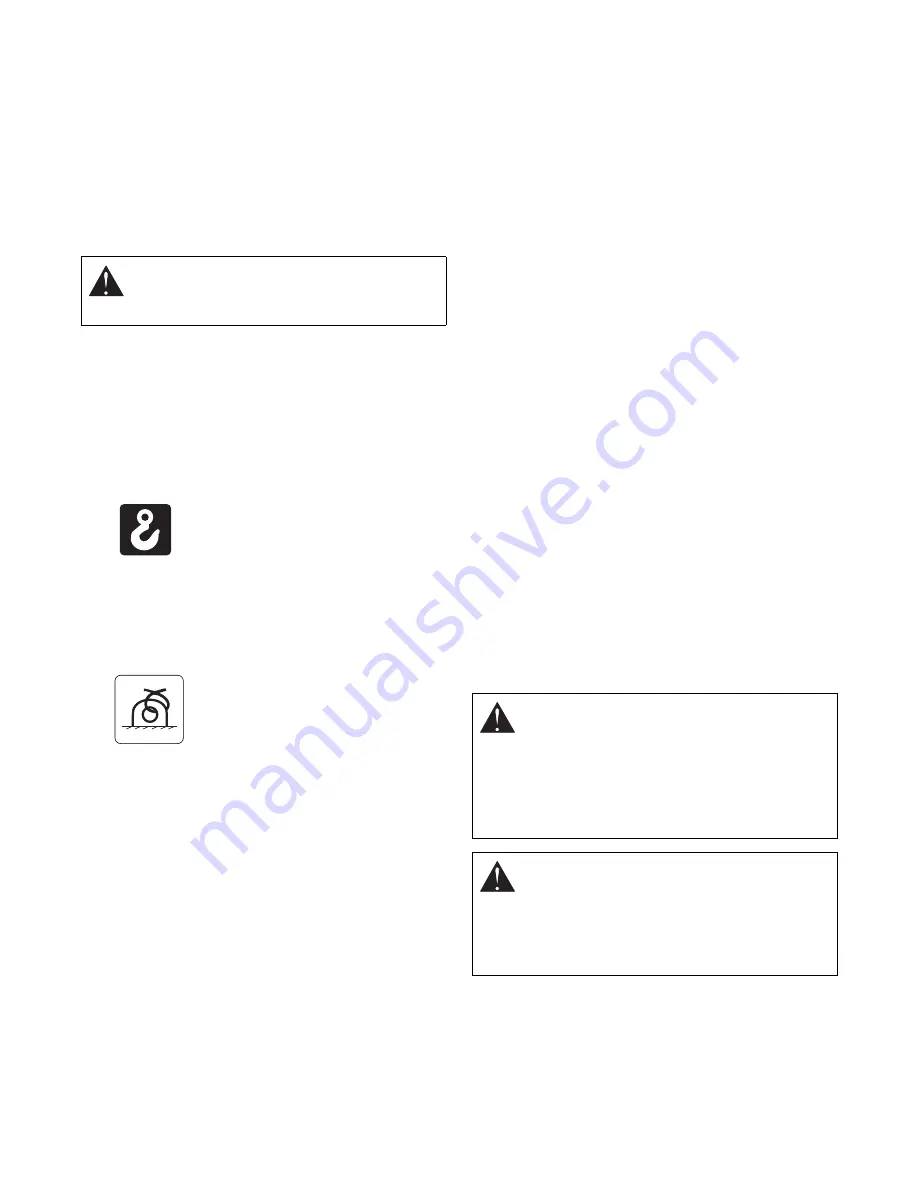
GB - 18
PARKING
1. Move the traction control levers to neutral.
2. Lower lift arms to the ground.
3. Move throttle to slow position.
4. Engage parking brake.
5. Turn the ignition key to OFF to stop the engine.
6. Remove the key from the ignition switch.
7. Avoid parking on slopes, but if you must, use wheel
chocks.
TRANSPORTING THE UNIT
IMPORTANT:
Do not operate or drive unit on
roadways.
IMPORTANT:
Do not tow the unit. Hydraulic damage
may occur.
Lift Lug
Unit may be lifted and moved by crane.
1. Stop the engine.
2. Secure crane hook to lift lug on top
of unit.
3. Lift the entire unit off the ground
and move to new location.
Tie Down Lugs
If transporting unit on a trailer, use the following
procedure:
1. Drive unit onto trailer.
2. Lower the attachment arms.
3. Stop the engine.
4. Secure the unit to the trailer. Use
the tie down lugs on the front and
back of the unit.
IMPORTANT:
DO NOT use tie down lugs to pull, winch
or lift unit.
CONNECTING STANDARD BUCKET
IMPORTANT:
Only use attachments that are approved
by the manufacturer. The operating characteristics and
stability of the unit is affected by any attachment. Using
unapproved attachments may void the warranty.
1. Clean the mounting plate before connecting any
attachment.
2. Check that all controls are in the neutral position.
3. Start engine.
4. Tilt the mounting plate forward.
5. Move the unit so the mounting plate is positioned
under the lip of the bucket’s mating plate.
6. Tilt back the mounting plate and raise the lift arms
at the same time. The bucket will slide into position.
7. Before stopping the engine, the bucket should be
clear of the ground and the mounting plate should
be tilted back.
8. Stop the engine.
9. Engage the attachment lock pins.
DISCONNECTING STANDARD BUCKET
1. Lower the bucket onto a pallet or 4 x 4 wood
blocks.
2. Stop the engine.
3. Disengage the attachment lock pins.
4. Start the engine, tilt the mounting plate forward,
and back the unit away from the bucket.
OPERATION OF STANDARD BUCKET
Do’s and Don’ts
When using the standard bucket, don’t lift more than
300 lbs. (136 kg). A weight kit can be added to
increase maximum lifting weight (see
Accessories).
Lifting more than this amount can make the unit
unstable and cause personal injury. Lift the bucket only
when you are in position to dump the load. When
dumping loads, unit should be on a level surface.
OPTIONAL ATTACHMENTS
For instructions on the proper use of other
attachments, refer to the attachment’s Owner/Operator
Manual.
Use only attachments and accessories approved by
Gravely.
CAUTION:
Always remove the ignition key
when leaving the unit to prevent unauthorized
use.
OK0540
OK0530
WARNING:
Use of attachments other than
those recommended by Gravely could cause
injury to operator and/or damage to unit.
DO NOT use auxiliary hydraulic equipment
that has a pressure rating below 3000 psi.
Serious injury and/or damage to unit may
occur.
WARNING:
To prevent tipping, DO NOT drive
unit without attachment when weight kit is
installed. ALWAYS remove weight kit when
removing attachment. ALWAYS install weight
kit when installing an attachment that requires
weight kit.