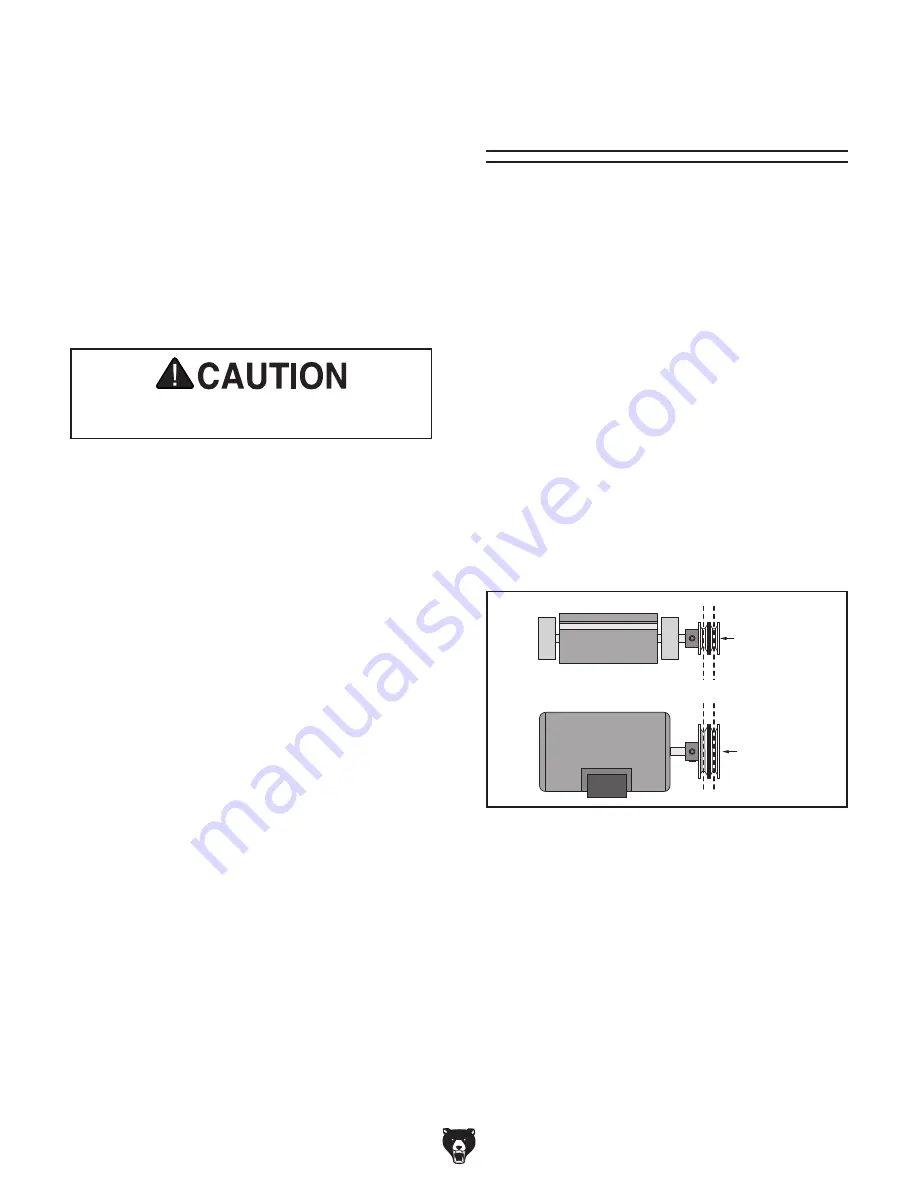
-36-
Model G0834 (Mfd. Since 12/17)
5. Press down on motor until there is proper
tension on V-belts. While holding motor
down, tighten hex nuts on tension rods
(see
Figure 41 on Page 35).
6. Replace rear access panel and close
cutterhead pulley cover.
Proper pulley alignment is important for optimum
power transfer and belt life. Pulley alignment is
adjusted by slightly repositioning the motor on the
motor mounting plate.
Items Needed
Qty
Hex Wrench 5mm .............................................. 1
Wrench or Socket 19mm ................................... 1
To check and align pulleys:
1. DISCONNECT MACHINE FROM POWER!
2. Remove rear access panel and open pulley
cover.
3. Visually check alignment of both pulleys
to make sure they are aligned and V-belts
are straight up and down, as shown in
Figure 42).
Checking/Adjusting
Pulley Alignment
Figure 42. Pulleys aligned.
Cutterhead
Pulley
Motor
Pulley
Alignment
1. DISCONNECT MACHINE FROM POWER!
2. Remove rear access panel and open
cutterhead pulley cover.
3. Loosen hex nuts on motor tension rods
(see
Figure 41 on Page 35).
4. Have another person lift motor as you remove
belts and replace them with new ones. It may
help to use a 2x4 as a lever to raise motor.
Make sure ribs of belt are seated in pulley
grooves.
5. Press down on motor until there is proper
tension on V-belts. While holding motor
down, tighten hex nuts on tension rods
(see
Figure 41 on Page 35).
6. Check belt tension (refer to Step 3
of
Tensioning V-Belts on Page 35 for
instructions).
7. Replace rear access motor cover and close
cutterhead pulley cover.
— If pulleys are aligned, no adjustment is
necessary.
— If pulleys are not aligned, proceed to
Step 4.
Items Needed
Qty
New V-Belts ....................................................... 2
Hex Wrench 5mm .............................................. 1
Wrench or Socket 19mm ................................... 1
Replacing V-Belts
V-belts and pulleys will be hot after opera-
tion. Allow them to cool before handling.
Summary of Contents for G0834
Page 60: ......