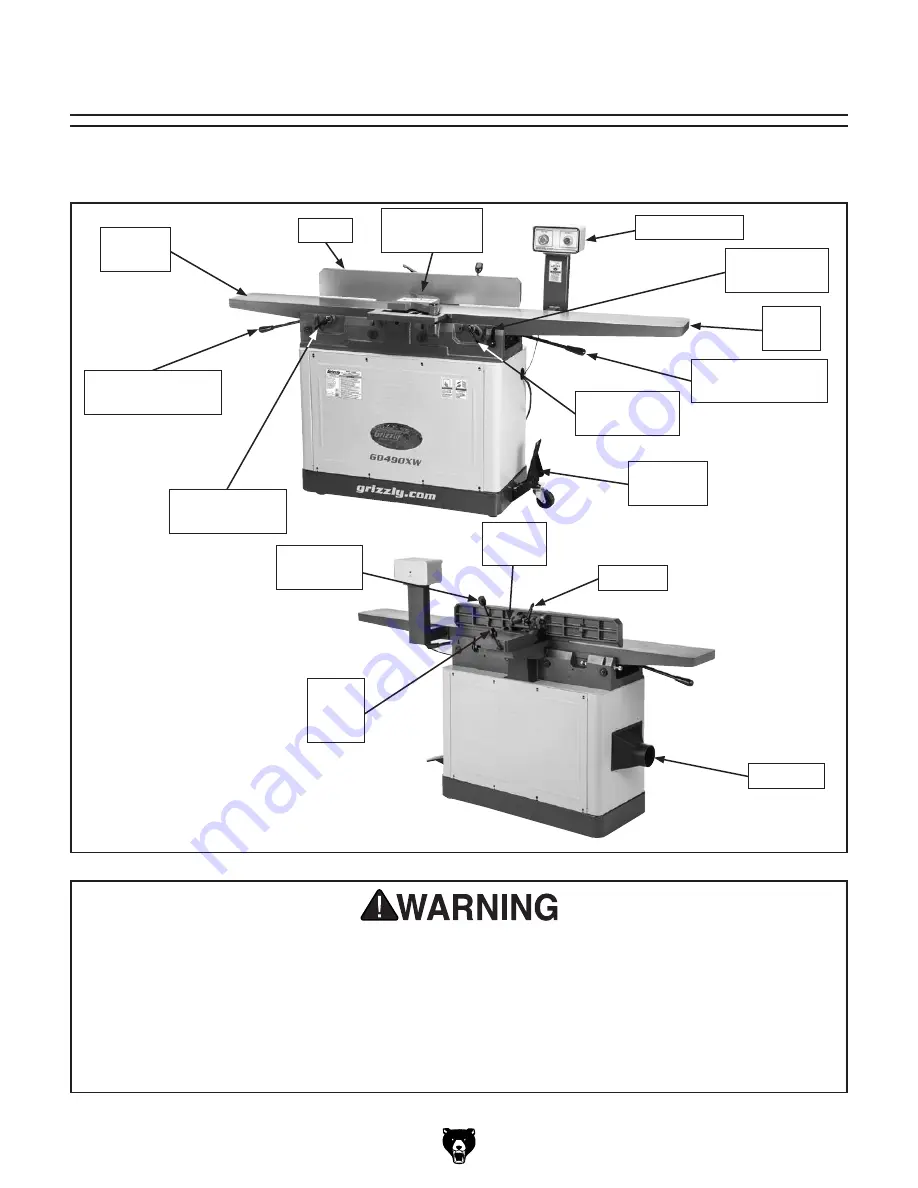
Model G0490W/G0490XW (Mfd. Since 5/16)
-3-
Identification
Become familiar with the names and locations of the controls and features shown below to better understand
the instructions in this manual.
Infeed
Table
Infeed Table
Adjustment Lever
Fence
Outfeed
Table
Outfeed Table
Adjustment Lever
Infeed Table
Lock
For Your Own Safety Read Instruction Manual Before Operating Jointer
a) Wear eye protection.
b) Always keep cutterhead and drive guards in place and in proper operating condition. ALWAYS
replace cutterhead guard after rabbeting operations.
c) Never make jointing or rabbeting cuts deeper than
1
⁄
8
" or planing cuts deeper than
1
⁄
16
"
d) Always use hold-down or push blocks when jointing material narrower than 3" or surface
planing material thinner than 3".
e) Never perform jointing, planing, or rabbeting cuts on pieces shorter than 8" in length.
Dust Port
Outfeed Table
Lock
Pedal
Assembly
Control Panel
Tilt Lock
Fence Tilt
Handle
Tilt
Plunger
Cutterhead
Guard
Depth-of-Cut
Scale
Fence
Lock
Lever
Summary of Contents for G0490W
Page 64: ......