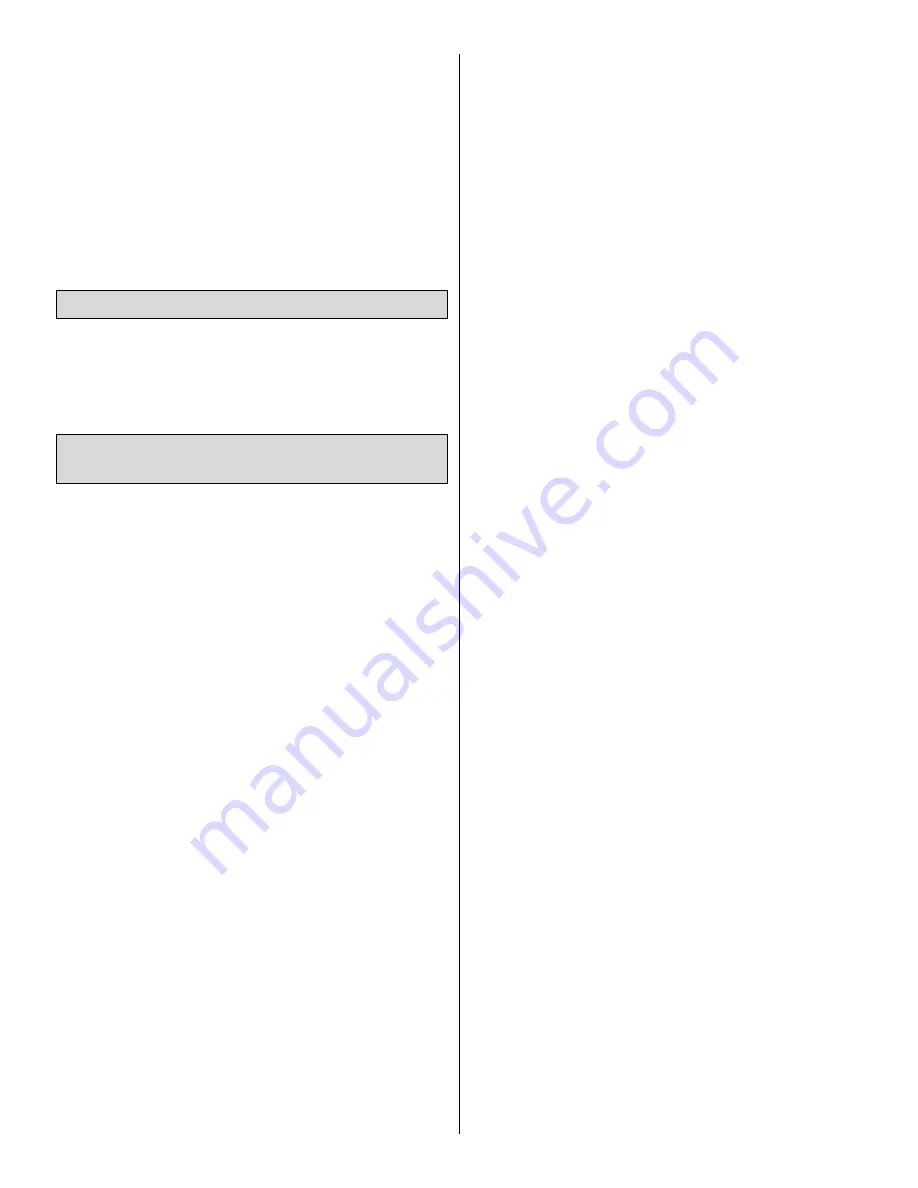
5.2 Engines with battery power ignition systems must have
a switch to turn off the power from the battery pack to
disable the engine from firing. This will also prevent
accidental starting of the engine. This switch shall be readily
available to both pilot and helper. This switch shall be
operated manually and without the use of the Radio System.
5.3 There must also be a means to stop the engine from the
transmitter. The most common method is to close the
carburetor throat completely using throttle trim. However,
other methods are acceptable. This requirement applies to
all glow/gas ignition engines regardless of size.
6.1 All transmitters must be FCC type certified.
6.2 FCC Technician or higher-class license required for 6
meter band operation only.
The following recommendations are included in the Safety
Code not to police such items, but rather to offer basic
suggestions for enhanced safety.
Servos need to be of a rating capable to handle the loads
that the control surfaces impose upon the servos. Standard
servos are not recommended for control surfaces. Servos
should be rated heavy-duty. For flight-critical control
functions a minimum of 45 inch/ounces of torque should be
considered. This should be considered a minimum for
smaller aircraft and higher torque servos are strongly
encouraged for larger aircraft. The use of one servo for each
aileron and one for each elevator half is strongly
recommended. Use of dual servos is also recommended for
larger aircraft.
On-board batteries shall be 1000 mAh up to 20 lbs., 1200
mAh to 30 lbs., 1800 mAh to 40 lbs. and 2000 mAh over 40
lbs. flying weight. The number and size of servos, size and
loads on control surfaces and added features should be
considered as an increase to these minimums. Batteries
should be able to sustain power to the onboard radio
components for a minimum of one hour total flying time
before recharging.
Redundant and fail-safe battery systems are recommended.
The use of anti-glitch devices for long leads are recommended.
There is no maximum engine displacement limit, as it is the
position of this body that an underpowered aircraft presents
a greater danger than an overpowered aircraft. However, the
selection of engine size relative to airframe strength and
power loading mandates good discretionary judgement by
the designer and builder. Current AMA maximums for engine
displacement are 6.0 cu. in. for two-stroke and 9.6 cu. in. for
four-stroke engines. These maximums apply only to AMA
Sanctions concerning competition events (such as 511, 512,
515 and 520) and, as such, the maximums apply. All IMAA
(non competition) events should be sanctioned as Class “C”
events, in which these engine size maximums do not apply.
Generally, it is recommended that no attempt should be
made to fly a radio controlled model aircraft with a gasoline
engine in which the model aircraft weight would exceed
twelve (12) pounds (underpowered) per cubic inch of engine
displacement, or be less than five (5) pounds (overpowered)
per cubic inch of engine displacement. Example: Using a 3
cu. in. engine, a model would likely be underpowered at an
aircraft weight greater than 36 pounds. With the same
engine, an aircraft weighing less than 15 pounds would
likely be overpowered.
Servo arms and wheels should be rated heavy duty. Glass-
filled servo arms and control horns are highly recommended.
Control surfaces linkages are listed in order of preference:
1. Cable system (pull-pull). A tiller bar is highly recommended
along with necessary bracing.
2. Arrow Shaft, fiberglass or aluminum, 1/4" or 5/16" O.D.
bracing every six (6) to ten (10) inches is highly recommended.
3. Tube-in-tube (nyrod). Bracing every few inches is highly
recommended. Inner tube should be totally enclosed in
outer tube.
4. Hardwood dowel, 3/8" O.D. bracing every six (6) to ten
(10) inches is highly recommended.
Hinges should be rated heavy duty and manufactured for
Giant Scale use primarily. Homemade and original design
hinges are acceptable if determined to be adequate for the
intended use.
Clevis (steel, excluding heavy-duty ball links) and
attachment hardware should be heavy duty 4-40 threaded
rod type. 2-56 threaded size rod is acceptable for some
applications (e.g. throttle). Clevis is to have lock nuts and
sleeve or spring keepers.
Propeller tips should be painted or colored in a visible and
contrasting manner so as to increase the visibility of the
propeller tip arc.
Additional IMAA General
Recommendations
Section 6.0: Radio Requirements
23