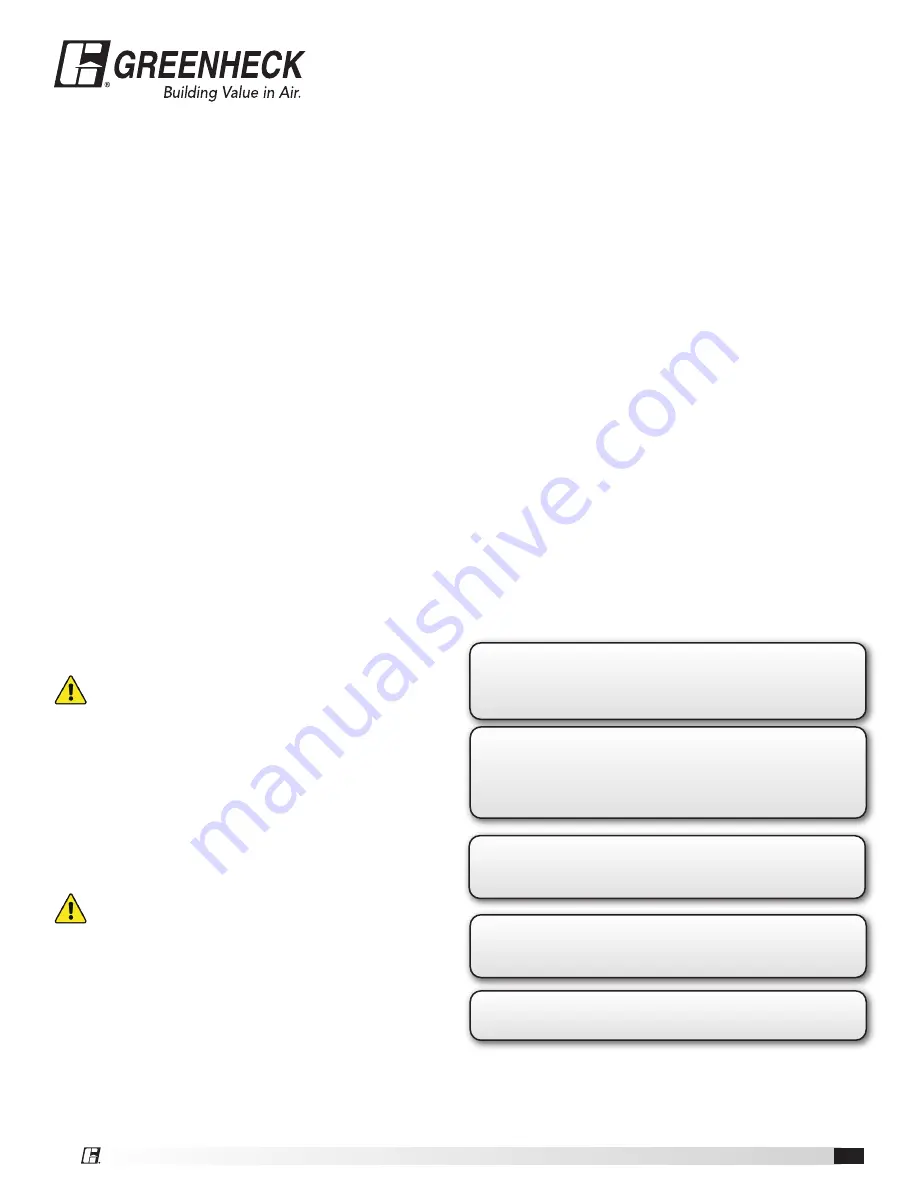
XG-Fan Powered Air Terminals Rev 2
4
Field Electrical Wiring
5
All field wiring must comply with local building codes and
NEC. (ANSI/NFPA 70-2002)
5
When Applicable, electrical control and piping diagrams are
attached to the inside of the control enclosure cover of the
XG-Fan Powered Air Terminal.
5
Use copper only conductors.
5
The XG-Fan Powered Air Terminal must be properly grounded
per NEC 424-14 and 250.
5
Always check product label for voltage and current data to
determine the proper wire size and over current protection.
5
The control cabinet contains live electrical parts.
5
Contacting these parts with power applied may cause seri-
ous injury or even death.
5
The control panel cover must be closed or in place before
applying electric power to the XG-Fan Powered Air Terminal.
5
These recommendations are not meant to precluded NEC
requirements or applicable local building codes and are the
sole responsibility of the installing contractor.
XG-Fan Powered Air Terminals with Electric Reheat
•
Always inspect the electric heating coils for damage prior to
installing the XG-Fan Powered Air Terminal.
•
All electric reheat is balanced by kW per stage.
•
The installing electrician should rotate these electric reheat
stages by phase in order to balance the buildings electrical
load.
•
The “
UP
” arrow orientation must be followed to prevent nui-
sance tripping or over heating which will cause damage to
the electric heater and or building.
•
Motor fusing is provided on all XG-Fan Powered Air Terminals.
Caution:
XG-Fan Powered Air Terminals must not be
operated without downstream duct work in place. Failure
to have downstream ductwork installed will expose the
line voltages and high temperature present in the operating
heater elements. Contact with these heater elements may
cause serious injury or death.
XG-Fan Powered Air Terminals with Hot Water Coils
•
Always inspect the hot water coils for damage prior to install-
ing the XG-Fan Powered Air Terminal.
Caution:
The copper tubing should not be used
as lift points.
•
The hot water coil casing must be field insulated.
•
The hot water coils do not have drip pans and are not suit-
able for use as cooling coils.
Controls
For information on controls provided by other manufactures and
installed on the Air Terminals, contact the local branch or dealer.
Important
XG-Fan Powered Air Terminals with digital controls, if factory pro-
grammed, incorporate specific communication addresses. Installing
the XG-Fan Powered Air Terminal in a different location than noted
on the XG-Fan Powered Air Terminal label and building plans,
may result in excessive start up labor and is the sole responsibility
of the contractor.
Inlet Flow Sensor
XG-Fan Powered Air Terminals are shipped with factory
installed (where applicable) pressure differential inlet flow sensors
in the primary inlet.
See figure 3
for calibration curve and K
factors. Model BP600 Air Terminals offer an optional downstream
flow sensor for field installation a minimum of 3 feet downstream
of box discharge.
Labeling
XG-Fan Powered Air Terminals are shipped from the factory with
multiple information labels.
Control Sequence Label:
Affixed to the inside of the control
enclosure cover. Displays piping/wiring diagram, control
sequence number and any optional components.
Terminal I.D. Label:
Affixed to the outside of the control
enclosure cover. Shows tagging, representative name, sales
order number, applicable certifications, model number, Made
in USA, any applicable electrical data and UL compliance
markings.
AHRI Certification Label:
Identifies applicable industry test
standard and certifies XG-Fan Powered Air Terminal is in
compliance.
AHRI Certification on Hot Water Coil
(if applicable)
:
Identi-
fies applicable industry test standard and certifies hot water
coil compliance.
Orientation Label:
Identifies the proper air flow direction
and top of XG-Fan Powered Air Terminal.