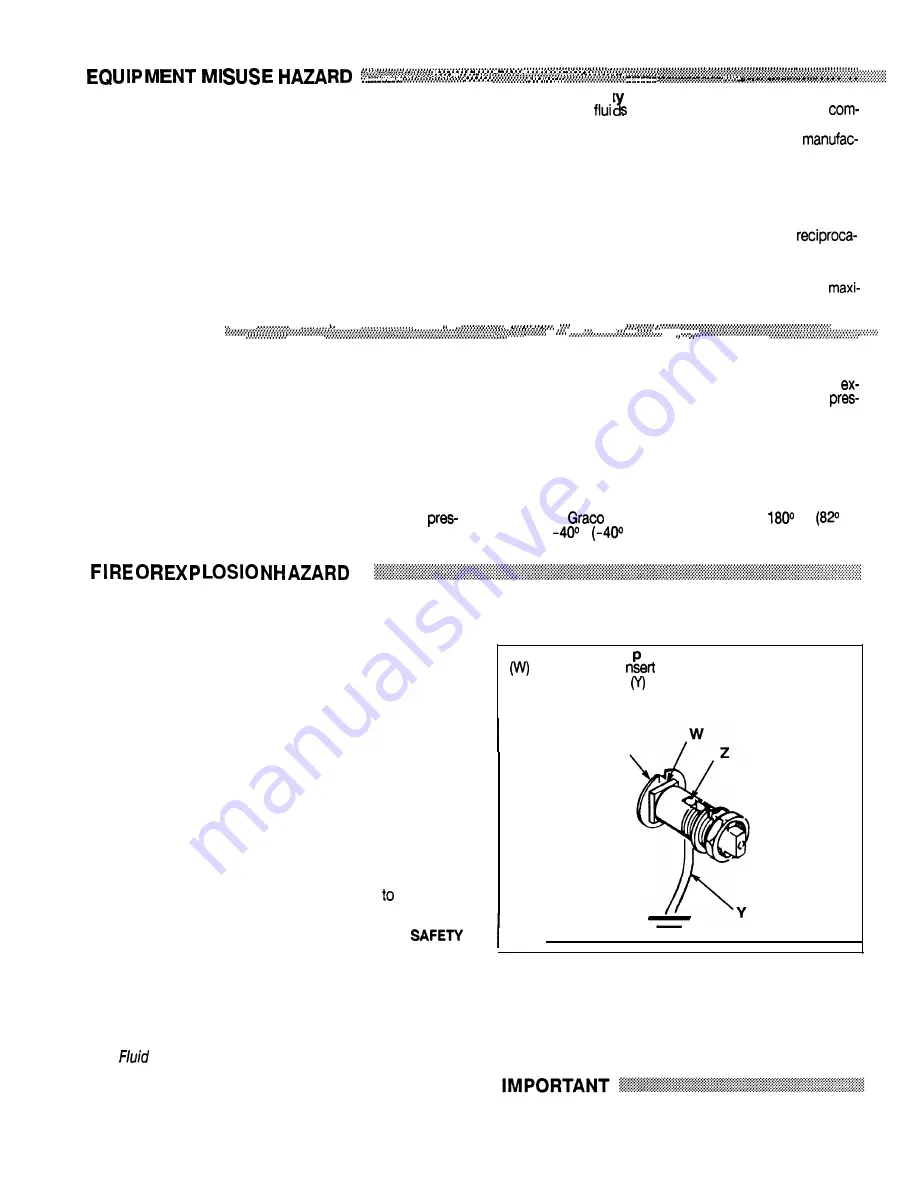
General Safety
Fluid Compatibilit
Any misuse of the dispensing equipment or accessories, such
BE SURE that all
and solvents used are chemically
as overpressurizing, modifying parts, using incompatible
patible with the
wetted parts
shown in the
TECHNICAL DATA
chemicals and fluids, or using worn or damaged parts, can
shown on page 12. Always read the fluid and solvent
cause them to rupture and result in injection or other serious
turer’s literature before using them in your system.
bodily injury, fire, explosion or property damage.
NEVER alter or modify any part of this equipment; doing so
could cause it to malfunction.
CHECK all spray equipment regularly and repair or replace
worn or damaged parts immediately.
System Pressure
The maximum hydraulic input pressure for this reciprocator is
1000 psi (70 bar). The maximum fluid outlet pressure is 3000 psi
(210 bar). Be sure that any components added to the
tor power supply side are rated to withstand this pressure.
ALWAYS read and follow the fluid and solvent manufacturer’s
recommendations regarding the use of protective eyewear,
Consult your separate pump instruction manual for the
clothing and equipment, including respirators.
mum working pressure of the complete pump.
HOSE SAFETY . . . . . . . . . . . . . . . . . . . . . . . . . . . . . . . . . . . . . . . . . . . . . . . . . . . . . . . . . . .
.. . . . . . . . . . . . . . . . . . . . . . . . . . . . . . . . . . . . . . . . . . . . . . . . . . . . . . .
.
. . . . . . . . . . . . . . . . . . . . . . . . . . . . . . . . . . . . .
. . . . . . . . . . , .
. . . . . . . . .
. . . . . . . . . . . . . . . . . . . . . . .
. . . . . . . . . . . . . . . . . . . . .
