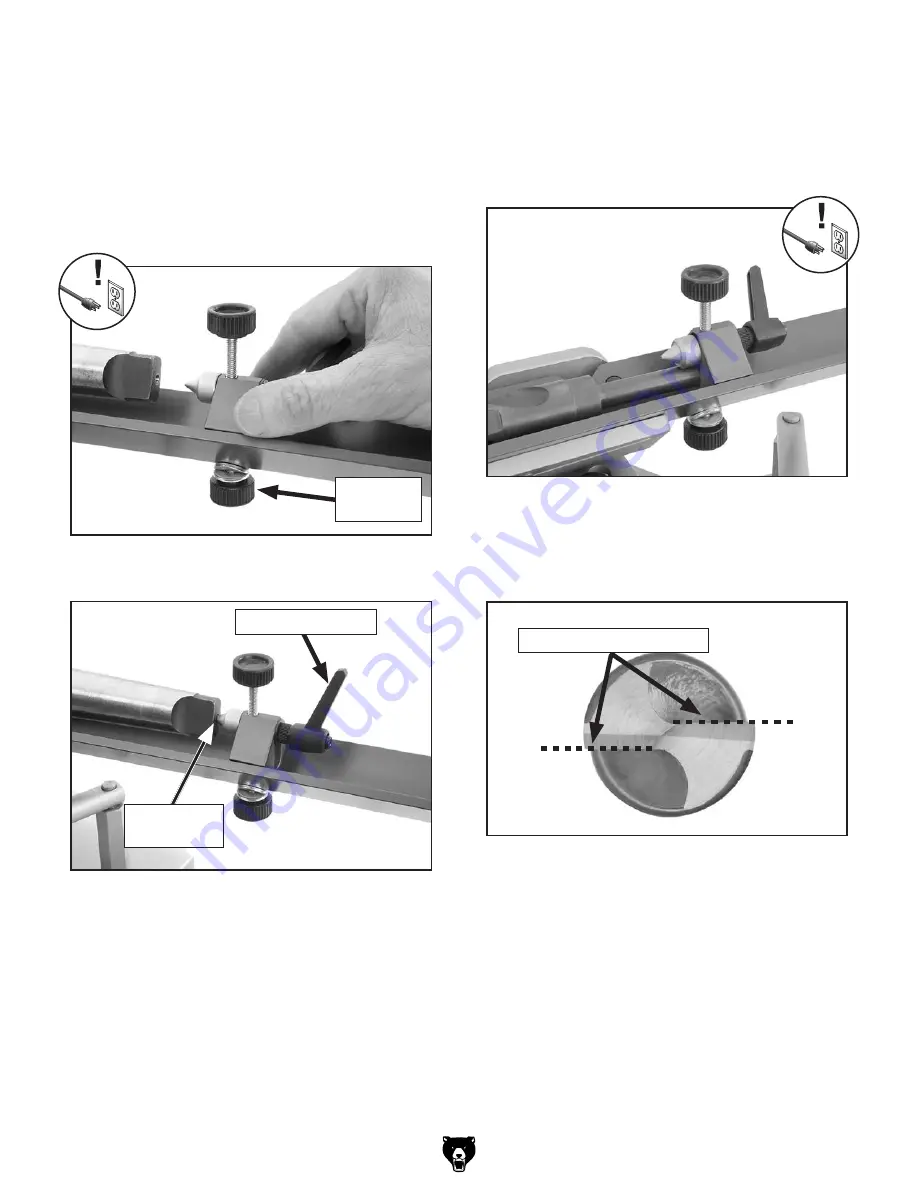
Model G0686 (Mfd. Since 01/15)
-23-
8. Position and secure the tailstock up against
the back of the bit so that it will not move away
from the grinding wheel during operation.
—
If the bit shank is center-drilled: Insert
the tailstock center point into the bit shank
center-drilled hole, then tighten the tailstock
bottom lock knob and height lock lever to
secure the setting (see
Figures 21–22).
Figure 21. Aligning the tailstock with the center-
drilled hole of the bit shank.
Bottom
Lock Knob
Figure 22. Tailstock in the correct position
against the center-drilled shank.
Tailstock
Center Point
Height Lock Lever
9. Rotate the bit so that the cutting edges are
horizontal, as shown in
Figure 24.
—
If the bit shank is not center-drilled:
Raise the tailstock center point above the
bit shank and lock it in place. Then, move
the tailstock base up against the bit shank
and tighten the bottom lock knob to hold it
in place, as shown in
Figure 23.
Figure 23. Tailstock in proper position against a
bit shank that is not center-drilled.
Figure 24. Bit rotated so that the cutting edges
are horizontal.
Cutting Edges Horizontal
Summary of Contents for G0686
Page 41: ......
Page 44: ...REVISED ...