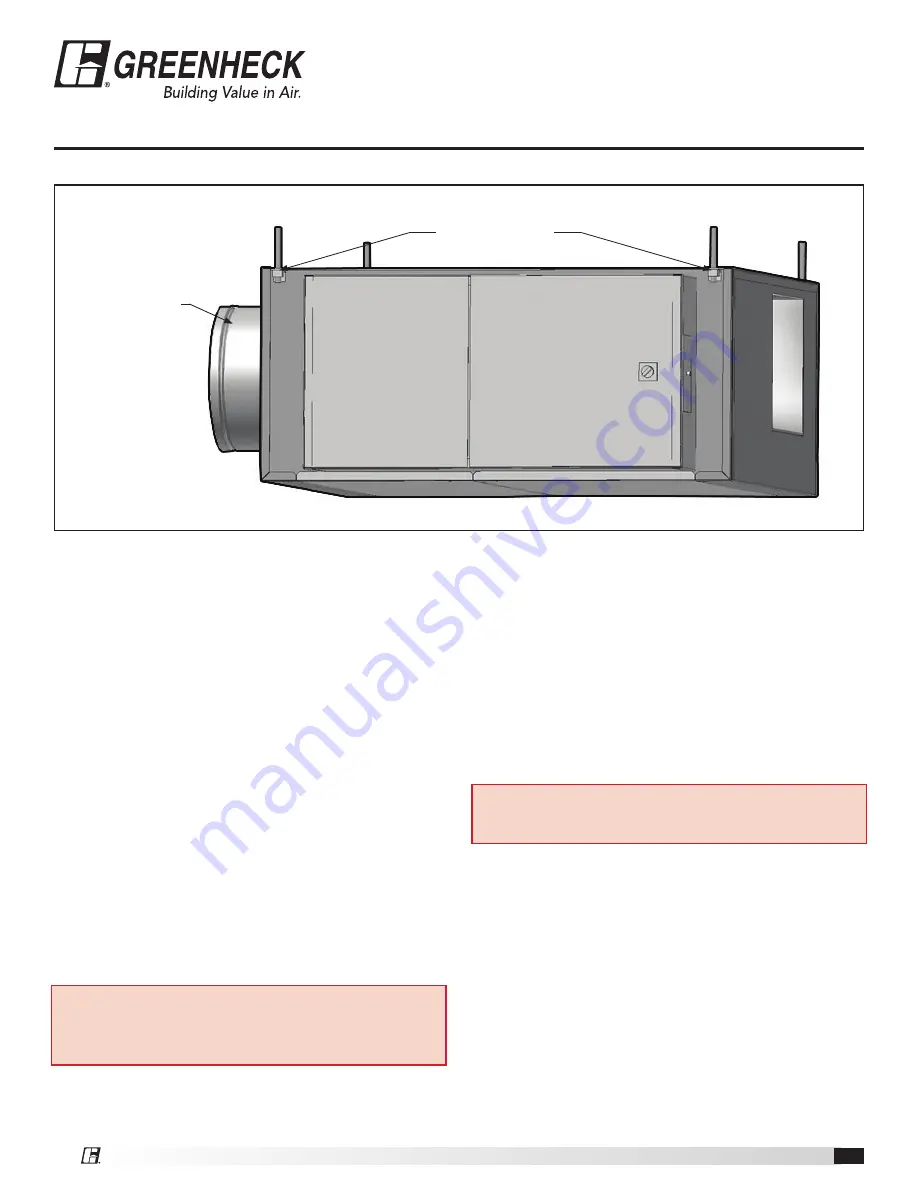
XG-Fan Powered Air Terminals Rev 2
3
Figure 2 Optional Hanger Brackets and Hanger Rods
Important
If equipped with pneumatic controls, the orientation of the XG-
Fan Powered Air Terminal unit is critical. The pneumatic controls
must be mounted right side up. The XG-Fan Powered Air Ter-
minal must be level or – 10 degrees of horizontal, both
parallel to the air flow and at right angle of air flow. The control
side of the XG-Fan Powered Air Terminal is labeled with an arrow
indicating up. Unless otherwise noted, most electric, analog elec-
tronic and digital are not position sensitive and may be installed in
any orientation.
Minimum Clearance for Access
XG-Fan Powered Air Terminals require sufficient space to allow
servicing of the controls, motor/blower and electric reheat (if
applicable) and single point power hook up. A minimum of 3”of
vertical clearance is required below the bottom of the unit. Hori-
zontal clearance requirements are dependent upon access panel
dimensions which are indicated on the appropriate submittal. For
control panel access, a minimum of 18” is recommended. See the
appropriate submittal for control panel location.
Note
:
These clearances recommendations are not meant
to preclude NEC requirements or local building codes that
may be applicable, which are the responsibility of the installing
contractor.
Connecting Duct Work
1. Slip each inlet duct over the inlet collar of the XG-Fan
Powered Air Terminal.
2. Fasten and seal the connection by method prescribed by
job specification.
3. The diameter of the inlet duct in inches, must be equal
to the listed size of the Fan Powered Air Terminal; e.g. a
duct that actually measures 8 inches must be fitted to a
size 8 inch XG-Fan Powered Air Terminal. The inlet tube
of the XG-Fan Powered Air Terminal is manufactured
1/8” smaller than the listed size in order to fit inside
the duct.
Note
:
Do not insert duct work inside the inlet collar of the
XG-Fan Powered Air Terminal. Inlet duct should be installed
in accordance with SMACNA guidelines.
4. If an inlet air flow sensor is installed, it is recommend-
ed the installer provide a minimum of 3 duct diameters
of straight duct at the XG-Fan Powered Air Terminal
inlet.
5. The outlet end of the XG-Fan Powered Air Terminal is
designed for use with connections flanged outlets.
(Slip and drive duct connections optional.)
6. A rectangular duct the size of the Air Terminal outlet
should be attached.
(Refer to submittal for correct size.)
Hanger brackets and Rod
(5/16” minimum)
Primary air inlet