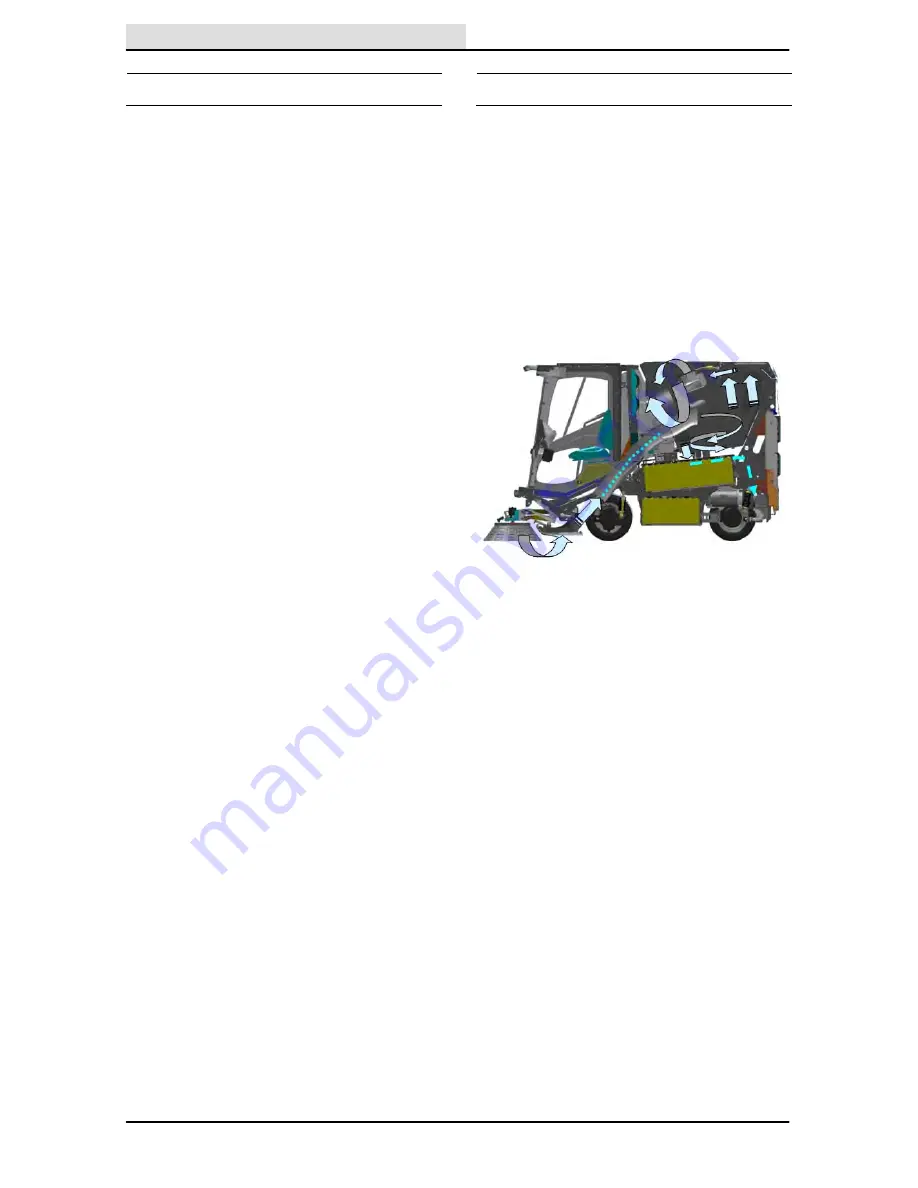
OPERATION
28
500ze YM180 (12
−
2011)
BRUSH INFORMATION
For best results, use the correct brush type for the
cleaning application.
NOTE: The amount and type of soilage play an
important role in determining the most effective
type of brushes to use. Contact an authorized
service representative for specific
recommendations.
Polypropylene Brush
−
Best overall general
cleaning brush. The bristles fan out and dig into
cracks to remove debris.
Polypropylene and Wire Brush
−
Recommended for moving heavy debris. Best
bristle mix for moving large quantities of sand and
heavier debris. The bristles fan out similar to the
polypropylene brush. The wire bristles provide the
ability to move heavier material.
PET (Polyethylene Terephthalate) Heavy Duty
Brush
−
Recommended for areas where there is
a heavy build up of debris. The stiffer / thicker
bristles provide more aggressive digging action to
remove compacted debris from along buildings,
curbs, and in corners.
HOW THE MACHINE WORKS
The two front brushes move debris to the center
of the machine and the vacuum pulls the debris
into the hopper. The airflow must be maintained
through the machine to keep it functioning
properly.
The air and debris swirl in a cyclonic rotation
inside the hopper. The dust and debris drops to
the bottom of the hopper and the air exits through
vents at the rear of the machine. Screens located
in the hopper prevent light debris (leaves, paper,
etc...) from exiting the hopper and the cyclone
assemblies located at the top of the hopper
prevent dust particles from exiting the hopper.