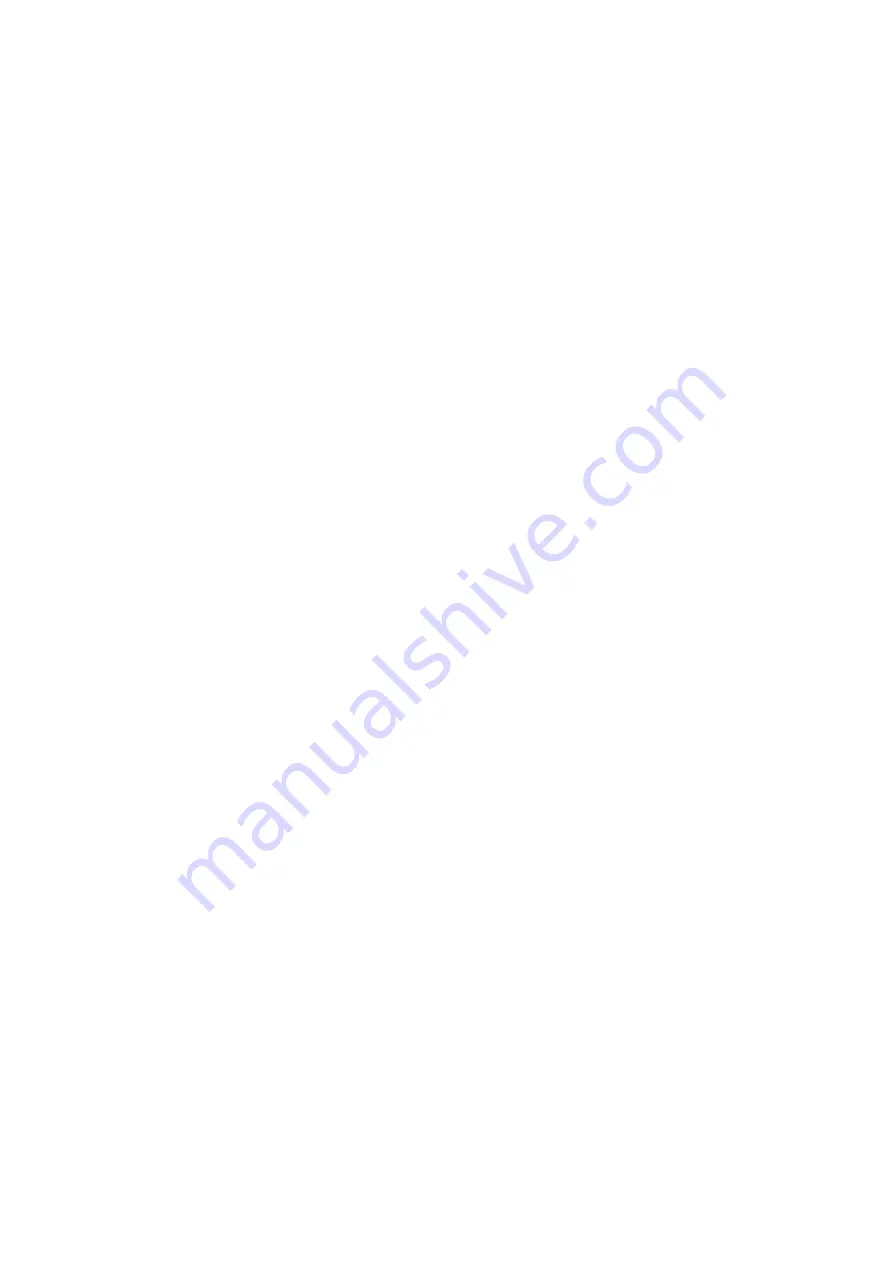
Section 9: Boiler Operation
Page 35
The boiler water temperature is continually monitored during boiler
operation. If it exceeds ‘Hysteresis On’ temperature plus ‘Set Point’
temperature (i.e. boiler temperature > ‘Set Point’ + ‘Hysteresis On’),
OR the ‘Temp Off H2O’ value, the boiler/burner will stop operating.
The boiler water temperature will now have to drop to below the ‘Set
Point’ – ‘Hysteresis On’ temperature before the boiler/burner will
operate again.
There is a pre-set ‘Temp Delta’ value (5°C). This gives the temperature
band above and below the ‘Set Point’ temperature – within which the
boiler output will be modulated. Refer to Figure 9-1.
When the boiler temperature is below the ‘Set Point’ temperature
minus ‘Temp Delta’ value, the modulation of the burner is set to
maximum.
When the boiler temperature is above the ‘Set Point’ temperature plus
‘Temp Delta’ value, the modulation of the burner is set to minimum.
When the boiler temperature is within the modulation band,
the modulation level is varied in direct proportion to the boiler
temperature, i.e. boiler output varies linearly from maximum at the
bottom of the modulation band (boiler temperature = ‘Set Point’ –
‘Temp Delta’) to minimum at the top of the modulation band (boiler
temperature = ‘Set Point’ + ‘Temp Delta’). Refer to Figure 9-1.
Pellets are delivered to the burner by switching the pellet feed auger
on and off. The auger ‘On’ period is defined by the pre-set ‘Time
Load’ parameter (1.7s).
The burner is modulated by varying the ‘pause’ time between the pre-
set parameters ‘Pause Max Power’ [7] at maximum output and ‘Pause
Min Power’ [6] at minimum output. Refer to Figure 9-2.
The fan speed is automatically controlled to maintain the required air
supply for the output of the boiler as the burner modulates, i.e. if the
output decreases the air supply (and fan speed) will be automatically
reduced, if the output increases the air supply (and fan speed) will be
automatically increased.
This control of the air supply is achieved using the Lambda sensor,
located at the top of the primary heat exchanger. This measures
the oxygen level in the combustion gases and, via the boiler control
system, automatically adjusts the fan speed to achieve the required
level of oxygen for the output level of the burner at that time. Thus, as
the output changes so will the fan speed and air supply rate.
As this system is monitoring the oxygen level and adjusting the
air supply rate accordingly it will automatically compensate for the
gradual increase of ash blockage in the boiler over time, ensuring
that the combustion remains at the optimum throughout the period
between boiler services.
9.3 automatic Cleaning
Adjustable boiler control parameter numbers are shown in square
brackets. Refer to Parameter Menu in Section 9.7.
The control system is programmed to carry out a self-cleaning
function on the burner brazier, heat exchanger and secondary
(condensing) heat exchanger at pre-set intervals.
This self-cleaning operation is automatically performed:
•
on power-up, i.e. when the power to the boiler is connected (this
includes the cleaning of the condensing heat exchanger)
•
after the pellet feed auger running time exceeds the pre-set
‘Clean Boiler’ parameter (480 mins).
The control system will inform the user when a service is required by
displaying a ‘Service’ message on the boiler control panel LCD when
the auger run time exceeds the pre-set ‘Hours service’ period [14].
Once the service is completed, the service engineer can reset the
auger run time hours to zero so that the control will indicate when the
next service is required (after the ‘Hours Service’ value is exceeded).
Refer to Section 12 – Servicing.
If a fault occurs with the operation of the boiler, the control panel LCD
will display a fault code to assist in the diagnosis and rectification.
Refer to Section 13 – Fault Finding.