. . . . . . . . . . .
. . . . . . . . . . . . . . . . . . . . . . . . . . . . . . . . . . .
. . . . . . . . . . . . . . . . . . . . . . . . . . . . . . . , . . . , . . . . . . . , . . . . . . . . .../..../ , . . . . . . . . , . . . . . . . . . . . . . . . . . . . . , . . . . . . , , . . . . . . . . . . . . . . . , , . . . . . . . . . . . . . . . . . .
, . . . . . . . . , . . , . . . , . . . .
, . . . . . . . , . . . . . . .
. . . . . . . . . .
. . . . . . . . . . . . . . . . . . . . .
. . . . . .
. . . . . . . . .
. . . .
. . . . . . . . . . . . . . . .
.......
. . . . . . . . . . . . . . . . . . .
. . . . . . . . . . . . . . . . . . . . . . . . . . . .
. . . . . . . . . . . . . . .
. . . . . . . . . . . . . . . . . . . . . . . .
. . . . . . . . .
. . . . . . . . . . . . . . . . . . . . . . . . . . .
. . . . . . , . . . . . . . . . . . . . . . . . . . . . . . . . . . . . . . . . . . . . . . . . . , . . . . . . . . . .
, . .
. . . . . . . . . . . . . . . . . . . . . . . . . . . . . . , .
High pressure fluid in the hydraulic hoses and pump fluid outlet
NEVER use a damaged hose. Before each use, check entire
hoses can be very dangerous. If a hose develops a leak, split or
hose for cuts, leaks, abrasion, bulging cover, or damage or
rupture due to any kind of wear, damage or misuse, the high
movement of the hose couplings. If any of these conditions
pressure spray emitted from it can cause a fluid injection injury
ist, replace the hose immediately. DO NOT recouple high
or other serious bodily injury or property damage.
sure hose. Never use
tape
or any device to try to mend the hoses;
ALL FLUID SPRAY HOSES MUST HAVE SPRING GUARDS
it cannot contain the high pressure fluid.
ON BOTH ENDS!
The spring guards help protect the hose from
kinks or bends at or close to the coupling which can result in
hose rupture.
HANDLE AND ROUTE HOSES CAREFULLY.
Do not pull on
hoses to move equipment. Do not use fluids or solvents which
TIGHTEN all fluid connections securely before each use. High
are not compatible with the inner tube and cover of the hose. DO
pressure fluid can dislodge a loose coupling or allow high
NOT expose
hose to temperatures above
F
C)
sure spray to be emitted from the coupling.
or below
F
C).
. .. . .. .. . .. . .. . .. .. . .. .. . . . . . . . . . . . . . . . . . . . . . . . . . . . . . . . . . . . . . . .
.
Static electricity is created by the high velocity flow of fluid
through the reciprocator, pump and hose. If the pump is not
properly grounded, sparking may occur, and the system may
become hazardous. Sparks from any source can ignite fumes
from solvents and the fluid being dispensed, dust particles and
other flammable substances, and can cause a fire or explosion
and serious bodily injury and property damage. Do not smoke,
and do not plug in or unplug any power supply cords in the spray
area when there is any chance of igniting vapors still in the air.
If you experience any static sparking or even a slight shock while
using this equipment, STOP SPRAYING IMMEDIATELY Do not
use the system again until the problem has been identified and
corrected.
Grounding
To reduce the risk of static sparking, ground the pump. CHECK
your local electrical code for detailed grounding instructions for
your area and type of equipment.
1.
2 .
3 .
4 .
5 .
6 .
7 .
Pump:
use ground wire and clamp as shown
the right.
Hydraulic Hoses and Fluid
Outlet
Hoses:
use only electri-
cally conductive hoses. Refer also to
HOSE
above.
Fig 1
Hydraulic Power Supply and Air Compressor:
follow manu-
facturer’s recommendations.
Spray gun:
obtain grounding through connection to a prop-
erly grounded fluid hose and pump.
supply container;
according to local code.
Flushing Safety
Reduce the risk of fluid injection injury, static sparking, or
splashing by following the specific flushing procedure given on
page 5. Be sure to relieve pressure and then remove the spray
tip before flushing. Hold a metal pan of the gun firmly to the side
of a grounded metal pail and use the lowest possible fluid pres-
sure during flushing.
Object being sprayed:
according to local code.
Any pails used when flushing:
Use only metal, grounded
United States Government safety standards have been adopted
pails when flushing. Make firm metal-to-metal contact be-
under the Occupational Safety and Health Act. These stan-
tween the a metal pan of the spray gun and the pail. Use the
dards- -particularly the General Standards, Part 191 O--should
lowest possible pressure.
be consulted.
8.
To maintain grounding continuity when flushing or reliev-
ing pressure,
always hold a metal part of the gun firmly to
the side of a
metal pail,
and then open the spray gun.
To ground the pum ,
loosen the grounding lug locknut
and washer (X).
one end of a 12 ga (1.5 mm 2)
minimum ground wire
into the slot in lug (Z) and tighten
the locknut securely. Connect the other end of the wire to
a true earth ground. Refer to page 11 to order a ground wire
and clamp.
X
307-623
3
Summary of Contents for Viscount I 3000
Page 1: ...Parts...