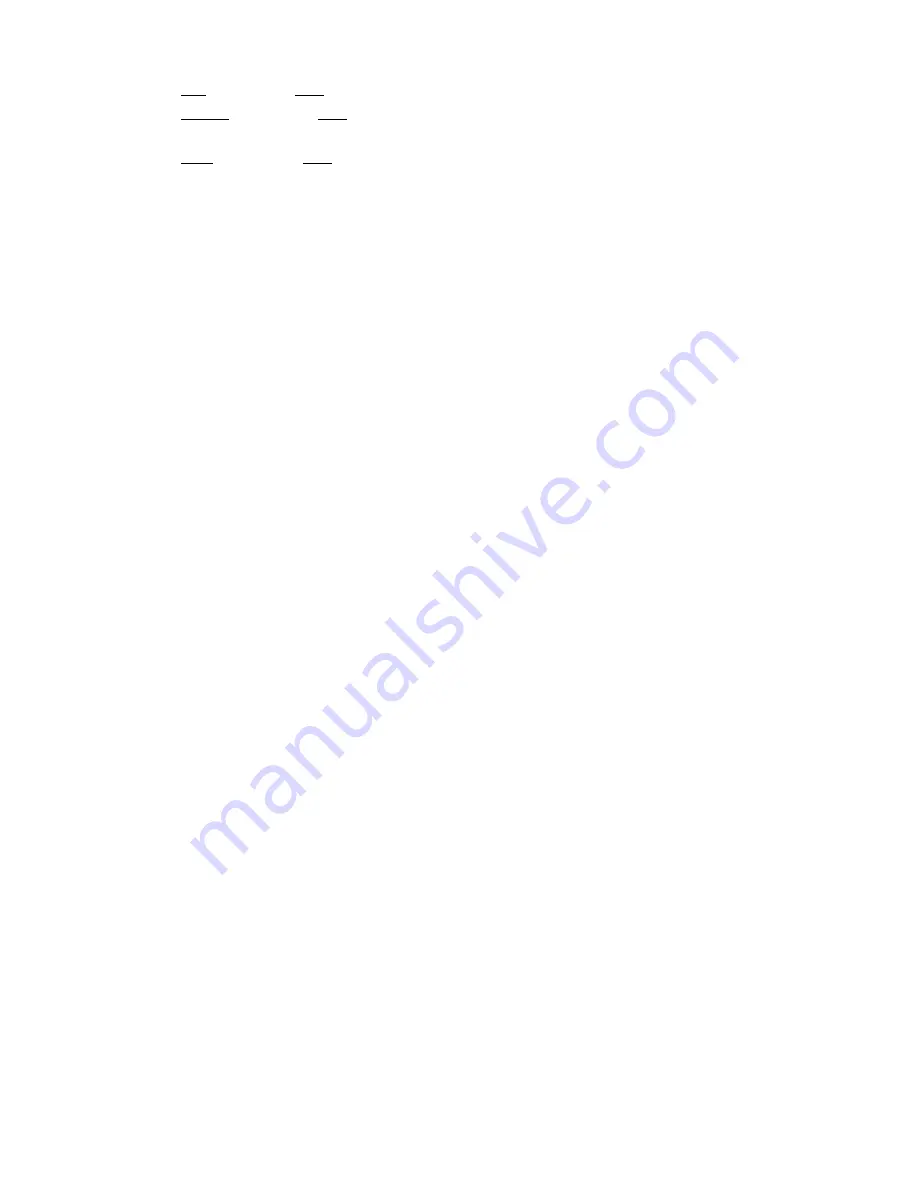
16
(
Note: Step A for timing lights with alligator clips - some lights have sharp prongs on spark lead - on
these simply push prong thru boot until it, contacts metal connector.)
B.
Connect one timing light lead to the wire that has just been wrapped around spark plug terminal.
C.
Connect second timing light lead to hot (ungrounded) side of battery - see timing light instructions for
battery size, wiring, etc.
D.
Connect third timing light lead to ground.
E.
Remove snap button, rotate (by hand) engine until S mark visible -- chalk S line for easy reading.
F.
Start engine, run at 1200 - 1800 RPM, aim timing light into sight hole -- light should flash just as S mark
is centered in sight hole or even with center mark on bearing plate or blower housing.
G.
If timing is off -- remove breaker point cover, loosen gap adjusting screw, shift breaker plate until S mark
is exactly centered. Retighten adjusting screw before replacing breaker point cover.
BREAKERLESS - ALTERNATOR IGNITION
The Kohler Breakerless-Alternator Ignition system uses solid state devices which eliminate the need for
mechanically operated breaker points. With the breakerless ignition, timing is permanently set for the lifetime
of the engine. Except for the spark plug, the entire system is virtually service-free. The system provides an
instantaneous, high energy spark which makes spark gap and even condition of the plug less critical.
The breakerless ignition system includes four major components which are: ignition winding (on
alternator stator), trigger module, ignition coil assembly and special flywheel with trigger projection. The
system also includes the conventional spark plug and lead, plus an ignition switch. The ignition winding is
separate from the other AC windings on the alternator stator -- the other windings are used for battery
charging and other purposes (Discussed in the Electrical System Section).
The trigger module includes three diodes, a resistor, a sensing coil and magnet, plus an electronic switch
called an SCR. The trigger module has two clip-on type terminals. The terminal marked A must be connected
to the alternator while the I terminal is connected to the ignition coil -- improper hook-up will cause damage
to the electronic devices.
The ignition coil assembly includes the capacitor and a pulse transformer arrangement similar to the
conventional high tension coil with primary and secondary windings. The flywheel has a special projection
for triggering the ignition.
AIR GAP: The air gap between trigger assembly and projection on the flywheel is usually set at about
.015" ( ±.005). Although the actual gap setting is not critical to operation at normal speeds, decreasing the gap
to .010" may promote faster starting under certain conditions. If a closer gap is desired, rotate flywheel until
projection is adjacent to the trigger assembly. To adjust, loosen capscrews on trigger bracket and move trigger
closer to projection until .010" gap is measured on feeler gauge. Do not set closer than .010", and make sure
flat surfaces on trigger and projection are parallel to each other. Retighten capscrews after gap is readjusted.
TROUBLE ANALYSIS: In case of ignition trouble, make the following tests in the sequence listed until
the faulty part is located. Use an ohmmeter or flashlight type continuity tester to perform the ignition Coil and
Trigger Module tests.
Spark Plug Test:
Remove plug from head, leave high tension lead connected to plug, ground plug
on engine then crank engine fast enough to produce spark -- if spark does not appear between electrodes, use
new plug and repeat test. If spark is still not evident, proceed with further tests.
Ignition Coil Assembly Tests:
(A)
-- Remove high tension lead from terminal on coil. Insert one tester
lead in coil terminal and the other to the coil mounting bracket. Continuity through the coil should be
indicated.
(B)
-- Connect one tester lead to the coil mounting bracket and the other to the ignition switch wire.
Continuity should not be indicated here. Replace ignition coil assembly if wrong results are obtained from
either of these tests.
Trigger Module Tests:
(A)
-- Connect one tester lead to the AC inlet lead on trigger module and other to
lead on trigger side of ignition switch. This should show continuity in one direction but not in the other -
reverse leads to check this.
(B)
-- Connect one tester lead to the trigger module mounting bracket and the
other to the AC inlet lead to the module. Continuity should be indicated in one direction but not in the
opposite - reverse leads to check this.
(C)
- Connect op sitive lead of tester to outlet (coil side)wire on
ignition switch, connect other lead to the trigger module mounting bracket. Crank engine -- when trigger