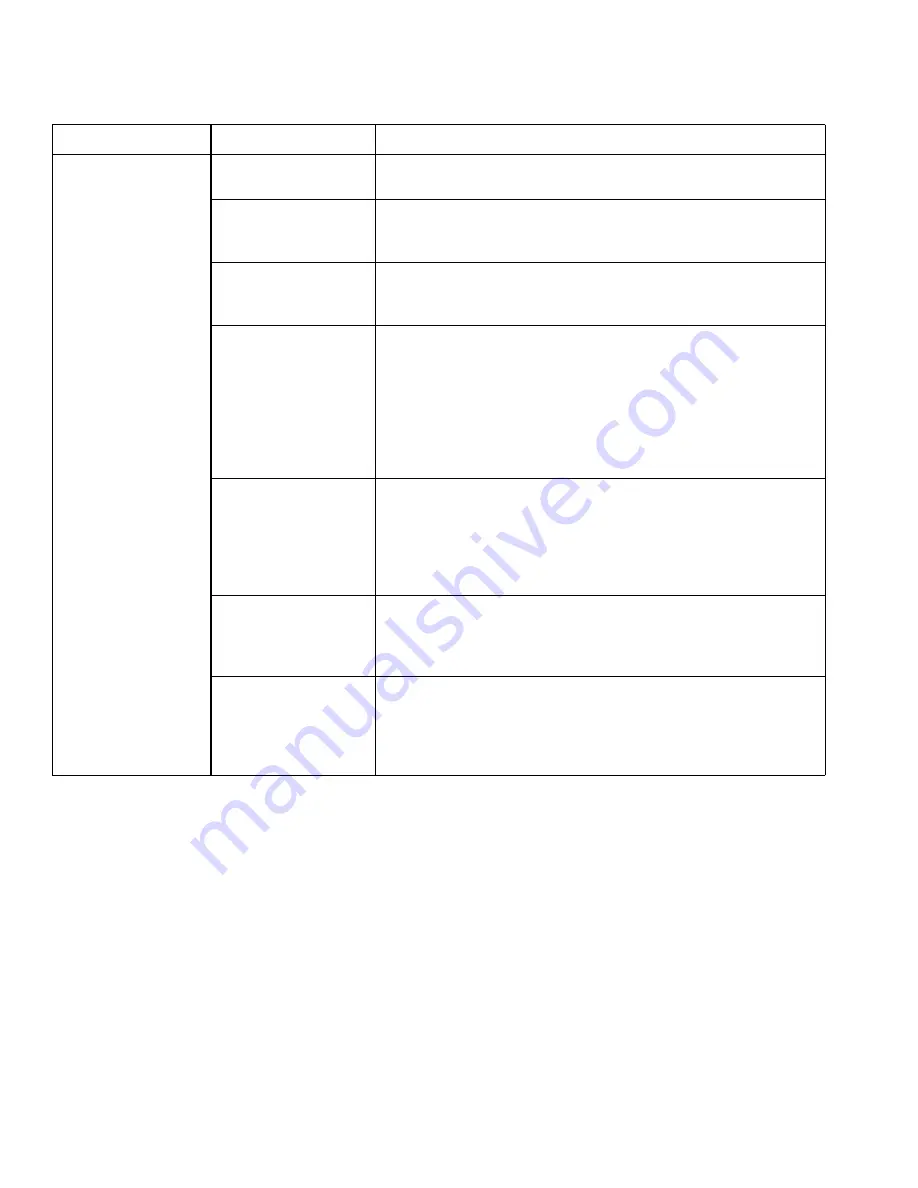
Troubleshooting
32
3A7467D
While in BLAST
mode, with the blast
control switch (B)
engaged, air is flowing
from the nozzle but
little or no abrasive is
flowing from the
nozzle.
The abrasive ball valve
is closed.
See
The abrasive metering
valve is not properly
set.
See
The pot does not have
a sufficient amount of
abrasive.
See
The pinch valve does
not open.
Engage the blast control switch (B) and check for actuation of the
pinch valve. If there is no actuation, disconnect the orange tubing
at the pinch valve. If the pinch valve opens and source air is
coming from the orange tubing, confirm that the tubing is correctly
routed. If the pinch valve does not open, replace it. If the pinch
valve opens and there is no source air coming from the tubing,
inspect the mufflers on the 4-way valve for debris. If debris is not
present, clean or replace the 4-way valve.
There is an obstruction
inside the pot or inside
the abrasive hose
between the pot and
the enclosure.
Follow
, page
12. With the abrasive hose disconnected, inspect the interior of the
pinch hose for obstructions or debris and replace if necessary (see
, page 37). Remove the tri-clamp from
the bottom of the pot. Inspect the bottom of the pot and the
abrasive hose for obstructions or debris.
The pot pressure is too
low.
With the blast control disengaged, allow the pot to pressurize and
wait for the pump to stall. If the pot pressure gauge does not reach
185 psi (12.75 bar, 1.275 MPa), see the “Unable to fill or
pressurize the pot with water” problem listed on this table.
The blast pressure is
too high.
If the blast pressure gauge reads 160 psi (11.03 bar, 1.10 MPa) or
greater, it may not be possible to achieve than 15 CPM on the
MediaTrak. This is more common with fine mesh abrasive usage.
Decrease the blast pressure to 100 psi (6.9 bar, 0.69 MPa) to see
if CMP can be increased.
Problem
Cause
Solution
Summary of Contents for 262960
Page 10: ...Component Identification 10 3A7467D Component Identification WL D WLL D 3 1 4 5 6 7 8 9 0 ...
Page 44: ...Parts 44 3A7467D EQ200T Parts WL F 1 Apply thread sealant to all non swivel pipe threads ...
Page 46: ...Parts 46 3A7467D EQ400T Parts 1 Apply thread sealant to all non swivel pipe threads ...