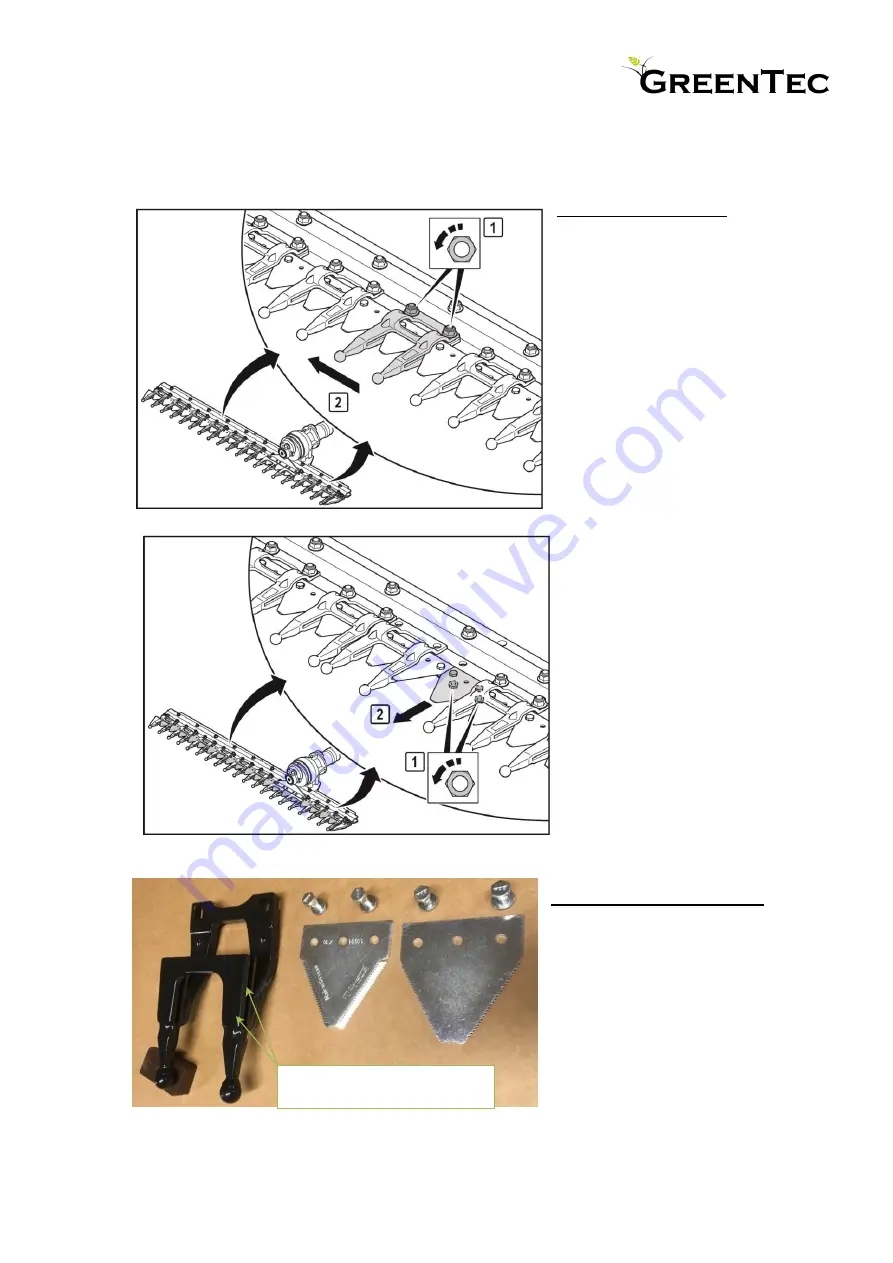
Greentec HL152- 242 Cutterbar
29
Parts replacement
Replacing sections
In case of breakage, single sections of the installed knives can be replaced.
Removing a section
►
Unscrew the nut of the
double guard on the damaged
section and remove the bolts.
►
Push the double guard to
the side in order to access the
knife bolts
►
Loosen the nuts on the
damaged section and tap the
serrated stud bolts to remove
them.
►
Remove the section from
the knife.
Installing the blade tooth
INFO:
As the cutterbar’s fingers
are supplied with a double
cutting edge
(on the topside and the
underside)
, the blade teeth can
be turned in both directions.
Double fingers with double cutting
edge
(on the topside and the underside)