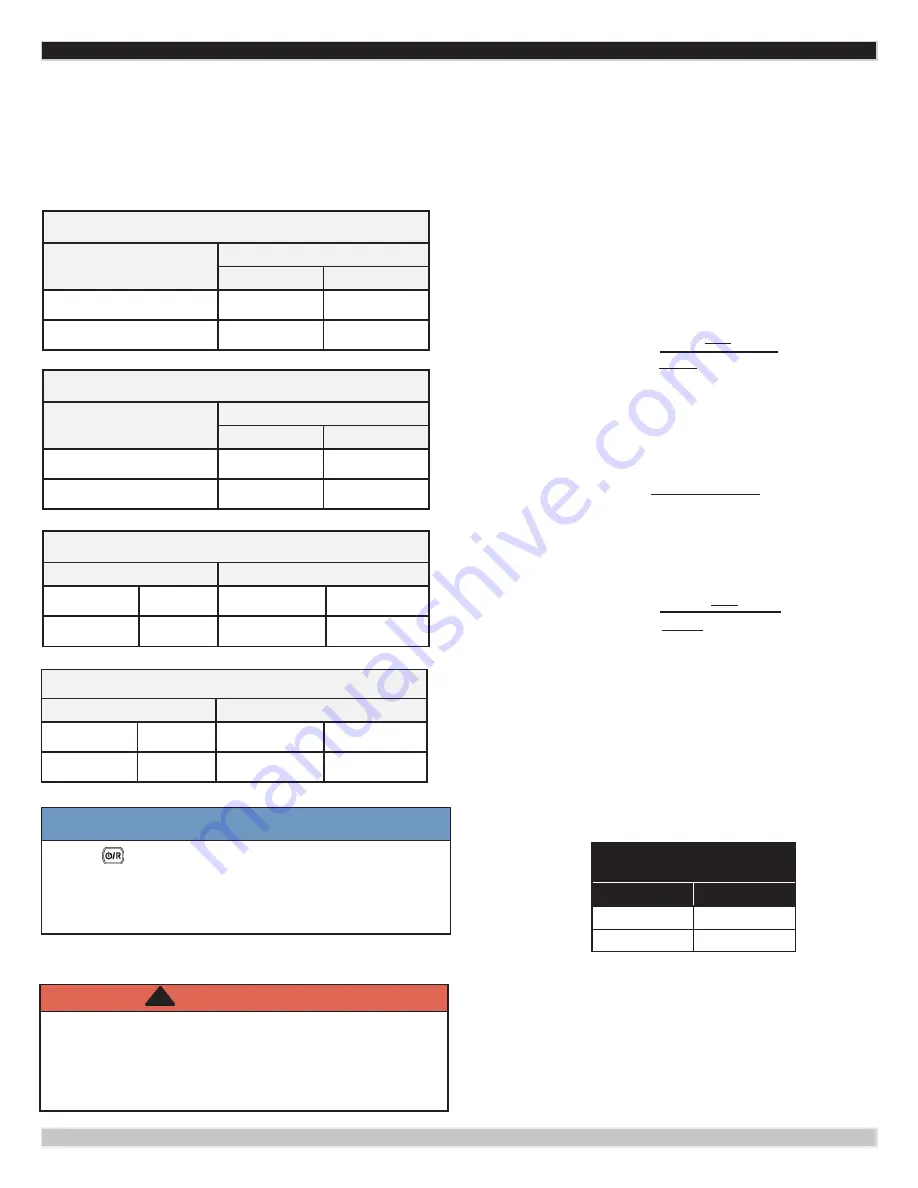
52
O
2
/CO
2
Values at Low-Fire Natural Gas (A)
Nominal value
Permitted value
O
2
%
CO
2
%
O
2
%
CO
2
%
5.7
8.5
5.4 - 6.1
8.3 - 8.7
O
2
/CO
2
Values at Low-Fire Propane Gas (E)
Nominal value
Permitted value
0
2
%
CO
2
%
0
2
%
CO
2
%
6.4
9.6
6.1 - 6.70
9.4 - 9.8
CO
2
Values Natural Gas (A) at High Fire
Front Panel
CO
2
%
Nominal
Range
ON
9.3
9.1 - 9.5
OFF*
8.9
8.5 - 9.0
CO
2
Values Propane Gas (E) at High Fire
Front Panel
CO
2
%
Nominal
Range
ON
10
9.8 - 10.2
OFF*
9.6
9.2 - 9.7
9.12 Chimney Sweep Function (CO
2
Adjust)
For correct boiler operation, content of (CO
2
- O
2
) in the
combustion flue must be within tolerances indicated in table
below.
COMBUSTION TABLE
NOTICE
• Press
to display instantaneous flow temperature for
15 seconds.
• Use a regularly calibrated combustion analyzer for
combustion analysis.
WARNING
Fire, explosion, and asphyxiation hazard! Boiler is set
for natural gas from the factory. If propane is to be used
the gas valve must be adjusted before turning boiler on.
Failure to follow these instructions could result in death
or serious injury.
!
9.13 Check Firing Rate
1.
Measure input, if a gas meter is installed in the system.
• Turn off gas to all other appliances.
• Activate some heating zones to dissipate heat.
• Set boiler on high fire using Chimney Sweep Function.
• Use ½, 1 or 2 cu ft dial on gas meter. Measure time
required for two or more complete revolutions. Measure
time
for one or more minutes.
• Calculate input.
For Metric formulas- See Glossary
For Natural Gas :
Input (MBH)
=
3600 x cu ft
seconds
Example: Natural Gas - Gas flow from
Meter = 2 cu ft
Measured time = 72 seconds
=
3600 x 2 cu ft
= 100 MBH
72 seconds
For Propane (LP):
Input (MBH)
=
9160 x cu ft
seconds
Input Rate (MBH)
Approximate Rate @
100% Fire (MBH)
Size
GMHB227
227
GMHB380
380
2.
Compare measured input to Table below. If calculated
input is not in range given in Table below, check firing
rate again after setting the combustion following steps in
section 9.18.
Table 9-2 Input Rate @ High Fire (MBH)
PN 240012369, REV A [08/31/2018]
9 - START UP PROCEDURE