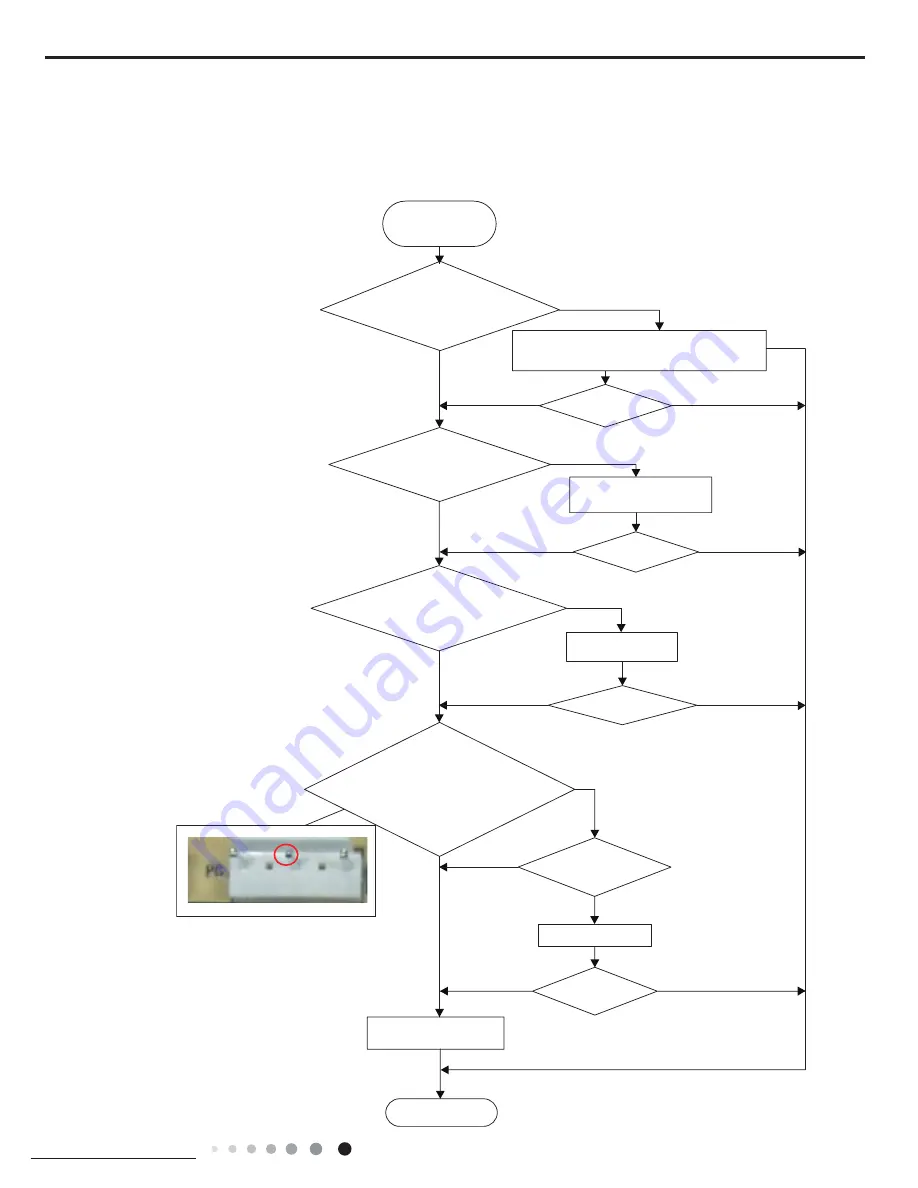
65
Installation and Maintenance
Service Manual
(2) Malfunction of Blocked Protection of IDU Fan Motor H6
Main detection points:
● SmoothlyIs the control terminal of PG motor connected tightly?
● SmoothlyIs the feedback interface of PG motor connected tightly?
● The fan motor cant operate?
● The motor is broken?
● Detectioncircuit of the mainboard is defined abnormal?
Malfunction diagnosis process:
Start
While power is off stir the blade
with a tool to see whether the
blade rotates smoothly
Check if the connection of PG
motor feedback terminal is firm
Check if the connection of PG
motor control terminal is firm
Turn on the unit again; measure
whether the output voltage on
control terminal for PG motor is
more than 50V within 1 min after
the louvers are opened
Tighten the screw; reassemble the blade, motor
and shaft bearing rubber base sub-assy to make
sure there is no foreign object between them
Yes
Yes
Yes
Yes
Yes
Yes
Yes
Yes
Yes
Yes
No
No
No
No
No
No
No
No
No
Is malfunction
eliminated
Is malfunction
eliminated
Is malfunction
eliminated
Is malfunction
eliminated
Is the motor started up
Replace PG motor
Replace the mainboard
with the same model
Measure the voltage of this foot to
neutral wire on the mainboard
End
Reinstall the blade
and motor correctly
Insert the control terminal
of PG motor tightly