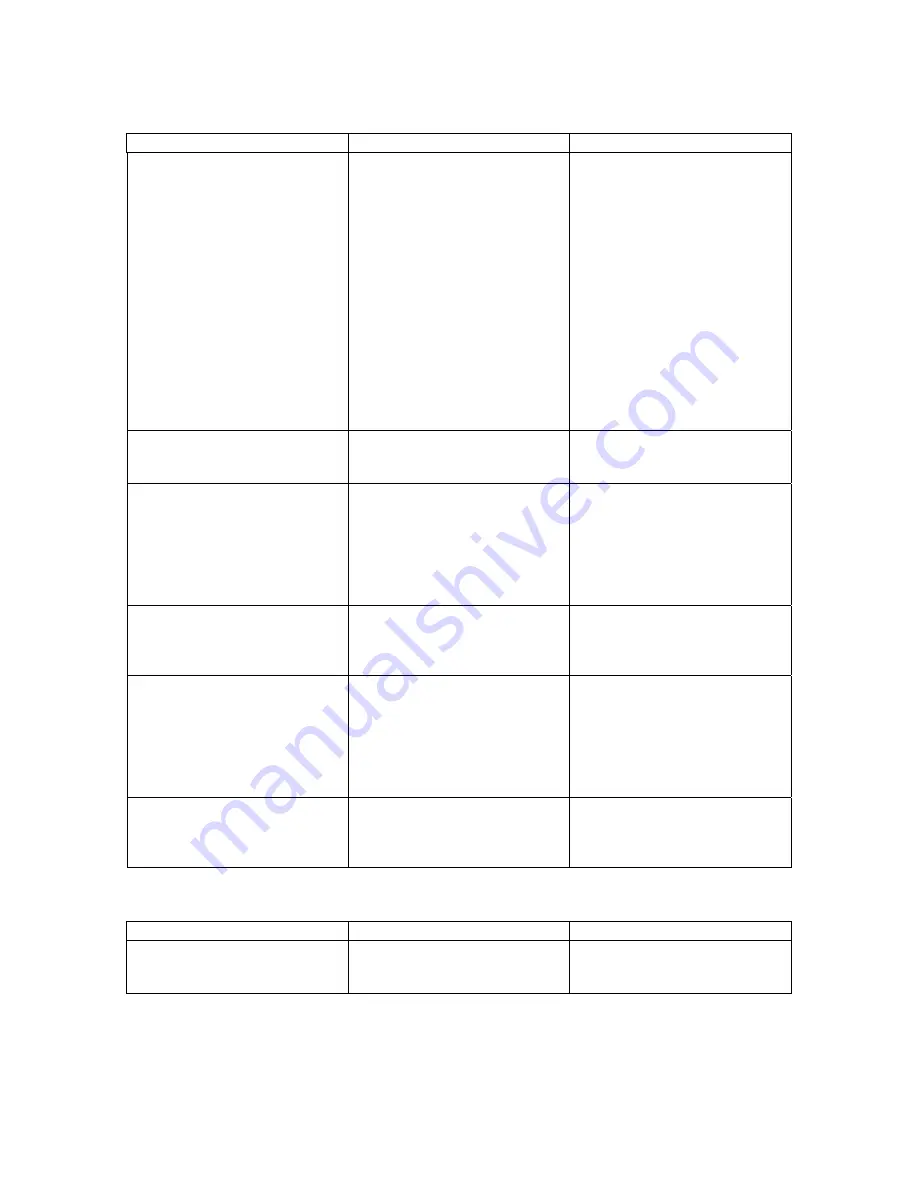
39
Pumping (after satisfactory startup) — Continued
Problem Cause
Solution
Material continues to flow after
pumps stop dispense stroke,
or air bubble apparent at some
part of the dispense stroke
each time.
Air in hose. Hose not primed
correctly.
Air in material — entrapped
during reservoir refill.
Air in material— being drawn
into pump from behind check
valve.
Air in material— being drawn
into pump through inlet hoses
or coupler.
Incline hose from check valve
to outlet of hose. Avoid sags in
hose. Cycle machine until all
trapped air is discharged.
Reload reservoir with
minimum air entrapment. (Ask
for technical advice.)
Remove check valve and
fitting in front of pump.
Reinstall with PTFE tape.
Tighten or seal as necessary.
Severe leaks at pump shaft.
Pump shaft seals worn.
Remove pump packing
assembly and replace shaft
seal set.
Pumps remain in extended
position and will not return.
Roller trip switch faulty.
Pump is out of calibration.
If roller trip switch has air
pressure applied but does not
function when checked,
replace.
Recalibrate pump.
Pumps remain at rest in
retracted position and do not
move when the machine is
signaled to start.
Material cured on piston rod.
Pump is out of calibration.
Clean piston rod, apply
Mesamoll.
Recalibrate pump.
Pumps remain in extended
position and will not return.
Roller trip switch faulty.
Pump is out of calibration.
If roller trip switch has air
pressure applied but does not
function when checked,
replace.
Recalibrate pump.
Pumps remain at rest in
retracted position and do not
move when the machine is
signaled to start.
Material cured on piston rod.
Pump is out of calibration.
Clean piston rod, apply
Mesamoll.
Recalibrate pump.
Motionless Mixer (after satisfactory startup)
Problem Cause
Solution
Material leaks past inlet valves
of dispense valve, mixing
block, or dispense block.
Inlet valve O-ring or seals
damaged or worn.
Replace O-rings or seals.