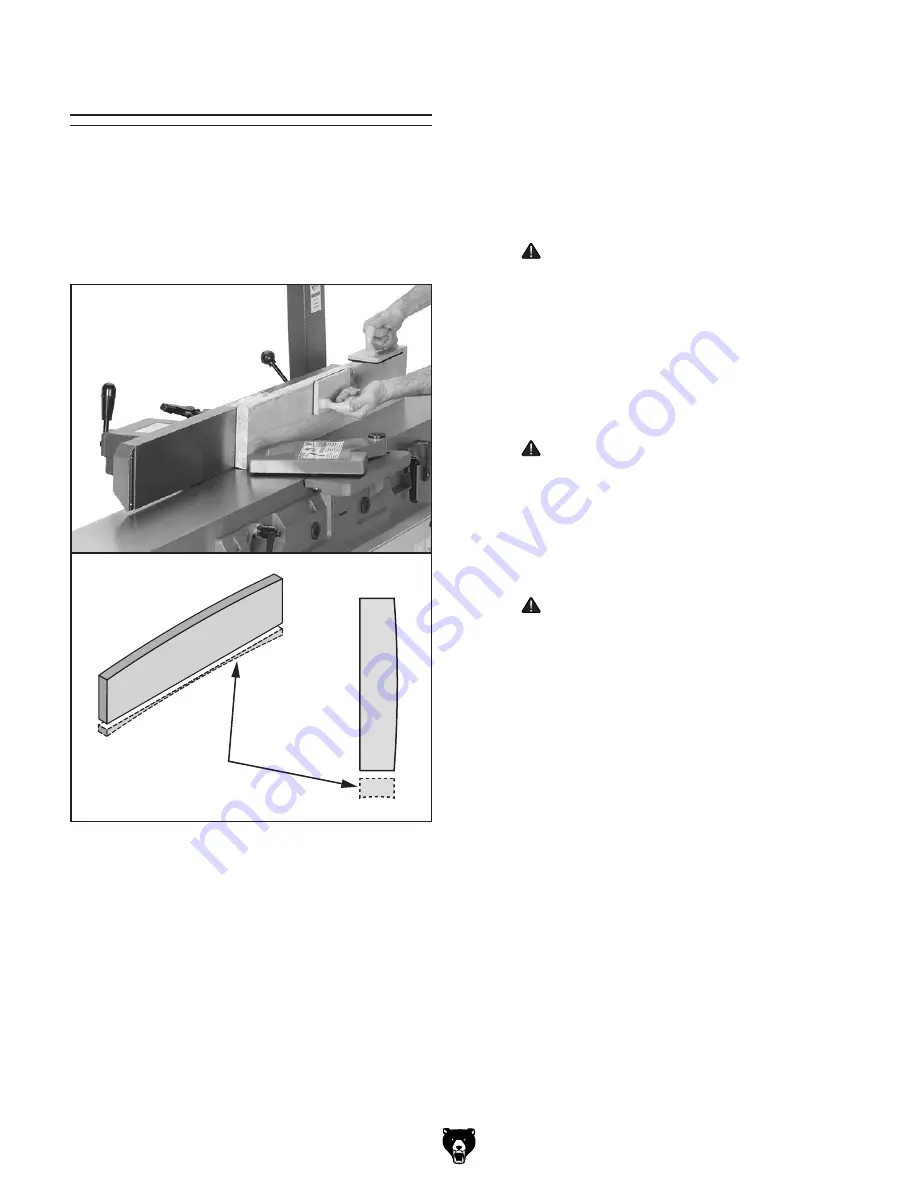
Model G0855/G0856 (Mfd. Since 02/19)
-31-
Edge Jointing
To edge joint on jointer:
1. Inspect stock to ensure it is safe and suitable
for the operation
(see Stock Inspection &
Requirements section).
2. Set infeed table height to desired cutting
depth for each pass.
CAUTION: To minimize risk of kickback,
do not exceed a cutting depth of
1
⁄
8
" per pass.
3. Set fence to 90°.
4. Start jointer.
5. Place workpiece firmly against fence and
infeed table.
CAUTION: To ensure workpiece remains
stable during cut, concave sides of workpiece
must face toward table and fence.
6. Feed workpiece completely across cutter-
head while keeping it firmly against fence
and tables during the entire cut.
CAUTION: Keep hands at least 4" away
from cutterhead during the entire cut. Instead
of allowing a hand to pass directly over cut-
terhead, lift it up and over cutterhead, and
safely reposition it on the outfeed side to con-
tinue supporting workpiece. Use push blocks
whenever practical to further reduce risk of
accidental hand contact with cutterhead.
7. Repeat Step 6 until the entire edge is flat.
Tip: When squaring up stock, cut opposite
edge of workpiece with a table saw instead
of the jointer—otherwise, both edges of work-
piece will not be parallel with each other.
Figure 29. Example photo of an edge jointing
operation.
Removed
Surface
Edge jointing (see example
Figures below) pro-
duces a flat and true surface along the side of
a workpiece by removing uneven areas. It is an
essential step for squaring up warped or rough
stock and when preparing a workpiece for joinery
or finishing.