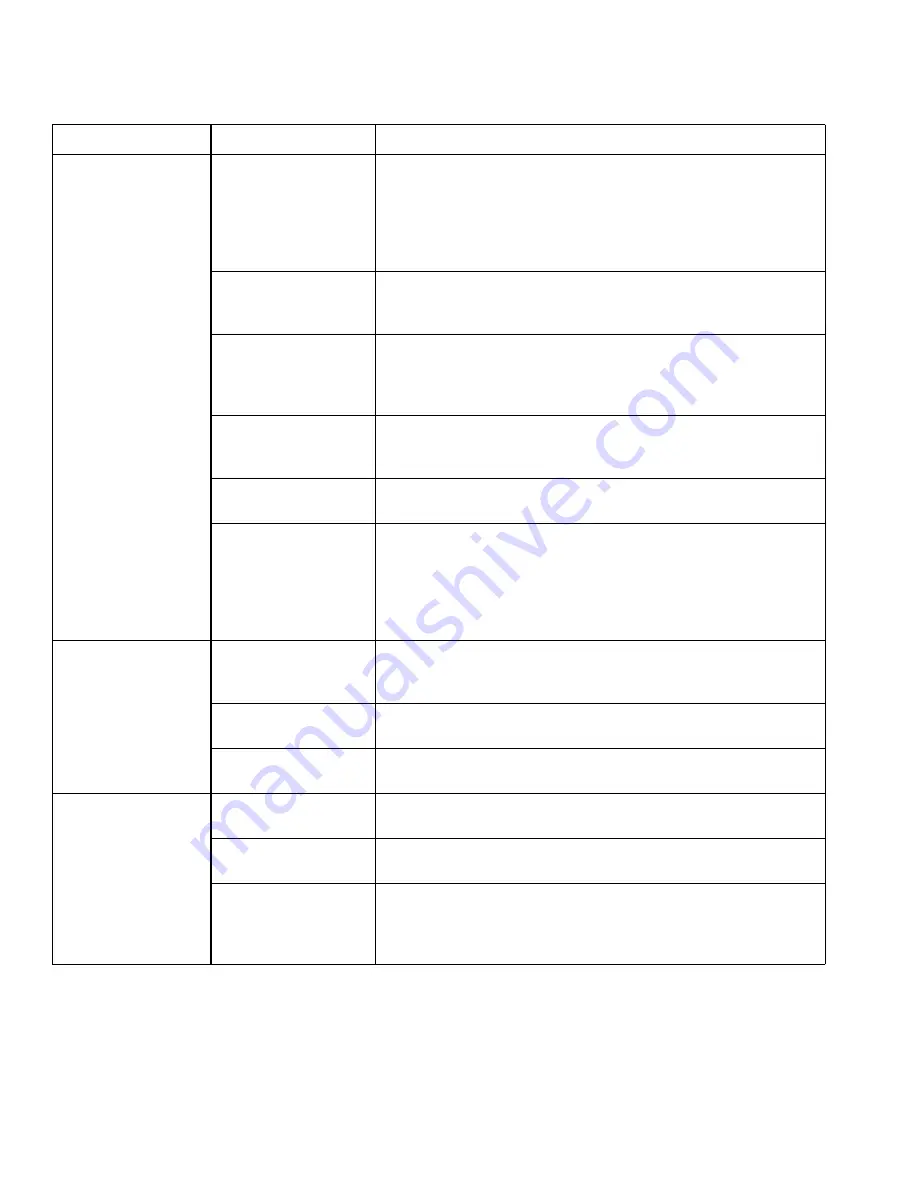
Troubleshooting
34
3A7467D
The blast spray
pattern is sputtering or
irregular.
The air supply is
inadequate.
Make sure the air compressor is capable of supplying the
minimum air flow requirement for your system. See
, page 64. Make sure the air inlet pressure gauge
reads 100-175 psi (6.8-12 bar, 0.68-1.2 MPa). If the gauge does
not read 100-175 psi check the air compressor for proper setup.
Make sure the air inlet filters are clean and replace if necessary.
The blast hose was not
properly cleaned out
after previous use.
See
The abrasive metering
valve setting is too high
for the blast pressure
and/or abrasive type.
See
Set the Abrasive Metering Value
The pot does not have
a sufficient amount of
abrasive.
Refill the pot with abrasive. See
There is an obstruction
in the nozzle.
Remove the nozzle and inspect for blockage, buildup, or damage.
Replace the nozzle if necessary.
There is an obstruction
inside the pot or inside
the abrasive hose
between the pot and
the enclosure.
12. With the abrasive hose disconnected, inspect the interior of the
pinch hose for obstructions or debris and replace if necessary. See
, page 37. Remove the tri-clamp from the
bottom of pot. Inspect the bottom of the pot and abrasive hose for
obstructions or debris.
Too much dust occurs
during blasting.
There is not enough
water in abrasive
mixture.
See
The blast pressure is
too high.
Decrease the blast pressure and re-evaluate the dust levels.
The abrasive is too fine
for the application.
Try a coarser or harder abrasive if possible.
Too much water is
coming from the
nozzle in BLAST
mode.
The water dose valve
(S) is open too far.
Close the water dose valve (S).
The abrasive material
is too coarse.
If possible, use at least 20 mesh abrasive material. Otherwise,
decrease the CPM setpoint until the pattern improves.
The abrasive metering
valve setting is too high
for blast pressure
and/or abrasive type.
See
Set the Abrasive Metering Value
Problem
Cause
Solution
Summary of Contents for 262960
Page 10: ...Component Identification 10 3A7467D Component Identification WL D WLL D 3 1 4 5 6 7 8 9 0 ...
Page 44: ...Parts 44 3A7467D EQ200T Parts WL F 1 Apply thread sealant to all non swivel pipe threads ...
Page 46: ...Parts 46 3A7467D EQ400T Parts 1 Apply thread sealant to all non swivel pipe threads ...