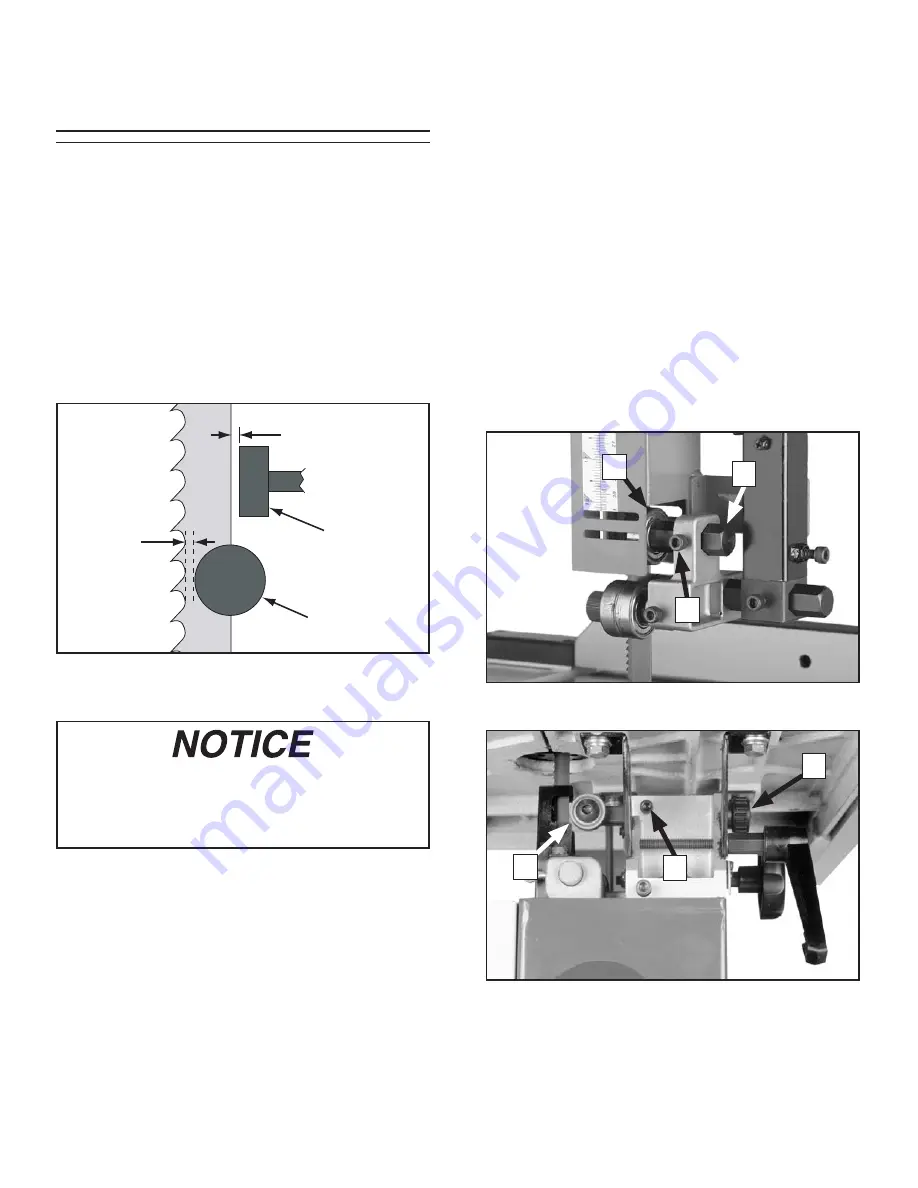
Page 10
G0513 Series Bandsaws
-35-
Adjusting Blade
Support Bearings
Before adjusting the blade support bear-
ings, make sure the blade is tracking prop-
erly (
Page 28
) and that it is correctly ten-
sioned (
Page 33
).
Support bearings stop excessive backward deflec-
tion of the blade from the advancing workpiece.
The proper adjustment of the support bearings
is an important part of making accurate cuts and
prevents damage to the blade teeth from contact
with the blade guides.
It is important that the distance of the support
bearing behind the blade is the same as the dis-
tance of the blade guides behind the teeth gullets,
which is typically about 0.016" (see
Figure 45
).
%#%&+
<Ve
%#%&+
<Ve
Hjeedgi
7ZVg^c\
7aVYZ
<j^YZ
Figure 45.
Distance settings of upper support
bearings and blade guides.
Tools Needed
Qty
Hex Wrench 5mm .............................................. 1
Feeler Gauge 0.016" .................................1 Each
Crisp Dollar Bill (Optional) ................................. 1
Tip:
You can use a crisp dollar bill in place of the
feeler gauge for the following procedures. The
thickness of the bill when folded in half twice is
approximately 0.016".
Refer to
Figures 46–47
and the following descrip-
tions to become familiar with the controls to adjust
the support bearings. Then, adjust the surface of
the support bearings approximately 0.016" behind
the blade.
Note:
The support bearing controls are similar for
all models.
Figure 46.
Upper support bearing controls.
A
C
B
Figure 47.
Lower support bearing controls.
C
D
A