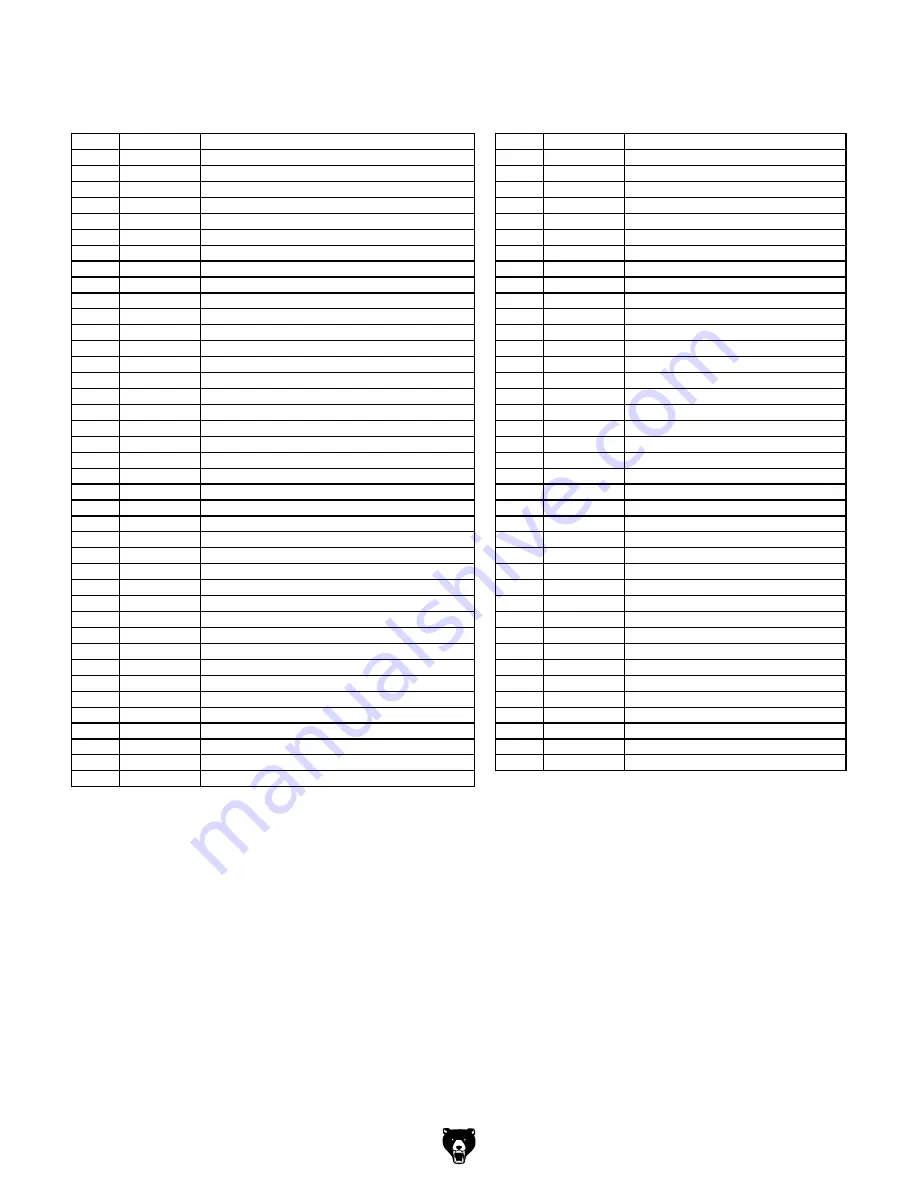
-40-
Model G0524 (Mfd. Since 7/16)
Motors & Conveyor Track Parts List
REF
PART #
DESCRIPTION
REF
PART #
DESCRIPTION
101
P0524101
PULLEY EYE BOLT M16-2 X 90 LH
137
P0524137
PHLP HD SCR 1/8-40 X 3/4
102
P0524102
HEX NUT M16-2 LH
138
P0524138
CONVEYOR BODY
103
P0524103
PULLEY COUPLING NUT M16-2 LH/RH
138-1
P0524138-1
CAT. BLOCK FITTED BAKELITE
104
P0524104
STUD-FT M16-2 X 110
139
P0524139
BRUSH L-BRACKET (RH)
105
P0524105
HEX NUT M16-2
140
P0524140
BALL OILER 1/8 NPT THREADED
106
P0524106
MOTOR LIFTING RING
141
P0524141
IDLE WHEEL
107
P0524107
MOTOR PULLEY
142
P0524142
PILLOW BLOCK BEARING
108
P0524108
SET SCREW M8-1.25 X 16
143
P0524143
HEX BOLT M12-1.75 X 30
109
P0524109
V-BELT A55
144
P0524144
EXT RETAINING RING 12MM
110
P0524110
KEY 10 X 8 X 70
145V2
P0524145V2
BLOCK PIVOT SHAFT 74MM V2.01.12
111V3
P0524111V3
CONVEYOR MOTOR 2HP 220V/440V 3-PH V3.07.16
146V2
P0524146V2
ENTIRE FEED CHAIN ASSY V2.01.12
111V3-1 P0524111V3-1 MOTOR FAN COVER
146V2-1 P0524146V2-1 SINGLE LINK FOR FEED CHAIN V2.01.12
111V3-2 P0524111V3-2 MOTOR FAN
147
P0524147
BAKELITE PLASTIC INSERT
111V3-3 P0524111V3-3 MOTOR JUNCTION BOX
148
P0524148
IDLER WHEEL AXLE
111V3-4 P0524111V3-4 BALL BEARING 6205LLB
149
P0524149
CAP SCREW M8-1.25 X 25
111V3-5 P0524111V3-5 BALL BEARING 6204 CM LLB
150
P0524150
BLADE MOTOR MOUNT PIVOT SHAFT
112
P0524112
KEY 8 X 8 X 40
151
P0524151
LOCK COLLAR
113
P0524113
REDUCER PULLEY
152V3
P0524152V3
MOTOR 15HP 220V/440V 3-PH V3.07.16
