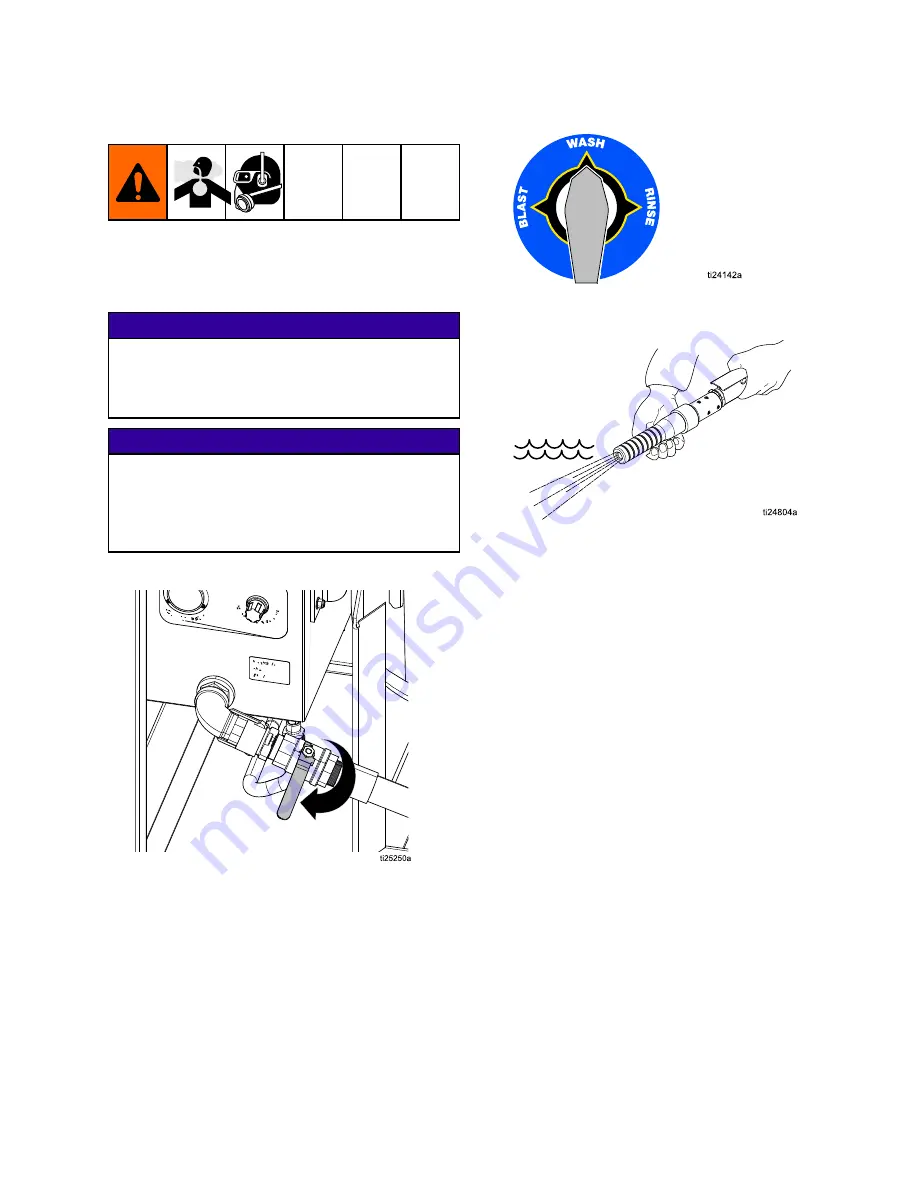
Using
Using
Using the
the
the Wash
Wash
Wash Feature
Feature
Feature
The wash feature causes air-driven water (without
abrasive) to blast and rinse areas that have already
been blasted with abrasive. It is also a convenient
feature for flushing abrasive from the blast hose.
NOTICE
NOTICE
NOTICE
There will always be some residual abrasive in
the blast hose. Never use the wash feature on
any surface other than where you have blasted, or
intend to blast. It will affect/dull the surface.
NOTICE
NOTICE
NOTICE
Do not use the wash feature on wood that has
been blasted. It could damage the wood and cause
the grain to rise. Wait for the wood to dry and then
use a broom, brush, or vacuum to remove any
residual abrasive.
1.
Close the abrasive ball valve.
2.
Turn the selector valve to WASH.
3.
Blast 1 – 2 minutes until the abrasive is cleared
from the hose.
4.
The equipment is now ready to wash any
previously blasted surfaces.
334143C
17
Summary of Contents for EcoQuip 300
Page 5: ...Notes Notes Notes Notes 334143C 5...
Page 34: ...Parts Parts Parts Parts EQ300 EQ300 EQ300 and and and EQ600 EQ600 EQ600 34 334143C...
Page 36: ...Parts Enclosure Enclosure Enclosure 12 Torque fitting to 35 40 ft lb 47 54 N m 36 334143C...