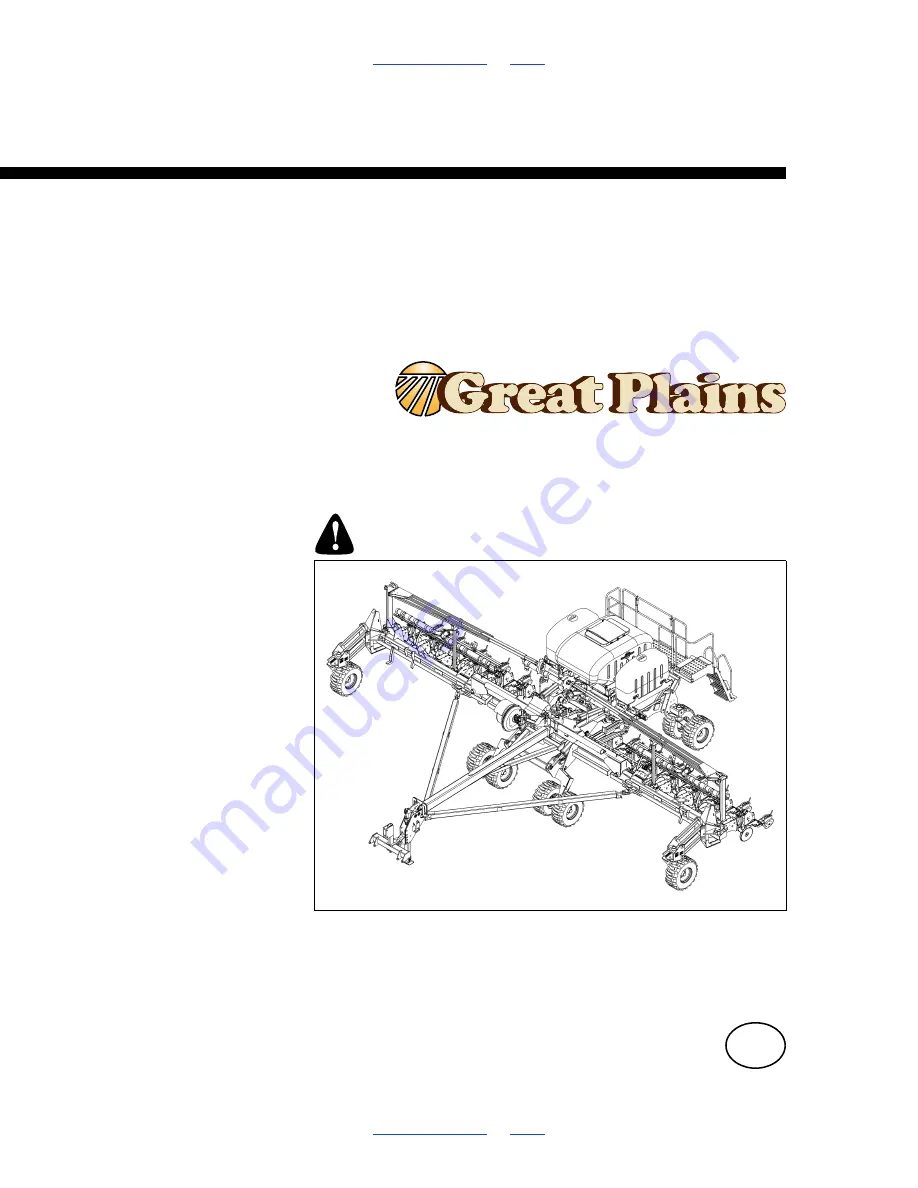
Manufacturing, Inc.
www.greatplainsmfg.com
© Copyright 2019
Printed 2019-03-19
411-198M
EN
ORIGINAL INSTRUCTIONS
Operator Manual
YP4025A-48TR20
40 Foot 3-Section Yield-Pro®
Planter
Read the operator manual entirely. When you see this symbol, the
subsequent instructions and warnings are serious - follow without
exception. Your life and the lives of others depend on it!
Illustrations may show optional equipment not supplied with standard unit or
may depict similar Great Plains implement name models where a topic is
identical.
29817