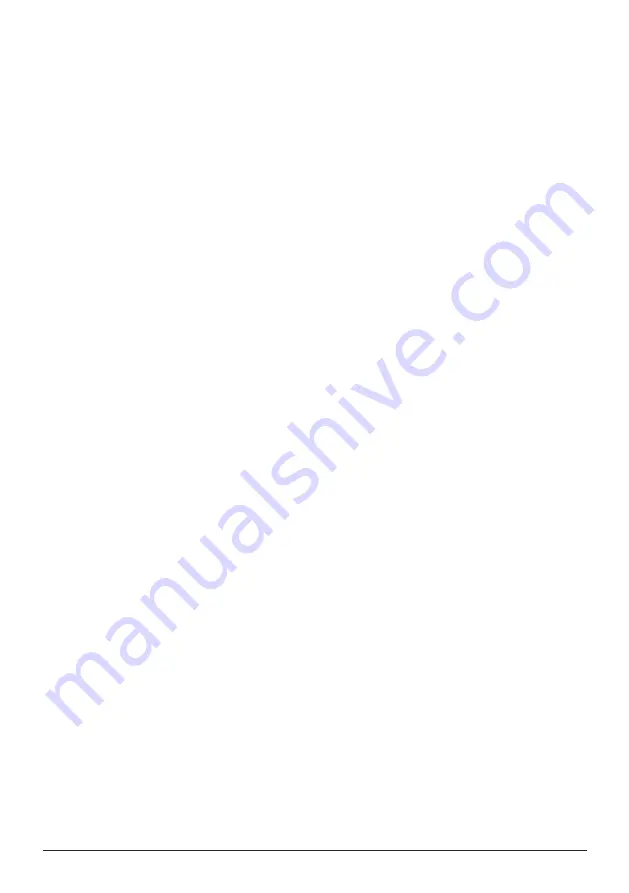
features two servos acting on each aileron instead of only one.
The SMART-BOX can be used to manage a maximum of sixteen transmitter channels. At this point
you can de
fi
ne how the transmitter channels (INPUT) are assigned to the channels (OUTPUT) of the
receiver(s).
If your model is
fi
tted with multiple receivers, the Master receiver is the last receiver to be bound.
However, in subsequent operations only the receiver which was bound last is able to make a telemetry
connection to the transmitter. On the other hand, this also means that only the last bound receiver can
be addressed using the Telemetry menu.
Fail-safe mode (MODE):
this function is used to select the fail-safe mode for the channel you have se-
lected. You can select either a programmed fail-safe position (Fail Safe), hold-mode for the last position
(HOLD) or OFF.
But CAUTION:
if the control signal is absent, analogue servos and many digital servos offer no resis-
tance to the forces acting on the control surfaces, with the result that the model’s control surface posi-
tions are more or less quickly lost.
Please read the corresponding chapter in the RC system instructions on this subject.
F.S.Pos. (Fail-Safe position):
For each OUTPUT CH (receiver servo socket) activate (highlight) the value
fi
eld by brie
fl
y pressing the
INC + DEC simutanously, then use the INC or DEC buttons in the “F.S.POS.” line to set the servo posi-
tion which the servo is to take up in “FAIL-SAFE” mode if interference should occur. The setting can be
entered in increments of 10
μ
s. Default setting: 1500
μ
s (servo centre).
Important note:
The “F.S.POS.” function is also signi
fi
cant if the receiver is switched on, but is (not yet) receiving a valid
signal; this applies to all three modes “OFF”, “HOLD” and “FAILSAFE”: The servo immediately runs to
the Fail-Safe position previously set in the “Position” line. This can be exploited, for example, to prevent
the operation of a retractable undercarriage or similar function if the receiver is switched on accidentally.
However, during normal model operations the corresponding servo behaves in accordance with the set
“MODE” if interference should strike.
Fail-safe response time (DELAY):
this point is used to select the delay time after which the servos run
to their selected position if interference affects the radio signal. This value is applied to all channels.
FAIL SAFE ALL (global fail-safe setting):
This sub-menu can be used to de
fi
ne the Fail-Safe position
of the servos simply by “pressing a button”; and is simple to use: Move to the “FAIL-SAFE ALL” line and
press the INC + DEC buttons simultanously to activate the value
fi
eld; “NO” is highlighted (black back-
ground). Now set the parameter to “SAVE” using the INC or DEC button. Use the transmitter controls to
move all the servos which you have assigned - or intend to assign later - in the “MODE - FAIL-SAFE”
line, to the desired fail-safe positions. In the extreme bottom line “Position” displays the current position
of the transmitter control for the channel you have just set.
After touching the INC + DEC buttons once more, the display reverts from “SAVE” to “NO”. This indica-
tes that the position of all the servos affected by the procedure have now been stored, and have also
been adopted in the “F.S.Pos.” line. At the same time the position for the current OUTPUT CH (servo
socket) is immediately displayed on the screen.
Switch the transmitter off, and check the Fail-Safe positions by observing the servo movements.
Fail-safe position (POSITION):
displays the Fail-Safe position for the channel set under OUTPUT
CH.
“Fail-Safe” in combination with “channel mapping”
It is clearly desirable that mapped servos - i.e. servos which are controlled by a common control channel
(INPUT CH) - should respond in the same way when interference occurs, so the corresponding settings
of the
INPUT CH determine the behaviour of mapped servos.
Manual Module M-G2 33302
10