX BOLT M8-1.25 X 30
30
P0926030
CIRCUIT BOARD HOUSING
84
P0926084
HEX NUT M8-1.25
31
P0926031
HEX BOLT M8-1.25 X 30
85
P0926085
LOCK WASHER 8MM
32
P0926032
HEX BOLT M8-1.25 X 16
86
P0926086
BALL BEARING 629ZZ
33
P0926033
HEX BOLT M8-1.25 X 30
87
P0926087
BLADE GUIDE PIN (FRONT)
34
P0926034
FLAT WASHER 8MM
88
P0926088
BLADE GUIDE (FRONT)
35
P0926035
HEX BOLT M6-1 X 12
89
P0926089
BLADE GUIDE SHAFT (FRONT)
36
P0926036
LOCK WASHER 6MM
90
P0926090
BALL BEARING 629ZZ
37
P0926037
TRACKING BRACKET
91
P0926091
EXT RETAINING RING 9MM
38
P0926038
FLAT WASHER 6MM
92
P0926092
BLADE GUARD (FRONT)
39
P0926039
TRACKING BRACKET MOUNT
93
P0926093
FLAT HD SCR M6-1 X 16
40
P0926040
TRACKING ADJUSTMENT BLOCK
94
P0926094
HEX NUT M8-1.25
41
P0926041
WHEEL SHAFT (REAR)
95
P0926095
LOCK WASHER 8MM
42
P0926042
BLADE TENSION NUT
96
P0926096
HEX BOLT M8-1.25 X 30
43
P0926043
COMPRESSION SPRING 2 X 14 X 76
97
P0926097
LOCK WASHER 8MM
44
P0926044
FLAT WASHER 10MM
98
P0926098
FLAT WASHER 8MM
45
P0926045
KNOB BOLT M10-1.5 X 90, 12-LOBE, D60
99
P0926099
BALL BEARING 629ZZ
46
P0926046
BUSHING 16 X 19 X 6.5
100
P0926100
BLADE GUIDE PIN (REAR)
47
P0926047
BALL BEARING 6202ZZ
101
P0926101
BLADE GUIDE (REAR)
48
P0926048
EXT RETAINING RING 35MM
102
P0926102
BLADE GUIDE SHAFT (REAR)
49
P0926049
BLADE WHEEL (REAR)
103
P0926103
BALL BEARING 629ZZ
50
P0926050
FLAT WASHER 5MM
104
P0926104
EXT RETAINING RING 9MM
51
P0926051
HEX BOLT M5-.8 X 16
105
P0926105
BLADE GUARD (REAR)
52
P0926052
BLADE 64-1/2" X 1/2" X 1/4" 14 TPI
106
P0926106
FLAT WASHER 4MM
53
P0926053
AUTO-OFF TAB
107
P0926107
PHLP HD SCR M4-.7 X 6
54
P0926054
FLAT WASHER 6MM
108
P0926108
BLADE GUARD BASE (REAR)
55
P0926055
LOCK WASHER 6MM
109
P0926109
PHLP HD SCR M4-.7 X 8
Main Parts List
Summary of Contents for G0926
Page 56: ......