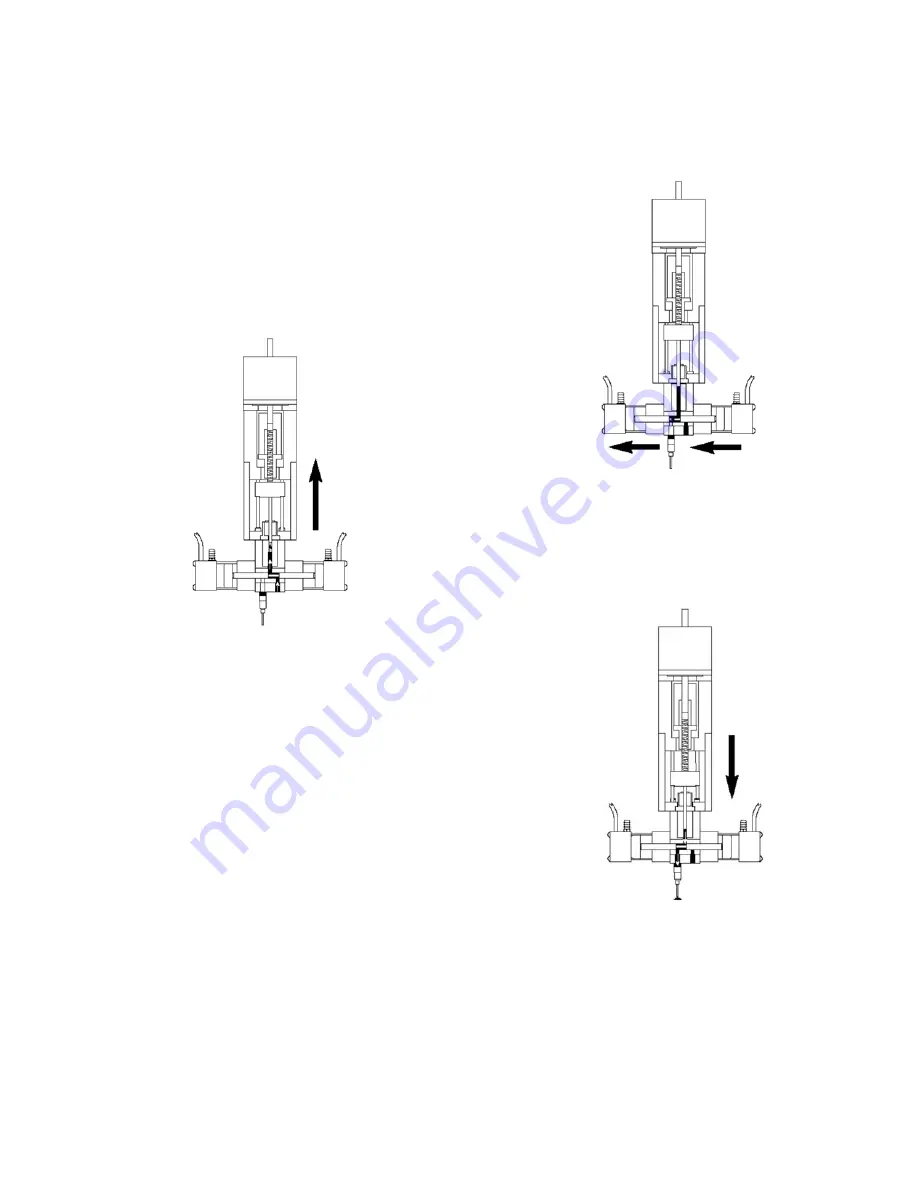
Operation
3A0231E
15
Operation
The operation of the 1052 metering valve is controlled
by an external source. If a 4104A Control Box was pur-
chased, see the 4104A Control Box manual for opera-
tion instructions.
Sequence of Operation
Step 1: Reload
•
Spool shifts to the right
•
Material feed inlet is opened
•
Material is transferred into the metering chambers
by a pressurized feed system
•
Outlet port is blocked
•
Metering rod is retracted to a precise position deter-
mining the volume of each material
Step 2: Shift
•
The balanced spool shifts to the dispense position
•
Material path to the needle is opened
•
Material feed inlet port is blocked
•
Metering rod remains in the retracted position
Step 3: Dispense
•
Metering rod extends
•
Material is dispensed from the metering chamber
into the needle
Upon completion of the dispense stroke, the metering
rod and spool shifts back to the reload position.