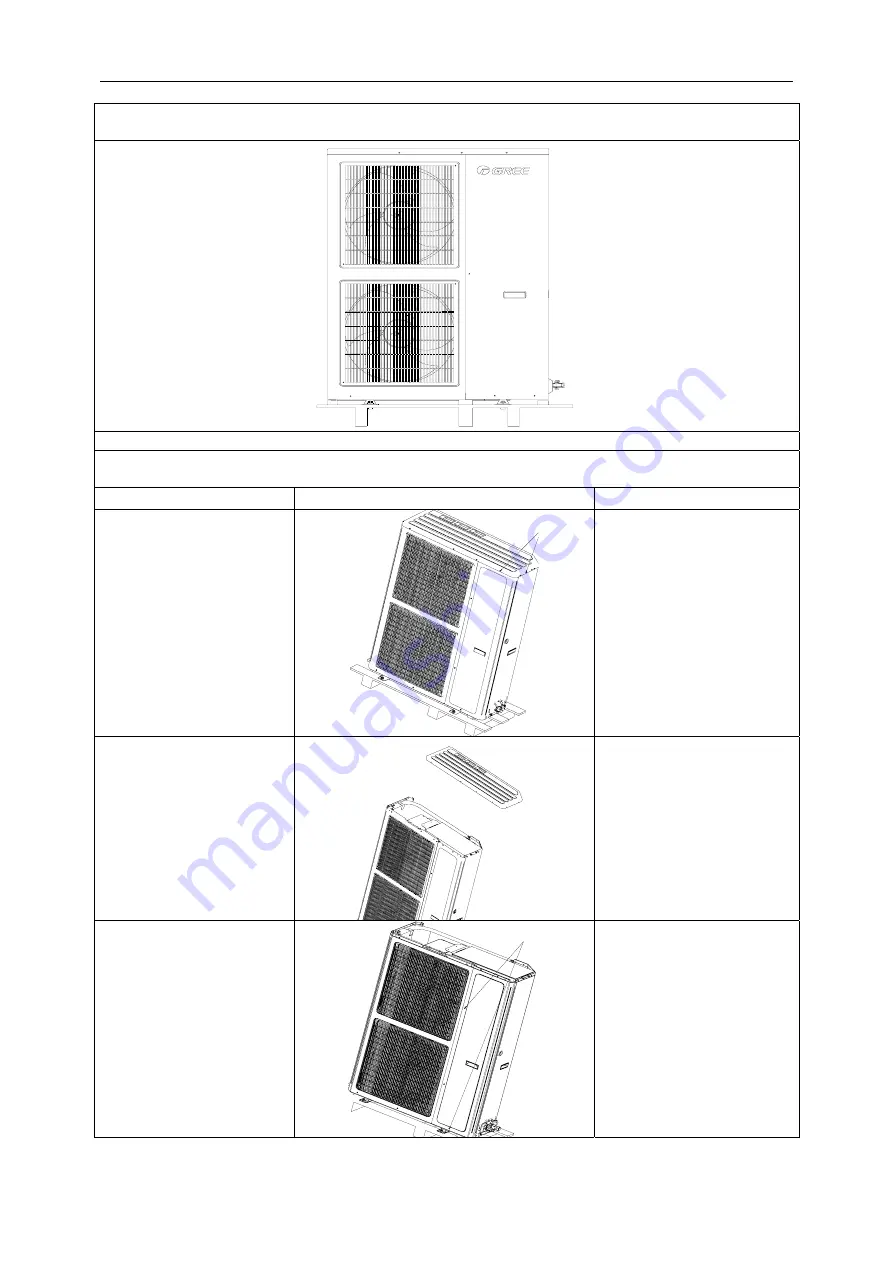
A/A DC INVERTER U-MATCH AIR CONDITIONERS MAINTENANCE
191
Double-fan Inverter Outdoor Unit, applicable toGUHD48NK3CO
/
GUHD48NM3CO
/
GUHD60NM3CO
Disassembly and Assembly of external casing
Remark : Before removing the outer housing, make sure that the unit has been cut off from the
power supply.
Step Illustration
Handling
Instruction
1.Diassemble the top cover.
A
.先切断电源;
B
.妥善回收冷媒;
C
.再用螺丝刀拧下固定顶盖板
的螺钉。
2.Remove the top cover
Move the top cover from the
unit.
3. Diassemble the front side
plate,
Looson the screws on the front
side plate.
Summary of Contents for U-MATCH GFH09K3CI
Page 4: ...GREE COMMERCIAL AIR CONDITION A A DC INVERTER U MATCH AIR CONDITIONERS 1 PRODUCT...
Page 25: ...GREE COMMERCIAL AIR CONDITION A A DC INVERTER U MATCH AIR CONDITIONERS 22 CONTROL...
Page 27: ...A A DC INVERTER U MATCH AIR CONDITIONERS CONTROL 24 1 2 Heating Operation...
Page 62: ...GREE COMMERCIAL AIR CONDITION A A DC INVERTER U MATCH AIR CONDITIONERS 59 5 3 7 Dimensions...
Page 63: ...GREE COMMERCIAL AIR CONDITION A A DC INVERTER U MATCH AIR CONDITIONERS 60 INSTALLATION...
Page 102: ...GREE COMMERCIAL AIR CONDITION A A DC INVERTER U MATCH AIR CONDITIONERS 99 MAINTENANCE...
Page 121: ...A A DC INVERTER U MATCH AIR CONDITIONERS MAINTENANCE 118 IPM module protection...
Page 122: ...A A DC INVERTER U MATCH AIR CONDITIONERS MAINTENANCE 119 DC busbar overvoltage protection...
Page 123: ...A A DC INVERTER U MATCH AIR CONDITIONERS MAINTENANCE 120 DC busbar undervoltage protection...
Page 124: ...A A DC INVERTER U MATCH AIR CONDITIONERS MAINTENANCE 121 Abnormal noise from PFC inductor...
Page 125: ...A A DC INVERTER U MATCH AIR CONDITIONERS MAINTENANCE 122 Radiator overheat protection...
Page 126: ...A A DC INVERTER U MATCH AIR CONDITIONERS MAINTENANCE 123 Tripping...
Page 130: ...A A DC INVERTER U MATCH AIR CONDITIONERS MAINTENANCE 127 Tripping...
Page 138: ...A A DC INVERTER U MATCH AIR CONDITIONERS MAINTENANCE 135 Model GUHD48NM3CO Model GUHD60NM3CO...
Page 183: ...A A DC INVERTER U MATCH AIR CONDITIONERS MAINTENANCE 180 7 8 A B C 9 A B 0 5 0 1kgf c C 10 A B...
Page 195: ...A A DC INVERTER U MATCH AIR CONDITIONERS MAINTENANCE 192 4 5 6...
Page 197: ...A A DC INVERTER U MATCH AIR CONDITIONERS MAINTENANCE 194 5 6 A B 0 5 0 1kgf c C 7 8 A B C...
Page 227: ...A A DC INVERTER U MATCH AIR CONDITIONERS MAINTENANCE 224 Model GUHD24NK3CO Exploded View...
Page 247: ...A A DC INVERTER U MATCH AIR CONDITIONERS MAINTENANCE 244 Model GKH18K3CI Exploded View...
Page 264: ...261 JF00300705...