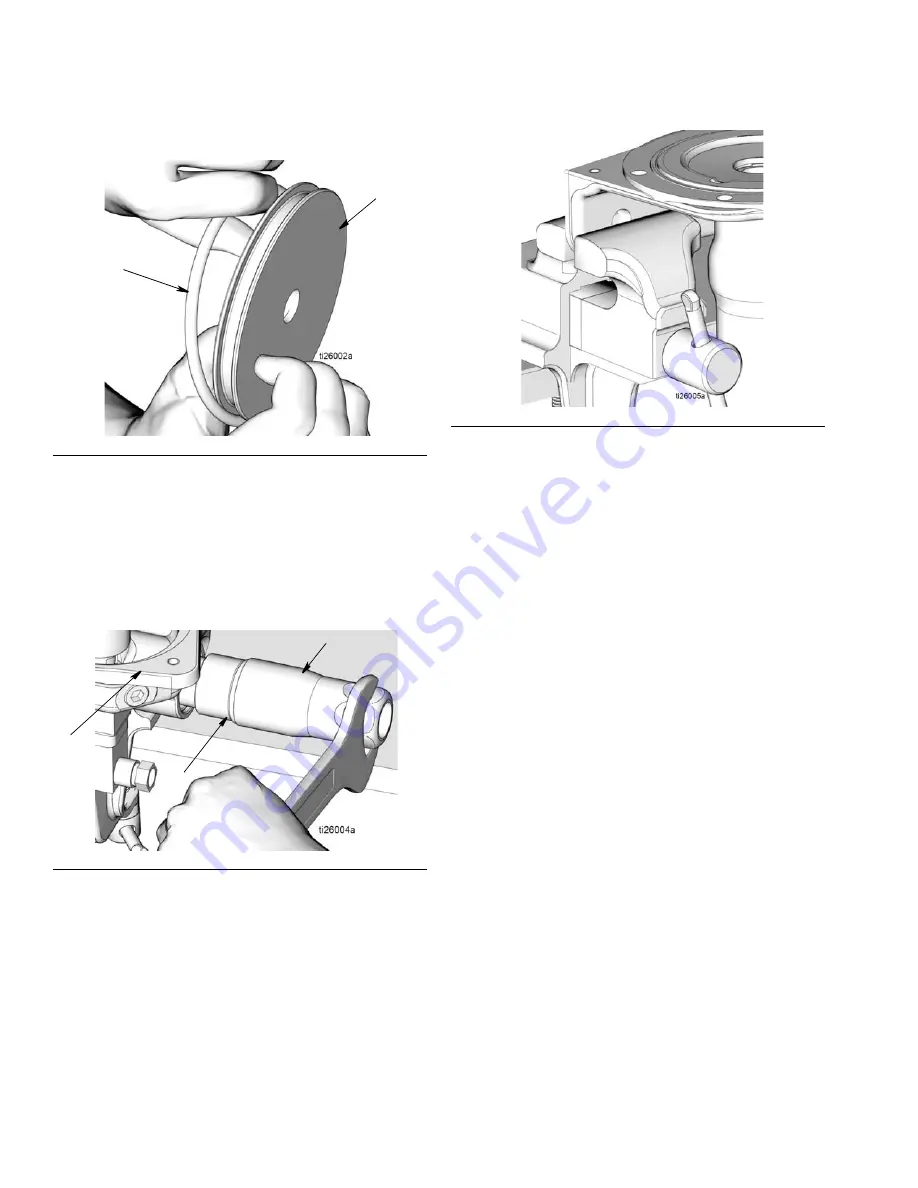
Repair
16
3A3169E
d.
Remove o-ring (7) from piston (6) (F
. 24).
e.
Discard o-rings (7, 41) and nut (5) according to
all regulations for proper disposal
17. Remove the outlet check valve (15) from the pump
base (1) (F
. 25). Remove o-ring (4) from outlet
check valve. Dispose of o-ring according to all regu-
lations for proper disposal.
18. Reposition the pump base (1) in the vise as shown
19. Throat Seal Kit
The Throat Seal Kit includes the following parts
(F
. 27):
•
Retaining Ring (9)
•
Tapered Spacer (10)
•
Seal (11)
•
Spacer (12)
•
Retaining Ring (51)
•
Spacer (12)
•
Seal (11)
•
Spacer (12)
F
IG
. 24
F
IG
. 25
6
7
4
15
1
F
IG
. 26