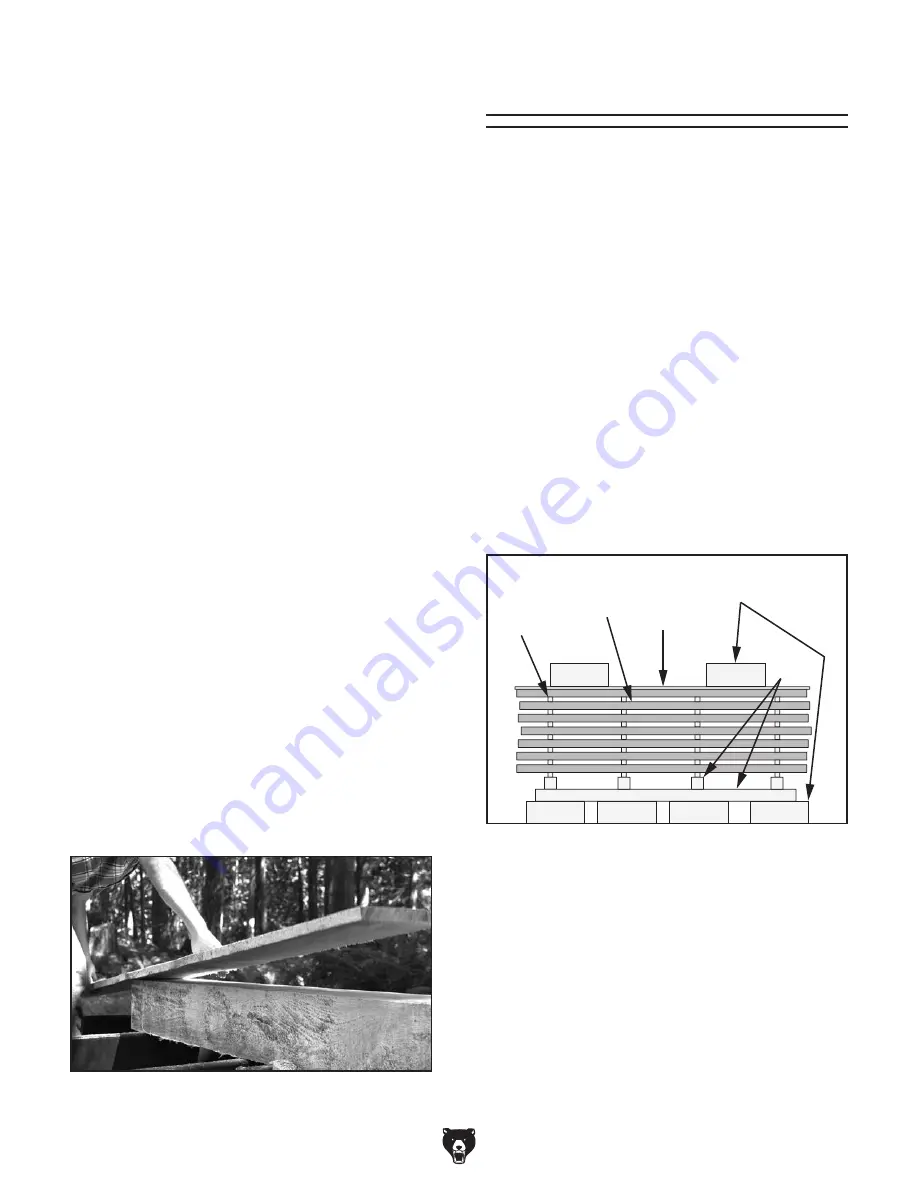
-26-
Model G0901 (Mfd. Since 09/19)
Quartersawn Lumber
Riftsawn Lumber
Cants
Quartersawn lumber is characterized by woodgrain
nearly perpendicular to the board. By some defi-
nitions, quartersawn lumber has grain more than
45° to the face of the lumber. In this manual,
quartersawn refers to lumber with grain between
75–90° to the face.
Quartersawn lumber is less likely to cup or twist
when dried. However, producing perfectly quar-
ter sawn lumber is typically time consuming and
wastes a large volume of wood.
Some types of wood, such as white oak, show ray
flecks on the surface of the board when quarter-
sawn, which is highly sought after by woodwork-
ers. Taking the time to produce more quarter
sawn lumber can pay off, but it is important to
know what you are sawing and how the lumber
will be used before putting in the extra work.
Sometimes classified as a type of quartersawn
lumber, riftsawn lumber is characterized by
woodgrain between 45 – 70° to the face of the
lumber. It will never have perfectly perpendicular
woodgrain or show ray flecks.
Riftsawn lumber is often the by-product of quarter
sawing methods. Many sawyers consider riftsawn
lumber to be a happy medium between structural
integrity and milling time.
Cants are sawn logs with at least one finished
side. Cants with four finished sides are often used
in construction or resawn into smaller pieces of
dimensional lumber.
Figure 31. Example of live sawing a cant into
dimensional lumber.
Drying Lumber
Before cutting your first log, have a plan for dry-
ing your lumber. Depending on the species of
wood, a green log might have anywhere from
60%–180% moisture content, and needs to be
dried to approximately 6%–11% before it can be
finished and used.
With the moisture loss, lumber will shrink and
warp. Depending on the drying conditions and
species of wood, air-drying can take anywhere
from several weeks to many months.
The most common method is air-drying, in which
freshly cut lumber is stacked outdoors with stick-
ers and weights and the ends are sealed with
latex paint. Weighing down the stack and sealing
the board ends help to minimize warping as the
wood shrinks. When the lumber reaches approxi-
mately 20% moisture content, the stack is moved
indoors until drying is complete.
Sticker
Drying
Wood
Cinderblock
4x4
Plywood
Figure 32. Side view of an air-drying stack.
Tracking moisture content can be done by regu-
larly weighing and recording several of the dry-
ing boards. When the rate of weight loss slow
or stops, the wood has stopped drying. Moisture
meters (see
Page 33) provide a fast and accurate
alternative to weight tracking.
Due to the many variables involved in drying lum-
ber, it is important to research and plan for your
specific needs. Understand the drying environ-
ment and type of wood in order to ensure the end
product meets your needs.
Summary of Contents for G0901
Page 56: ......