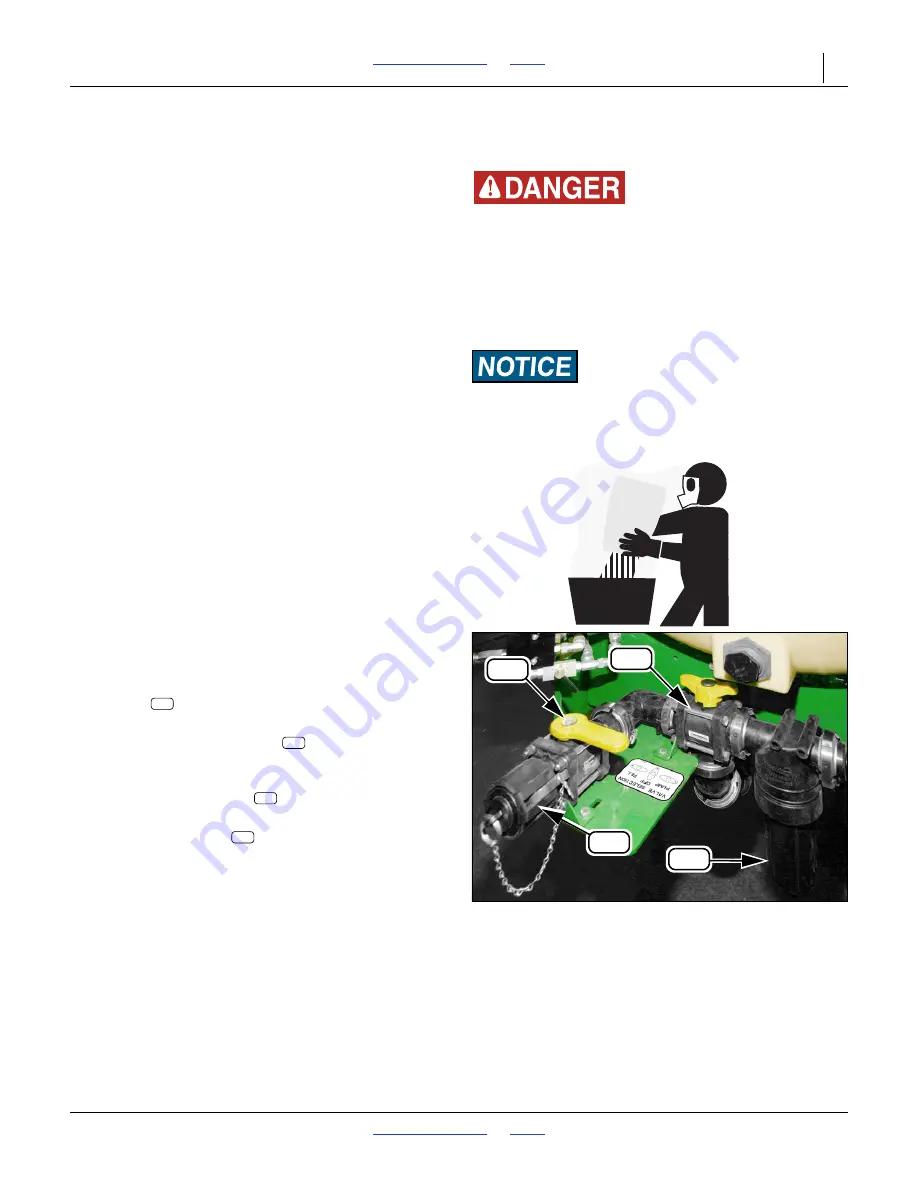
2019-04-12
417-459M
NP2540
Operating Instructions
72
Liquid Operations
Operations for anhydrous nitrogen fertilizer begin on
Liquid: Filling On-Board Tanks
The tanks may be loaded from the quick-fill inlet, or from
the lids (page 73).
If the fertilizer solution has any tendency to settle,
sediment, gel, coagulate, precipitate or stratify, load
material immediately prior to application. The tank
system has no agitators for sustaining suspensions.
Apply fertilizer soon after material loading. Clean out
unused materials promptly. Fertilizer allowed to remain in
the tanks for an extended period can settle, resulting in
excessive or insufficient concentrations during
application. System plugging can also occur.
1. Hitch the applicator to a tractor. Filling an unhitched
applicator is not recommended, as it can increase
parking stand loads above the bearing capacity of
the soil.
2. Inspect the tanks from the lids.
3. Drain excess condensation from the tank, so that
this water does not dilute the material to be loaded.
4. Flush the tank if there is other residue present.
NH
3
: Tank Quick-Fill
5. Position the applicator on level ground, or tanks may
fill unevenly.
6. Connect the nurse-tank hose to the quick-fill
coupler
located at the left end of the left tank.
Lock hose in place with cam-lock levers.
7. Open the discharge valve (
, not shown) of each
tank to be filled. If filling must be performed on
unlevel ground, fill one tank at a time.
8. Set the selector valve
to “FILL” (handle arrow
pointing forward, toward elbow from inlet).
9. Open shut-off valve
at quick-fill coupler.
10. Open any supply valve and fill tanks. Tanks are
marked with fill levels.
11. Close valve at supply, then quick-fill coupler, and
disconnect the nurse tank hose.
12. Set selector valve to OFF, or to PUMP if applying
immediately.
L17
L15
L16
L18
Figure 49
Inlet and Selector Valve
32082
Agricultural Chemical Hazards:
Observe safety precautions specified by material suppliers.
Some chemicals can cause serious burns, lung damage and
death. Avoid contact with skin or eyes. Avoid prolonged
breathing of chemical fumes. Wear respirator and other
protective equipment as required by chemical manufacturer.
Seek medical assistance immediately if accident occurs. Know
what to do in case of an accident.
System Plugging Risk:
Use only pre-mixed liquid fertilizer. Fill tanks at field,
immediately prior to application. Do not use dry mixes. Do not
leave material in tanks for extended periods.
L16
L13
L15
L17