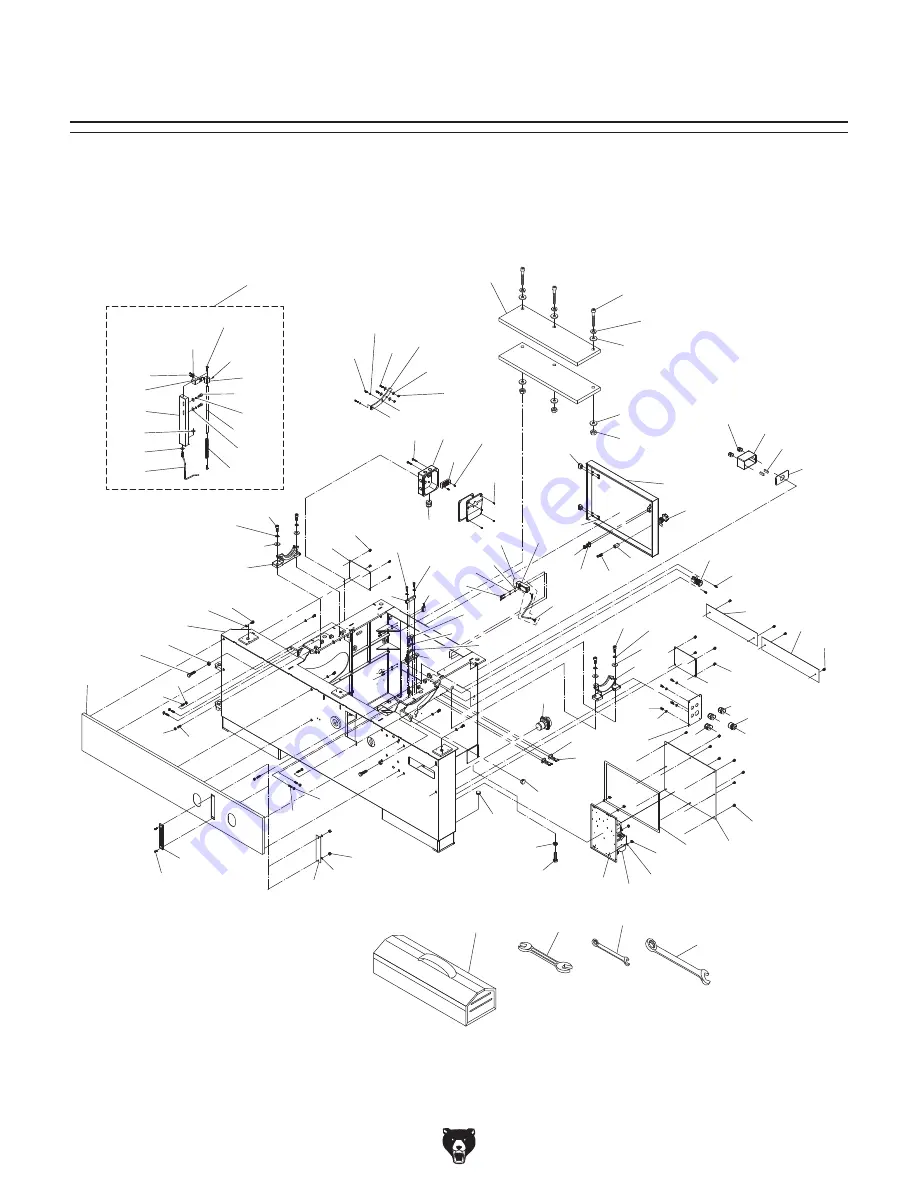
-90-
Model G0764Z (Mfd. Since 10/15)
1
77
78
2
3
4
8 9
12
13
12
13
14
16
16-1
17
18
19
20
20-1
20-2
24
27
28
29
30
31
32
33
34
31
32
33
34
35
36
37
38
39
5
11
6
6
10
7
40
41
42
43
44 45
46
47
48
49
50
51
55
56
57
58
59
60
61
62
63
64
65 66 67
68 69
71
71-1
71-2
71-3
71-4
71-5
71-5
71-6
71-7
71-8
71-9
71-10
71-11
71-12
71-13
71-14
72
73
74
75
80
81
76
99
82
83
84
86
87
88
89
89
89
90
52
79
53
54
21
22
23
91
92
93
95
96
97
Body
SECTION 9: PARTS
We do our best to stock replacement parts when possible, but we cannot guarantee that all parts shown
are available for purchase. Call
(800) 523-4777 or visit www.grizzly.com/parts to check for availability.
Summary of Contents for G0764Z
Page 21: ...Model G0764Z Mfd Since 10 15 19 5mm Hardware Recognition Chart ...
Page 118: ......