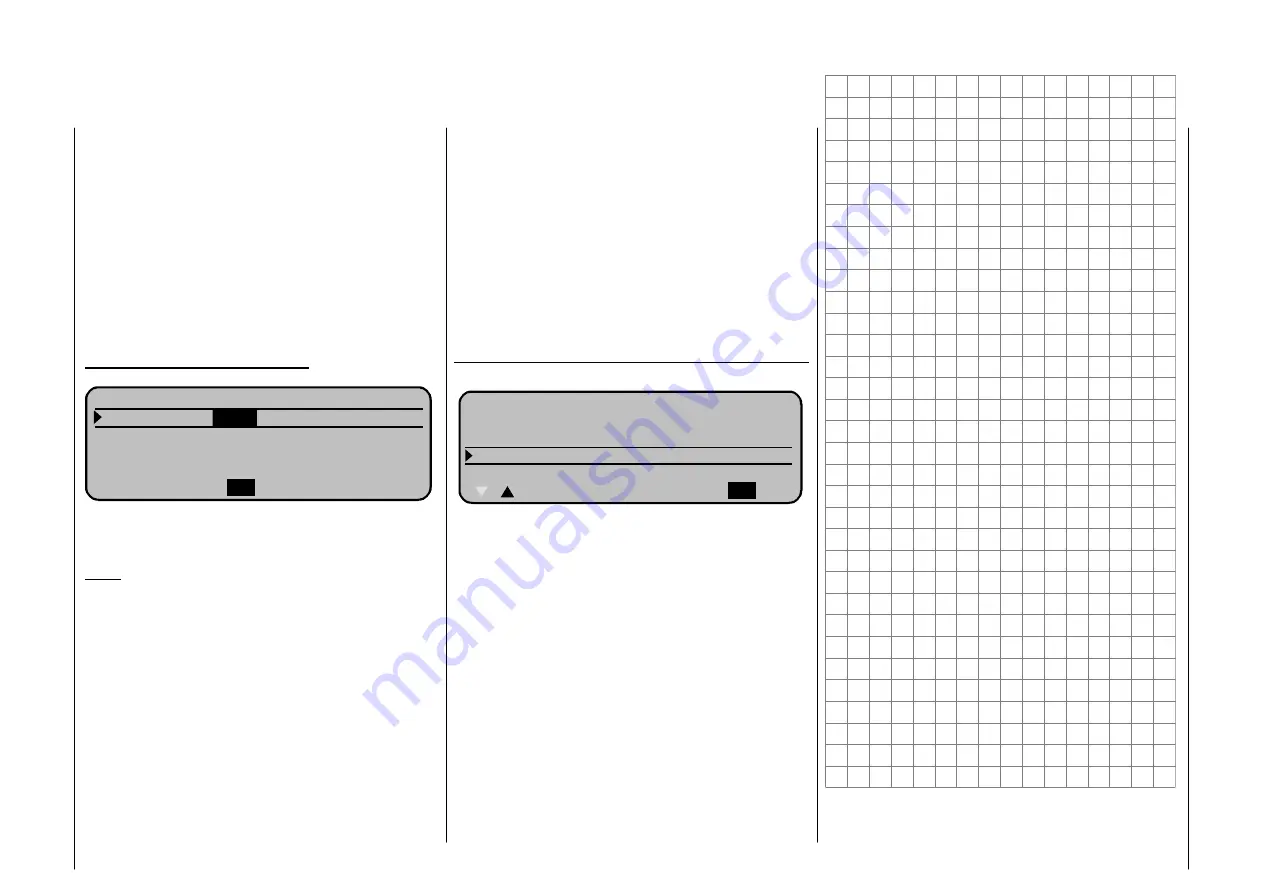
Programming examples
37
movement of servos 1+7 while simultaneously in the
“Landing“ phase output 6 (speed controller) is
The display indicates in the “Start“-phase the
movement of servos 1+6 with the movement of the
CH 1 control stick and in phase “Landung“ the
changing without delay to -100% (=Motor OFF). At
this stage the two aileron servos 2+5 are not
affected by the CH controller in the landing phase?!
As there is no servo connected to output 1+7 we are
no longer interested in the servo display.
To be able to move the two aileron servos with the
CH 1 controller we change to ...
Code 71 »Wing mixer«, page 28
QR
B R E M S E I N S T E L L U N G E N
Butterfly
+3
0%
Diff.-Redukt. 0%
HR-Kurve
=>
directly into the sub-menu “Brake adjust“.
Note:
You are missing the “Multi-Flap-Menu“?
Again change with a push on the rotary knob to the
»
Servo display
«:
In phase “Landing“ the output for the aileron servos
2+5 are now also moving with movement of the Ch 1
controller (throttle stick), but now as landing flaps!
If necessary you have to select an elevator
compensation for the extension of the landing flap in
“El-curve“ mixer. (To be able to select the correct
value during (test) flight we do recommend the
installation of a INC/DEC-switch in Code 49
»
Auxiliary switch
«. Preferably you use a 2 position
momentary switch Part-Nr.
4160.44
.)
The ailerons used as “Landing flaps“ have the
neutral position with the CH 1 control stick in the
foreward position (away from pilot) as the offset is
at +100% in the default setting...
Code 22 »Model type«
M O D E L L T Y P
Leitwerk
normal
Querruder/Wölbklappen 2 QR
Bremse Offset +90% Eingang 7
SEL
This can be changed as necessary. (To be able to
change the offset value make sure you switch into
the landing phase first). A value of about 90% is
most appropriate: As the remaining control throw of
the stick to full foreward no longer influences the
aileron position and you are ensured the ailerons
are neutral with the throttle stick full foreward in the
landing mode even if you have moved the stick
slightly backwards (accidentally).
At the same time the avalable control travel
On a model with only two aileron servos is this menu
not relevant. It is inhibited in the software!
Adjust the control values for the ailerons to your
requirement.
isexpanded to 100%.
Summary of Contents for 4831.660
Page 41: ...Programming examples 43 ...
Page 42: ...Personal notes 44 ...