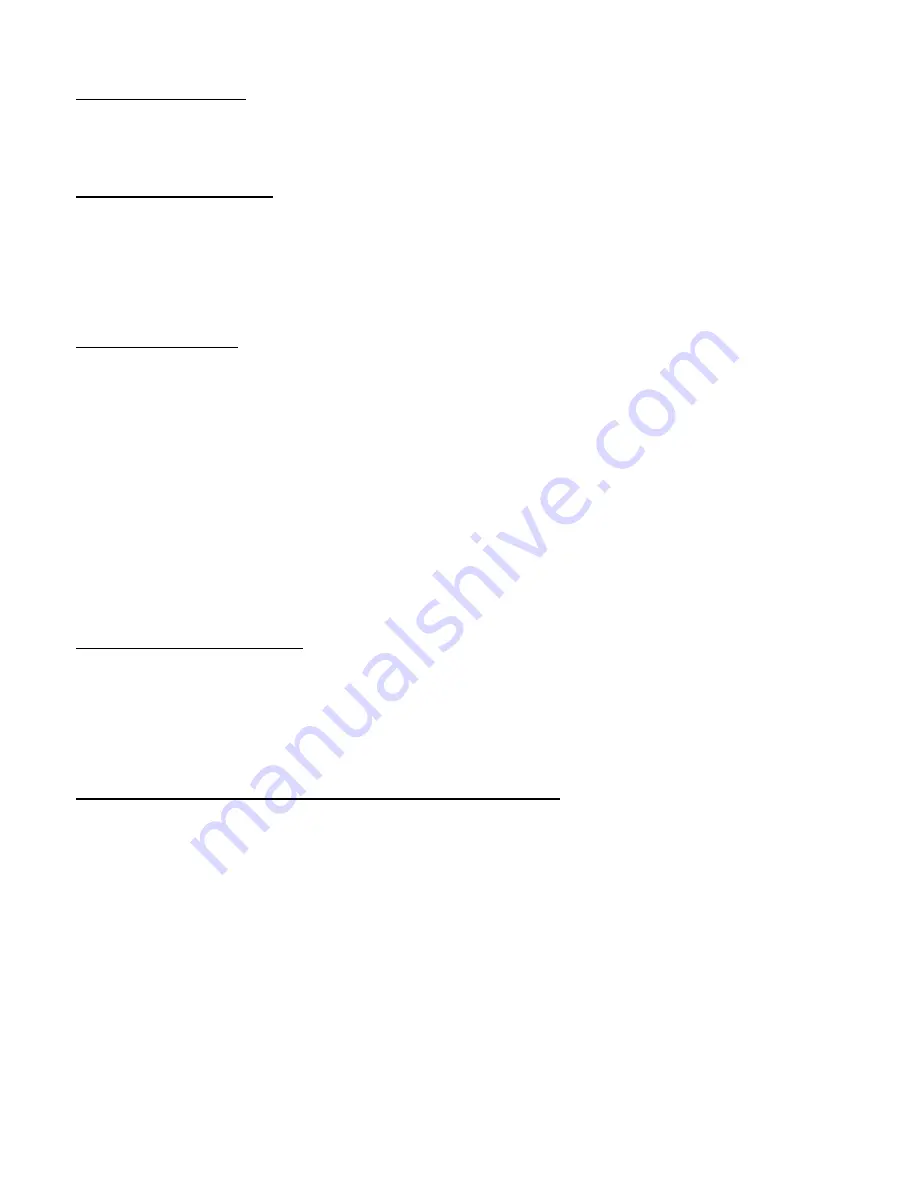
48
SHIFTING LINKAGE
Before assuming that internal transmission problems exist, check all external linkage. Inspect the shifting
linkage beginning with the control lever and work towards the transmission. Check for binding. Look for
broken or missing cotter pins and sheared keys.
CLUTCH ADJUSTMENT
Clutch adjustment is necessary anytime clutch slippage occurs.
Clutch rods when engaged should just completely compress the springs on the clutch actuating lever when
fully engaged.
To adjust, tighten the jam nuts until proper adjustment is obtained.
If external adjustments do not correct problems, internal examination may be necessary.
ENGINE REMOVAL
1.
Remove ground cable from battery.
2.
Drain Transmission oil.
3.
Turn off fuel at fuel tank. Remove fuel line from fuel pump.
4.
Remove the choke cable from carburetor.
5.
Remove the throttle cable from the linkage.
6.
Separate wiring harness at connector.
7.
Remove cable from starter motor.
8.
Remove rear hitch from tractor.
9.
Remove 2 lower bolts securing engine to the chassis casting.
10.
Remove the 2 upper bolts from the engine but leave in place the casting to support the braces.
11.
Remove engine from tractor.
TRANSMISSION REMOVAL
1.
Remove engine from tractor.
2.
Remove battery.
3.
Remove capscrews holding the handles, fuel tank, and battery box assembly to the chassis, and lift
assembly off chassis.
4.
Remove wheels and wheel hubs
FORWARD-REVERSE CLUTCH AND PLANETARY SYSTEM
To gain access to the forward-reverse clutch and planetary system, remove advance housing and rotate
actuating rod with the lever until entire planetary system is released. All components of the forward-reverse
clutch assembly are now ready for inspection.
a.
Examine all parts for excessive wear or play.
b.
Pay particular attention to the orbit gears and the orbit gear pins. If the bores of the gears are scored or
out-of-round, replace gears and pins.
c.
Check internal gear teeth for wear.
d.
If friction surface, or bond, of clutch cup is worn or damaged, replace cup.
e.
Check the friction surfaces of the reverse cone and internal gear for scoring. If surfaces are damaged,
replace parts to prevent rapid wear of a new clutch.