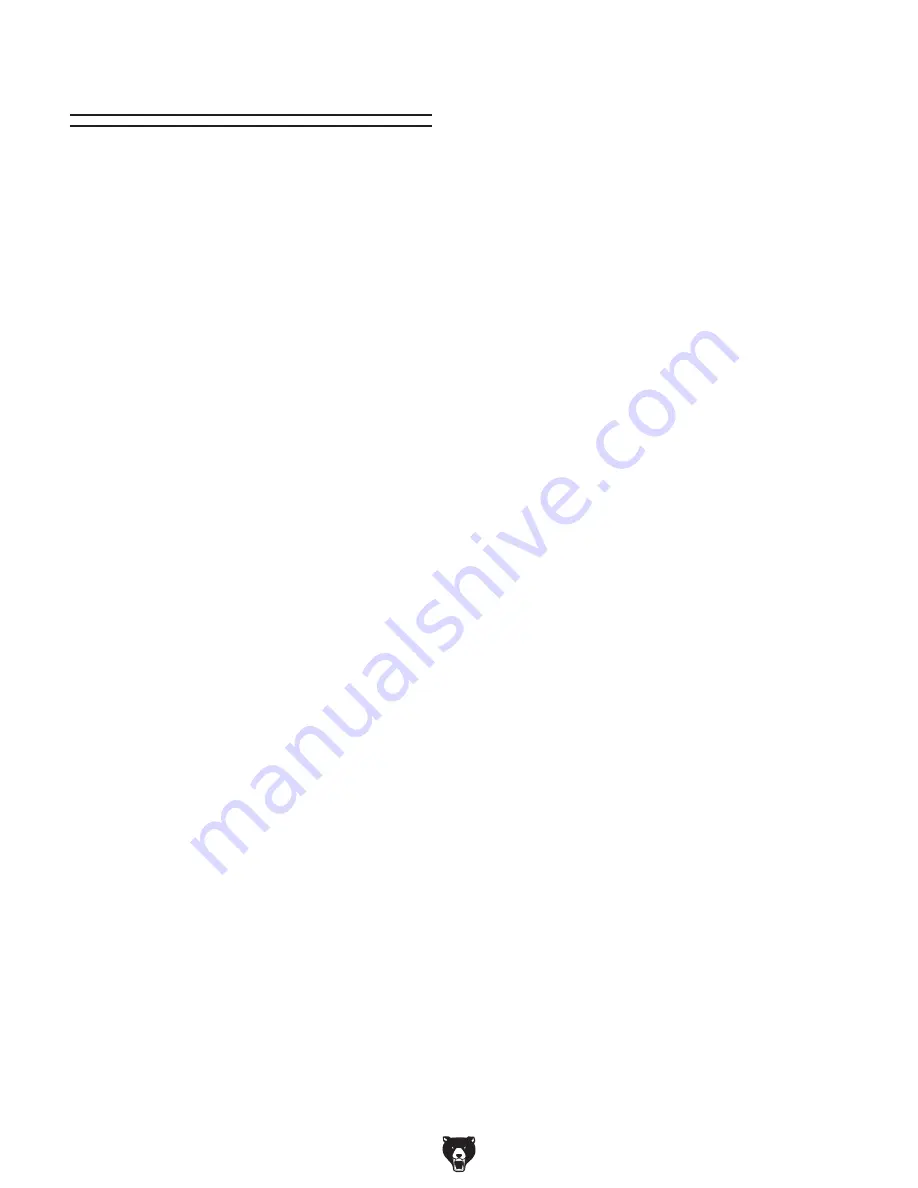
-26-
Model G0555XH
(Mfd. Since 1/18)
Tensioning Blade
The Flutter Method
A properly tensioned blade is essential for mak-
ing accurate cuts, maximizing blade life, and
making other bandsaw adjustments. However, a
properly tensioned blade will not compensate for
cutting problems caused by excessive feed rate,
hardness variations between workpieces, and
improper blade selection.
Optimal cutting results for any type of workpiece
are achieved through a combination of correct
blade selection, proper blade tension, properly
adjusted blade guides and other bandsaw compo-
nents, and using an appropriate feed rate.
Improper blade tension is unsafe, produces inac-
curate and inconsistent results, and introduces
unnecessary wear on bandsaw components.
Over-tensioning the blade increases the chance
of the blade breaking or wheel misalignment.
Under-tensioned blades wander excessively
while cutting and will not track properly during
operation.
The method used to tension the blade is often
a matter of preference. This manual describes
two methods: the flutter method and the deflec-
tion method. Either method will help you properly
tension the blade. Experience and personal pref-
erence will help you decide which method you
prefer.
Note: Tensioning the blade before the Test Run
was an approximate tension. The following proce-
dures fine-tune the blade tension.
Using the flutter method, you intentionally loosen
the blade until it just passes the point of being
too loose (when it begins to flutter). Then you
gradually tighten the blade until proper tension is
reached.
1. DISCONNECT MACHINE FROM POWER.
2. Make sure blade is properly center tracking
(refer to
Blade Tracking on Page 23 for
instructions).
3. Raise guide post all the way up and move
upper and lower guide bearings away from
blade.
4. Engage blade tension quick release lever to
apply tension to blade.
10. Re-adjust
blade
guides
(refer
to
Adjusting Blade Support Bearings and
Adjusting Blade Guide Bearings on
Pages 27– 28 for instructions).
9. Disconnect bandsaw from power.
5. Connect bandsaw to power, and turn bandsaw
ON.
6. Using blade tension adjustment knob, slowly
decrease blade tension until you see the
blade start to flutter.
7. Slowly increase tension until blade stops flut-
tering, then tighten blade tension adjustment
knob and additional
1
⁄
8
to
1
⁄
4
turn.
8. View tension gauge and use that as a guide
for tensioning that specific blade size in the
future.
Note: Do not rely on this setting for other
blades or for long periods of time because all
blades require specific tensioning and stretch
with use. If you notice a decrease in perfor-
mance at the setting repeat this procedure.
With extended use, blade tensioning system
may need to be reset. Refer to
Resetting
Blade Tensioner in the Service section in
this manual for details.
To tension bandsaw blade using flutter
method:
Summary of Contents for G0555XH
Page 72: ......