114
P0524114
KEY 7 X 7 X 45
152V3-1 P0524152V3-1 MOTOR FAN COVER
115
P0524115
LOCK WASHER 12MM
152V3-2 P0524152V3-2 MOTOR FAN
116
P0524116
HEX BOLT M12-1.75 X 40
152V3-3 P0524152V3-3 MOTOR JUNCTION BOX
117
P0524117
REDUCER WORM GEAR
152V3-4 P0524152V3-4 BALL BEARING 6308 CM LLB
118
P0524118
REDUCER PULLEY
152V3-5 P0524152V3-5 BALL BEARING 6308 CM LLB
119
P0524119
COGGED BELT 1922V30-22
153
P0524153
MACHINE ID LABEL
120
P0524120
CONVEYOR MOTOR PIVOT SHAFT
154
P0524154
KEEP COVER CLOSED LABEL
121
P0524121
HEX NUT M12-1.75
155
P0524155
KICKBACK LABEL
122
P0524122
STUD-FT M12-1.75 X 100
156
P0524156
SAFETY GLASSES
123
P0524123
FLAT WASHER 12MM
157
P0524157
UNPLUG LABEL 220V
124
P0524124
CONVEYOR MOTOR MOUNT
158
P0524158
READ MANUAL
125
P0524125
FLAT WASHER 12MM
159
P0524159
INFEED HAND LABEL
126
P0524126
LOCK WASHER 8MM
160
P0524160
TRAINING LABEL
127
P0524127
HEX BOLT M8-1.25 X 25
161
P0524161
ELECTRICITY
128
P0524128
HEX BOLT M10-1.5 X 35
162
P0524162
HANGING BUTTON LABEL
129
P0524129
LOCK WASHER 10MM
163
P0524163
ARBOR ROTATION LABEL
130
P0524130
BLADE MOTOR MOUNT
164
P0524164
GREASE FITTING LABEL
131
P0524131
HEX NUT M10-1.5
165
P0524165
LUBRICANT OIL LABEL
132
P0524132
SPROCKET 10T
166
P0524166
GEAR OIL LABEL
133
P0524133
KEY 10 X 8 X 30
167
P0524167
GRIZZLY.COM LABEL
134
P0524134
BRUSH
168
P0524168
MODEL NUMBER LABEL
135
P0524135
BRUSH L-BRACKET (LH)
169
P0524169
PREWIRED 220V LABEL
136
P0524136
HEX BOLT M10-1.5 X 30
Summary of Contents for G0524
Page 60: ......